As The Electronics Manufacturing Industry Slowly Recovers From The Pandemic, What Can We Learn?
It doesn’t take a rocket scientist (or even an epidemiologist) to recognize that the COVID-19 pandemic has had a massive impact on the world. From the incredible strain on our healthcare systems to the rapid decline of the global economy, it is clear there was plenty out there that no one was really prepared for. As things begin to reopen, we can only hope for a smooth transition back into a somewhat normal life.
Within the realm of manufacturing, one thing is abundantly clear: supply chains are intrinsically tied and vulnerable to just about everything in our world today. Small changes in how a country interprets its laws governing raw materials can lead to rippling hiccups throughout an industry. A global pandemic can completely shut down a market and lead many of us to question what we previously took for granted.
Moving forward, things are bound to change substantially. What we learn from the pandemic and how we adapt to these new challenges will set the tone and direction for production into the future. How the electronics manufacturing industry will respond is just one of many examples.
Shutdown Ripples
The electronics industry was one that was hit pretty hard and somewhat blindsided by the impacts of COVID-19. As the initial outbreak spread through China, many electronics parts factories and manufacturing plants were shut down in order to limit the spread and protect the millions of people that could have been exposed. This had broad implications on a global scale.
As China is the central starting point for nearly every piece of technology we use today, this disruption in the supply chain was profound. Everything from cell phones to lawn mowers was impacted to some degree. Some leading electronics companies were bracing for the fallout of these delays and gently alerted consumers that certain products may begin to experience a multiple week delay.
Although much of the threat has passed in China, COVID-19 is still wreaking havoc on much of the rest of the world, with nearly 6 million confirmed cases worldwide. Many tech and finance experts believe complete disaster in the electronics supply chain has been avoided for now, and that markets will slowly begin to recover. However, the pandemic shows no sign of slowing down, and that has many watching the news with bated breath and rethinking how things are done.
Automation Focus?
One of the big-ticket items that many experienced business professionals are considering is to automate an even greater part of the supply chain. Doing so could greatly reduce the number of people that are needed to manufacture parts, reducing much of the risk and stabilizing supply lines during challenging times. The idea isn’t a bad one, as there have been multiple major disruptions over the past 25 years including the SARS outbreak and the Fukushima incident.
Introducing more uses for artificial intelligence (AI) into the supply chain could also help limit the number of hiccups along the way. For instance, AI can be used to predict market fluctuations and help gain greater insights into how customers are likely to respond to a new product. From a manufacturing-based perspective, AI can identify where there are bottlenecks in the supply chain and direct attention to safety concerns.
Just because it is a good idea, doesn’t necessarily make automation easy to implement, however. There is a relatively steep buy-in process. Converting from human labor to automation is expensive and takes a fair amount of time, so companies need to have the capital in order to make the conversion. Furthermore, the human employees that are still needed require more education in fields such as analytics and data science or even engineering and computer science.
Old Tricks and New Ideas
This disruption in the supply chain has also gotten many business leaders thinking about the damage an extended disruption could cause and how to mitigate those risks. Many companies are continuing to stockpile supplies so they have them during shortages and can sail through disruptions more or less unscathed. Others are taking a deeper look into how used materials can be refurbished and used again, cutting down the need for dependence on raw materials.
Additionally, others are taking a deeper look at how the negative aspects of globalization could impact them. COVID-19 is the case and point. The shutdown of one key manufacturing country, China, severely limited and negatively impacted the entire global technology market. Working towards localizing supply chains and moving manufacturing plants closer to where products are distributed and sold could provide some very real benefits.
Finally, even more ideas regarding workplace safety and efficiency are cropping up. COVID-19 has caused many companies to relook at how business is conducted and to evaluate if enough safe practices are in place. For example, some companies have deemed it safe to go back to work if the employees are wearing proper COVID personal protective equipment, while others are keeping as many employees as possible working from home, which isn’t always easy in the manufacturing world.
COVID-19 has had a profound impact on the electronics manufacturing world and will continue to prompt major changes into the future. Greater automation has become a major goal for many leaders who realize that humans are the limiting factor, not the technologies. Others are exploring new ideas including recycling products, stockpiling, localizing supply chains, and improving safety where possible.
Comments (0)
This post does not have any comments. Be the first to leave a comment below.
Featured Product
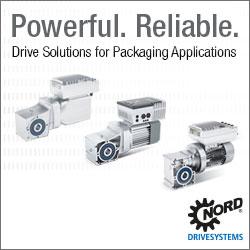