Visco-elastic Technology: A Monolithic, Amorphous Coating Transforming Pipeline Protection
By: Edwin Welles, Vice President - Viscotaq
Introduction: The Critical Role of Pipelines
Pipelines play a critical part in supporting our way of life. In the USA alone there are a total of 3 million miles of natural gas pipelines1, and 2.2 million miles of water pipelines2 supporting the infrastructure to fulfill our demands in basic functions we take for granted daily such as available energy and water. The infrastructure is aging, however: for example, over 50 percent of the pipelines were built in the USA 40 years or longer ago. Without coatings and cathodic protection systems, the majority of this infrastructure would have to be replaced by now. The cost to rebuild pipeline networks would be astronomical; that is why companies and governments invest in protecting their pipelines to extend the life of these assets as long as possible.
The Growing Market for Pipeline Coatings
The total market globally for pipeline coatings was valued at 8.4 billion dollars in 2024 3 and is expected to grow to 15.1 billion dollars by 2033 3. New technologies such as Visco-elastic coating systems have established markets in niche areas within this industry such as replacing or repairing old pipe coatings, coating weld seams at new pipeline projects and coating transitions between underground and aboveground pipelines (soil-air interface). Market share and revenues have grown rapidly over the past two decades and are expected to keep growing due to the versatility, easy application, cost savings, and technology awareness by a broader audience. This article will help explain the benefits and the cost savings this technology has brought to the market.
The Evolution and Innovation of Visco-elastic Technology
2.a. History
Originating from a waterproofing concept, Visco-elastics were designed to stop water on a molecular level. Corrosion cannot occur without water, not even microbiological incurred corrosion (MIC).
The elimination of water on a molecular level is the essential concept of the Visco-elastics and was developed in the 1990s with support of a major gas and oil company in the Netherlands. After trials and long-term testing, confirming the proof of concept, the products went to market. Multiple patents were granted to different manufacturers over the years. In 2016, international standards such as the International Standards Organization (ISO) added this successful technology giving credibility and setting minimum requirements for the products on the market and for any new products to come. Currently standards such as ISO 21809-3:2016, ISO 21809-11:2019, AWWA C232:2022, NACE SP 0109:2019 and CSA Z45:32 have been in place to safeguard the technology and to assist end users with its use.
2.b. Bonding on a Molecular Level
The polymers of a Visco-elastic coating adhere by van der Waals bonding and have a continuous wetting effect on the surface. The distance between the coating polymers and the steel substrate is extremely small (10-9 m) as van der Waals bonding occurs on a molecular level between the two materials (electron affinity/interaction). Examples of other materials that show wetting and van der Waals bonding on a substrate are oil and grease: they are well bonded and without a solvent, they are very difficult to remove from the surface. Figure 1 shows a microscopic image of a visco-elastic product adhering to the surface via van der Waals bonding, demonstrating the close interaction of the coating and the substrate.
Due to a low surface tension, Visco-elastics adhere to steel, and most common materials (PE, PP, Bitumen, Epoxy, Urethanes, Coal Tar) used in the industry, creating a seamless transition and are therefore easily integrated into existing pipeline networks.
2c. Monolithic Self-Repairing Coating
Unlike oil and grease, Visco-elastic coatings present both liquid behavior and rubbery behavior, carefully designed, to fulfill coating functionality. The design allows for unique features such as self-repair (Figure 2) when indentations or even small damages occur, and an easy application creating a smooth, monolithic layer, conforming itself entirely to the substrate without any stress.
An example of the manual application of a Visco-elastic coating on a large pipe surface with spiral welds demonstrates excellent coverage (Figure 3). The coating conforms perfectly to the surface, bonding on a molecular level, which prevents water molecules from penetrating. This results in a monolithic layer with complete adhesion, ensuring the coating is entirely watertight. Such applications often undergo rigorous testing, such as peel strength tests following standards like ISO 21809-3:2016.
The unique properties of a Visco-elastic coating are nowadays included in the minimum requirements of various international standards and specifications of leading oil and gas, utility and water companies. The recognized, successful technology with its unique properties and benefits established itself over the past decades and demand is growing rapidly due to the ability to have new solutions for pipeline owners and to replace older, traditional coating systems with a longer lasting, easy to apply, and clean coating system. Traditional systems such as tapes and shrink sleeves require most often a higher level of surface preparation and may require primers, while installation is more sensitive to application errors. Shrink sleeves are applied by heating the product with for instance a torch, while tapes are applied under tension (preferably with a machine). Besides safety concerns, the applications are therefore more sensitive which may result in disbondment and overlap issues. Liquid coatings such as epoxies or polyurethanes often need a perfectly clean surface (SSPC 10), are sensitive to humidity and temperature changes, and require drying time. Visco-elastics address this by an easy-to-apply conforming inner layer (hand-applied with no tension) with lower surface preparation requirements (SP-2/SP-3), while having no primers, solvents or drying time. The easy, safe and clean application creates a better environment to do a proper installation of the coating and minimizes risks of failures. Visco-elastics are compatible with existing and previous line pipe coatings such as coal tar, 3LPE, 3LPP, urethanes, bitumen, etc.. Visco-elastics have many advantages for in the field applications such as pipe coating rehabilitation, pipe crossings, soil to air interfaces, field joints (girth welds) both on- and offshore, t-s and elbows, and more.
