Game-Changing 3-D Woven Thermal Protection System Technologies Support NASA Space Missions
Patented materials provide a new level of protection for spacecraft and crews By Sarah Minhas, Bally Ribbon Mills
3-D weaving offers significant benefits over other options
Bally Ribbon Mills has been working to develop 3-D weaving since the company received a research contract from the United States Air Force Research Laboratory (AFRL) to develop the technology in the early 1990s. Alterations to existing looms ultimately led to the creation of a fully automated 3-D loom, which could create orthogonal, isotropic, and quasi-isotropic composites, as well as near-net-shape and complex net shape preforms. The looms have since been used to fabricate 3-D woven composite structures for the aerospace, automotive, construction, military, and safety industries.
"3-D weaving is an emerging technology that offers a variety of benefits over both two-dimensional (2-D) composite production and more traditional building materials, like steel and aluminum," says Curt Wilkinson, BRM's Senior Textile Engineer. "Compared to traditional 2-D fabrics, 3-D weaving reduces weight, eliminates delamination often experienced with 2-D fabrics, reduces crack risks, and lowers production time. 3-D fabrics also offer direct and indirect manufacturing and operational cost reductions."
New materials needed for strong and robust compression pads
A TPS protects a spacecraft from harsh heating. TPS materials are typically thermally robust, low-density insulators that are somewhat fragile. For the human-rated Orion vehicle, some crucial parts of the TPS need to be extremely strong as they are part of the vehicle structure. After the Orion's 2014 Exploration Flight Test-1 (EFT-1), engineers determined that the existing materials used as the structural ablator would not work for future missions beyond low Earth orbit. The 2-D carbon phenolic material used for the EFT-1 compression pads has relatively low interlaminar strength and requires a metallic shear insert to handle structural loads.
There were few options for materials that can meet the load demands of lunar return missions due to performance or part size limitations, so NASA began looking for a TPS technology tailored to the specific and unique needs of missions with human rated spacecraft. NASA's Orion/Artemis mission is preparing for sending humans into deep space - with the ultimate goal of putting astronauts on Mars in the 2030s.
NASA began considering the use of 3-D weaving technology for the Orion Multi-Purpose Crew Vehicle (MPCV), which uses compression pads that serve as the interface between the crew and service modules. The multiple pad locations in the heat shield serve as a part of the mechanism for holding the crew and service modules together during most mission phases prior to separation, followed by the crew module's Earth reentry. The compression pads must carry the structural loads generated during the two modules' launch, space operations, and pyroshock separation, and then serve as an ablative thermal protection system that can withstand the high heating of Earth reentry.
Dr. Jay D. Feldman, a Research Materials Engineer at NASA Ames Research, has been leading the development and design of heat shield materials for more than a decade and had been exploring and developing new approaches. He became aware of Bally Ribbon Mills' capabilities to perform 3-D weaving of composite fabrics to produce complex, single-piece structures that are strong and lightweight, and began working with the company to explore use of their technology and expertise. Starting by touring the BRM factory to meet with technical experts and researchers, Dr. Feldman brainstormed on how to take the 3-D weaving technology and use it for the NASA heat shield application. Talking face to face helped NASA understand what could be done with 3-D weaving and 3-D braiding to make complex shapes and combinations of materials and weave designs required for their needs.
After initial exploratory work proved promising, BRM received additional funding and began working on what eventually became the patented 3-Dimensional Multifunctional Ablative Thermal Protection System (3D-MAT). The project combines the 3-D weaving of quartz yarns with resin transfer molding to develop a robust multifunctional material architecture capable of meeting both structural and thermal performance needs for lunar return and beyond. The material is made by 3-D weaving quartz yarns and infusing them with a cyanate ester resin. BRM's 3-D orthogonal weave with high fiber volume showed a 900 percent increase in tensile strength in the z direction, and the resin infusion fully densified the material so there are no pores, which locked in the strength and robustness.
The 3D-MAT project is led by NASA'S Ames Research Center with many partnerships, including BRM and NASA's Johnson Space Center (JSC), where the resin infusion takes place. Mechanical testing of the 3-D composite took place at Southern Research Institute, NASA's Langley Research Center, and JSC. The primary funding source for the project was the Game Changing Development (GCD) Program, which investigates ideas and approaches that could solve significant technological problems and revolutionize future space endeavors. GCD projects develop technologies through component and subsystem testing on Earth to prepare them for future use in space. The 3D-MAT project team is well integrated with the NASA and Lockheed Martin Orion teams to assure development meets the MPCV needs.
