PMMA Machining: A Comprehensive Guide
Polymethyl methacrylate (PMMA), commonly known as acrylic or acrylic glass, is a widely used thermoplastic material known for its excellent optical clarity, weather resistance, and versatility. It is often used in a variety of applications, from automotive to medical devices, and is a popular choice for CNC machining due to its easy processability and superior finish. In this post, we'll dive into the essential aspects of PMMA machining, including its properties, machining techniques, and best practices for achieving high-quality results.
What is PMMA?
Signage and displays: Its clarity and ability to withstand outdoor weather conditions make it a popular choice for billboards and illuminated signs.
-Automotive parts: PMMA is used for parts like headlights, taillights, and windows due to its optical clarity and impact resistance.
- Medical devices: It's used in medical applications such as prosthetics, surgical tools, and diagnostic equipment.
- Aesthetic and decorative items: Acrylic's ability to be easily molded and colored makes it ideal for creative designs.
Given its versatile range of applications, PMMA machining is an essential process for transforming this material into specific shapes and sizes for use in various industries.
PMMA Machining Process
PMMA is a relatively easy material to machine, though it does require specific considerations to ensure the desired quality and finish. CNC machining, including CNC milling, turning, and drilling, are the most commonly used methods for shaping PMMA. The machining process typically involves the following:
CNC Milling
CNC milling involves the use of rotating cutting tools to remove material from the PMMA workpiece. Milling machines allow for the creation of precise cuts, such as slots, holes, or complex 3D contours, making it ideal for high-precision machining of acrylic components.
Best practices for CNC milling PMMA:
- Use sharp cutting tools: Dull tools can cause excessive heat build-up and lead to chipping or cracking of the material.
- Lower cutting speeds: PMMA is prone to melting under high-speed conditions, so using slower feed rates and cutting speeds is essential for a smooth finish.
- Use coolant: Using an appropriate coolant or air stream helps control the temperature during the machining process and prevents the material from overheating.
CNC Turning
CNC turning is ideal for creating cylindrical shapes or features like threads or grooves in PMMA. This process involves rotating the workpiece while a stationary cutting tool is used to remove material.
Best practices for CNC turning PMMA:
- Slow spindle speeds: Like milling, using a slower spindle speed will help prevent melting or surface distortion.
- Avoid excessive cutting forces: Heavy cutting forces can lead to cracking or uneven surfaces, so it's important to keep forces within manageable levels.
- Finishing techniques: After machining, a light abrasive finishing or polishing process may be required to achieve a smooth and glossy surface.
Drilling
Drilling is commonly used for making holes in PMMA. This process can be tricky because excessive heat generated during drilling can cause the material to crack or burn.
Best practices for drilling PMMA:
- Use specialized drill bits: Choose drill bits that are designed specifically for acrylic to reduce the likelihood of cracking.
- Low speeds and steady pressure: Apply consistent, low speeds and light pressure to ensure a clean hole and prevent the drill bit from catching the material.
- Coolant application: Just like in milling and turning, using a coolant (or even just air cooling) can help manage the heat and avoid damaging the material.
Challenges in PMMA Machining
While PMMA is a relatively easy material to machine, there are a few challenges that manufacturers need to consider to ensure the best possible results:
Heat Generation
One of the biggest challenges when machining PMMA is heat generation. The material is sensitive to high temperatures, which can lead to melting, warping, or cracking. This is especially important when using CNC milling and turning. Proper feed rates, cutting speeds, and coolant use are essential to prevent thermal damage.
Chipping and Cracking
Due to its brittleness, PMMA is prone to chipping and cracking during machining. This can be particularly problematic when making fine cuts or working with thin sheets of acrylic. To reduce chipping, ensure that cutting tools are sharp and that feed rates are appropriate.
Surface Finish
While PMMA is known for its optical clarity and aesthetic appeal, achieving a high-quality surface finish during machining can be challenging. The material's tendency to scratch and smudge means that extra care must be taken to avoid damaging the surface. Additionally, post-machining polishing or buffing may be required to achieve the glossy finish that PMMA is known for.
Advantages of PMMA Machining
PMMA offers several advantages in the CNC machining process, making it a highly sought-after material for a range of industries:
Excellent Optical Clarity
PMMA is often used when clarity and transparency are crucial, as it allows up to 92% light transmission. CNC machining allows for precise adjustments, making it possible to create components that are both functional and aesthetically pleasing.
Lightweight
Despite its glass-like appearance, PMMA is significantly lighter than glass, making it a more practical option for many applications, especially in industries like automotive and aerospace.
Durability and Resistance
PMMA is resistant to weathering and UV light, making it an ideal material for outdoor applications. It also has a high impact resistance compared to glass, making it safer in many environments.
Ease of Machining
PMMA is relatively easy to machine compared to other plastics and metals, which allows for more flexibility in design and a faster production process.
Applications of PMMA Machining
PMMA's versatility makes it suitable for a wide range of applications across different industries:
- Automotive: PMMA is used in headlights, taillights, and window components due to its durability, UV resistance, and optical clarity.
- Aerospace: In aerospace, PMMA is used for cockpit windows, lighting systems, and as a lens for navigation equipment.
- Signage and Displays: PMMA is widely used in the creation of illuminated signs, display cases, and protective covers due to its clarity and ease of shaping.
- Medical Devices: PMMA is used in medical devices like prosthetics, lenses, and diagnostic tools due to its biocompatibility and transparency.
- Consumer Products: PMMA is used for eyewear lenses, furniture, decorative items, and even in the production of CDs and DVDs.
Conclusion
PMMA machining offers a unique set of benefits for a wide range of industries, from automotive to medical devices. With the right equipment, techniques, and careful attention to factors like heat generation and material brittleness, manufacturers can achieve high-quality results in terms of both function and appearance. Whether for prototyping or full-scale production, CNC machining offers precise, efficient, and customizable solutions for working with PMMA.
By following best practices and selecting the right machining processes, manufacturers can ensure the successful fabrication of complex acrylic components for various applications.
Featured Product
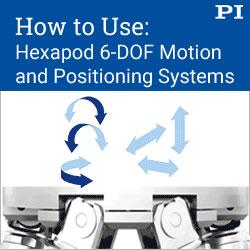