Essential Warehouse Safety Checklist: Protecting Your Team and Inventory
Maintaining safety in a warehouse is vital for employee protection. Regular inspections using a checklist help identify hazards. Key areas include building integrity, lighting, safe material stacking, equipment maintenance, ventilation, fire safety, and cleanliness.
If you manage a warehouse, you already know that keeping safety standards high is essential. You may even have your own safety rules and guidelines in place to protect both your team and your inventory.
Part of that responsibility is making sure your warehouse remains a safe place to work. To help maintain this, regular inspections using a warehouse safety checklist can be a valuable tool.
According to OSHA, around 5 out of every 100 warehouse workers experience injuries each year, many of which could be avoided with improved working conditions—conditions that routine inspections can often catch.
A safety inspection checklist can help identify potential hazards and give you the chance to address them early on. Wondering what to include in this checklist and how to use it for thorough inspections?
Keep reading as we walk you through the essentials for your warehouse inspections.
What Should You Check in the Warehouse Inspection?
When inspecting a warehouse, make sure your checklist includes the following:
1. Inspect the Building and Location for Damage
Begin by thoroughly reviewing the structure, including windows, floors, doors, ceilings, and walls. Check for cracks, leaks, broken windows, or any signs of wear that might need repair. Look for water damage on ceilings and walls, which could indicate leaks or structural problems. Make sure doors and windows open and close smoothly and securely, as issues here could impact safety or security. Take notes on any areas that need attention, so repairs can be planned before issues worsen.
2. Check Warehouse Lighting
Good lighting and well-maintained electrical components plays an important role in keeping the warehouse safe. All areas, including workstations, hallways, fire exits, loading docks, offices, lunchrooms, and even bathrooms, should have proper lighting.
Poor lighting can make it hard for workers to move around safely, increasing the risk of accidents. Regularly checking and maintaining the lights helps create a safer and more functional workspace for everyone.
3. Review Material Stacking Practices
Review how materials are stacked and stored throughout the warehouse. Improper stacking can lead to items falling or shelving units collapsing, which poses serious safety risks. Ensure that materials are arranged securely and are not leaning or unbalanced. Employees should follow proper stacking practices, keeping heavier items on lower shelves and lighter ones on top. Verify that shelving or racking systems are not overloaded and stay within their load limits. Regularly remind staff of these guidelines to prevent accidents and maintain a safe work environment.
4. Regular Equipment Inspections
It's important to schedule regular maintenance and check-ups for warehouse equipment to keep everything running smoothly and avoid unexpected issues. Inspections should cover items like forklifts, ladders, shelving, and other tools to catch signs of wear and tear or identify any bigger problems before they become serious. Keeping track of these checks with inspection logs and tags ensures that no equipment is overlooked and that everything stays in safe working order.
5. Check Ventilation
Working in a packaging warehouse often involves dealing with a lot of dust, which can affect the air quality. Proper ventilation is essential to ensure workers have a safe and healthy environment. Make sure the ventilation systems are functioning well to keep the air clean and reduce potential health risks.
6. Review Fire Safety Measures
Fire safety is crucial in any workplace, especially in a setting where materials and equipment can increase fire risks. Check if fire extinguishers are available and placed where they are easy to access. Inspect sprinklers, fire hoses, and alarms to ensure they are in good working condition. If chemicals are stored on-site, assess the risk of explosions and take precautions to prevent fires from spreading to those areas. Regular checks and maintenance can make a significant difference in preventing accidents.
7. Focus on Cleanliness and Hygiene
While it can be challenging to keep everything spotless in a busy warehouse, it's still possible to clear out unnecessary clutter and waste that might cause tripping or fire hazards. Regularly tidying up work areas, removing debris, and organizing materials can make a big difference. Additionally, make sure that break rooms, bathrooms, and workstations are kept clean and hygienic for the well-being and comfort of all employees.
Closing Thoughts
Maintaining a safe warehouse is an ongoing process that requires attention to detail and regular checks. A well-thought-out safety checklist can help you catch issues before they lead to problems, protecting both your team and your operations. By staying proactive and addressing hazards early, you create a safer and more efficient environment for everyone.
Featured Product
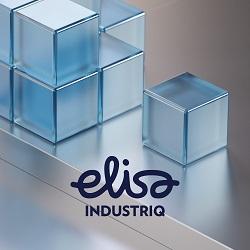
Supply Chain Management by Elisa IndustrIQ
Elisa IndustrIQ's Supply Chain Management (SCM) solution is designed to enhance productivity, efficiency, and effectiveness throughout the entire supply chain. This advanced solution focuses on improving flexibility and responsiveness in both planning and operation execution, crucial for adapting to rapidly evolving markets. Our solution facilitates business growth by offering end-to-end visibility, essential for efficiently managing and streamlining supply chains. Key features include AI-powered demand forecasting, automated quoting and purchasing, intelligent replanning capabilities, structured collaboration tools, and direct supplier integration. These features can be tailored to align with your business and financial objectives, adding a strategic dimension to sales and operations planning and execution. The solution is designed to meet the manufacturing industry's needs for speed, resilience, and efficiency, primarily through innovative approaches to reduce business friction.