Case Histories
Gulf Coast Countries (GCC) such as Saudi Arabia, United Arab Emirates and Oman are faced with aggressive soil (Sabkha soil) in the coastal areas: due to tide, sea water sometimes travels over a mile inland, depositing salt and sulphuric compounds into the desert sands, creating a wet and dry cycle. The salinity concentration of the top surface may reach over 30% (which represents concentrations of salt present in dust) while the brine salinity of the water table can go as high as 18 %. Lab testing according to international standards utilizes salt concentrations similar to sea water (3%), therefore not representable for circumstances like these.
During application, a sandblasted clean pipe can be contaminated with salt by flying dust within hours. Coatings sensitive to osmosis will not survive, while surface preparation requirements limit many coatings in the market. End users prefer long term trials to qualify coatings for these regions. In 2011, a Visco-elastic coating (Viscotaq) was applied on a 42 inch main line and inspected after 15 months. The coating remained in excellent shape, there was no corrosion and no disbondment observed at the inspection. Figure 4 represents an image taken during application: salt crust, water table and intermediate soil area are clearly visible. The inspection results after 15 months showed not only complete adhesion on the surface but also the uniform, continuous behavior of the coating (with no overlaps present, forming a single, cohesive layer). Visco-elastics have proven to be successful and have saved end users in the GCC region tens (if not hundreds) of millions of dollars in repairs and maintenance.
Another long term review of applied coating showed excellent performance of a Visco-elastic in aggressive clay areas where the elastic component (rubbery behavior) allowed for resilience against shear. After installation in 2012 on various diameters of pipelines running at an operating temperature between 40 and 50 degrees Celsius, inspection took place after two years: (Figure 5) no corrosion was observed, 100% adhesion and consistent thickness readings at various clock positions. Note that the Visco-elastic type of coating was the semi-solid technology having added benefits in these circumstances, which is discussed in the next paragraph.
The coating rehabilitation program continued for a number of years and the end user was able to improve their integrity system saving millions of dollars in recoating programs. No recoating was ever needed up to date and compared to their traditional system (which showed deterioration sometimes even after five years), the service-life has been close to tripled by choosing a Visco-elastic system. Currently the coating is in mint shape and continuous to add beneficial years of service free of charge each year.
Summarized, many clients globally have saved millions of dollars over the past decades profiting from the benefits of the Visco-elastic technology where most importantly their assets are preserved, reliably extending service-life with a clean, easy to apply, long term solution.
Technological Advancements
Even though the visco-elastic technology is seen as relatively new, it has been on the market for 30+ years. In 2009, a new improved visco-elastic coating was developed (Viscotaq), improving stability at elevated temperatures and at vertical applications, and adding more resilience to soil stress and other mechanical influences. Unlike existing visco-elastics, which are more or less semi-liquid, and therefore more dynamic, Viscotaq came with the concept of a semi-solid advancement allowing for more stability to prevent sliding at verticals, and differences in thicknesses over time at elevated temperatures. Additionally, the proprietary patented polymer formulation shows high stability by semi-solid behavior up to 130 degrees Celsius and more resilience against mechanical influences such as soil stress caused by movement of the pipe (temperature expansion, movement after installation).
Current Limitations of Visco-elastic Coatings and Future Developments
Visco-elastic coatings are mostly hand-applied which makes the technology ideal for in the field applications. Applications are limited to stretches of pipe rather than coating an entire (new) pipeline. New developments by Denso however have made it possible to supply the market with a cost effective, long-term line pipe coating for the oil and gas, water, and off-shore industry (Figure 6). Previously, high temperature applications (above 95 degrees Celsius) were a limiting factor. Since they have become of more interest to end-users, visco-elastic systems such as the Viscotaq XHT system were developed over the past years to meet this demand and are currently commercially available and in service by leading oil companies.
Conclusion
Visco-elastic coatings offer the industry an innovative, new approach in solving corrosion problems, combining advanced polymer technology with practical benefits like durability, cost savings, and environmental sustainability. As industries incorporate these innovations, pipeline networks are better protected, creating a safe and reliable infrastructure. Whether in oil and gas, utilities or water, visco-elastic coatings have a transformative impact on pipeline integrity management for generations to come and benefit the industry and our way of life as a whole.
References
Natural gas pipelines - U.S. Energy Information Administration (EIA)
Water Infrastructure | ASCE's 2021 Infrastructure Report Card
Pipe Coatings Market Size, Share & Analysis 2033 Report
Featured Product
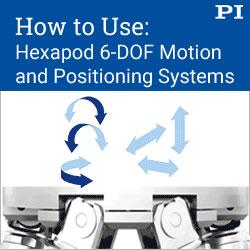
PI USA - Hexapod for Industrial Alignment
This new compact 6-axis hexapod was designed with 24/7 industrial precision alignment tasks and easy serviceability in mind. It is equipped with absolute encoders (no need for referencing) and motor brakes that automatically engage during a loss of power, for extra safety. Debuting at Photonics West 2025 last month, applications include camera lens alignment, micro assembly, and fiber optical alignment applications.