Why Siemens, GE and Rolls-Royce are turning to 3D printing
Sara Murphy for GreenBiz: As 3D printing becomes the new norm in manufacturing, many have waxed poetic about its environmentally friendly attributes, positing a green production revolution that minimizes waste.
The reality is not so straightforward. While printing parts or components on site may be environmentally preferable to some production techniques, it does not compare favorably to others in many contexts.
3D printing techniques, however, could be almost universally preferable, if industry steers in the right direction. And clear pathways exist for maximizing the technology’s green potential. A new OECD report, "3D Printing and its Environmental Implications," examines the technology’s sustainability implications and offers top priorities for policy interventions to address and improve its environmental impact. (See chapter 5 on "The New Production Revolution.") Those changes involve revisions in both printer design and operation strategies.
Green is not a foregone conclusion
3D printing, also known as additive manufacturing, is a process of making three-dimensional, solid objects from a digital file. The printer adds successive layers of material only where needed, layer upon layer, until the three-dimensional object is created. Each layer can be seen as a thin slice of the eventual object. 3D printing technologies have been around since the 1980s, but it is only in the past decade that discussion about their disruptive potential has gained traction. Data from research firm Statista sizes the 3D printing market at about $8.8 billion in 2017, with revenue projected to reach $16 billion by 2019.
Despite many people’s assumptions, 3D printing is not inherently greener than other manufacturing methods. In fact, it includes many methods of printing, most of which cause worse impacts than injection molding of plastic at scale, because 3D printing consumes more energy and often generates more waste. On the other hand, 3D printing manufacturing techniques usually have a smaller environmental footprint than machining. Full Article:
Comments (0)
This post does not have any comments. Be the first to leave a comment below.
Featured Product
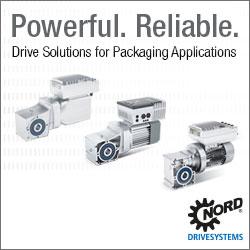