A New Boeing Patent Describes Levitating 3D Printing
By Lindsey Kratochwill for Popular Science: Watching a 3D printer work can sometimes seem like magic--thin filaments slowly build up on top of a platform, turning into parts and figurines. Now, apatent published by aerospace company Boeing introduces an even more futuristic element: levitation.
With this method, the object prints while floating in midair thanks to magnets or acoustic waves. A "nugget" or base gets printed first out into space, and then a cadre of 3D printers add more and more of the printing material.
But why? Levitation is cool, yes, but it turns out there is also a practical purpose for a floating 3D printed object, at least according to Boeing's patent. The levitating object can be manipulated and turned more so than an object stuck to a platform can be, and using many printheads at the same time would ostensibly speed up the process. Cont'd...
Comments (0)
This post does not have any comments. Be the first to leave a comment below.
Featured Product
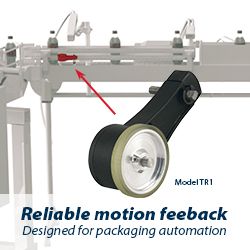