Collaborative iterative process provides major disruptive breakthrough
NASA began by providing BRM with detailed requirements on such items as fiber volume and fiber percentages. BRM then suggested a preform weave and design - at the time it was four times larger than the largest preform ever woven at BRM. Development required significant equipment modification and procurement of a new Jacquard loom harness design to individually control 5000 yarns.
The project was the first achievement of continuous, automated 3-D orthogonal weaving at large scale (12-inch x 3-inches) and high fiber volume (60 percent). It features a cross section that is 4 times larger than the prior state of the art, making the fabric a major disruptive breakthrough. The project also resulted in a game changing innovation in resin infusion, with full resin densification of large 3D preforms established for the first time (<1 percent porosity). This maximized the strength of the 3D-MAT composite, at a factor of 12 times thicker than the prior state of the art for full densification.
"NASA and BRM conducted a design review where top engineers from across the country converged," addedWilkinson. "Brilliant minds collaborated, solving complex physics problems on the spot, which was nothing short of awe-inspiring. Being part of that dynamic group was incredibly exciting and a truly memorable experience."
The combination of materials and architecture result in an extremely high-performance composite. Compared to the 2D carbon phenolic used on Orion EFT-1, 3D-MAT is 9 times stronger in tensile strength (z); 3 times stronger in shear strength; and 25 percent lower in thermal conductivity.
BRM processed the raw material, set-up the loom and wove the material, supplying it to NASA. Development partner San Diego Composites worked with NASA to develop the infusion process. NASA then tested the 3D-MAT composites and Lockheed Martin, NASA, and BRM developed material specification and a process control document.
The heat shield compression parts are doing double duty, serving as multi-functional material that must be light and strong to connect the two modules in a structural way while also managing heat. Says Wilkinson, "Using an iterative process trying different ways to make the weave work with two layers, BRM came up with the right solution - 3D-MAT - an elegant and intricate system in which the two functions are integrated into one weave that provides the necessary materials and architecture."
The patented material fit the need and was immediately folded into the mission, performing flawlessly on Artemis-1; it is now classed as an operational flying technology. Lockheed Martin is using 3D-MAT for a variety of items in the Orion crew module, including 10 umbilical pad parts, 2 skid pads, 6 launch abort system and crew module release mechanism pads, 1 hatch bumper pad, 4 outer compression pads, and 4 inner compression pads.
Wilkinson explains that working with NASA using BRM's 3D weaving capabilities to help modernize the TPS for the Orion spacecraft was a fun and collaborative experience that was extremely positive for everyone involved. BRM also enjoyed working with NASA to teach them more about the weaving technology so they can make better systems. BRM even organized a small group 3-D weaving 101 class to teach the technology to the project team, along with an extended group from NASA Ames and other NASA centers.
The 3D orthogonally woven 3DMAT Quartz Material for the Orion MPCV compression pads was named the 2023 NASA Government Invention of the Year. Wilkinson concludes, "BRM is a great example of an American family-run business with a unique specialized technological capability that will further NASA's current and future exploration plans."
Development of more sustainable 3-D woven heatshield
BRM also worked with NASA on a material designed to meet NASA's needs for TPS technology for planetary science missions with very high heating entry environments. The material must protect the vehicle from high heating as it enters the atmosphere at high velocity.
Looking to develop a system that would manage heat while avoiding some of the sustainability challenges related to heritage TPS like those composed of carbon phenolic, NASA worked with BRM and other partners to develop a new mid-density 3-D woven dual layer carbon phenolic. The material, which was ultimately dubbed Heatshield for Extreme Entry Environment Technology (HEEET), is designed for use on vehicles with base diameters ranging from <1 meter - >3.5meters.
HEEET features a 3-D dual layer-to-layer weave. The outermost layer manages recession. It is a higher density all carbon fiber weave, exposed to the entry environment. The innermost layer is an insulation layer that manages the heat load. This lower density layer offers a lower thermal conductivity and is composed of blended carbon/phenolic yarn. The two layers are integrally woven together; they are mechanically interlocked but not bonded. The woven material has medium density phenolic resin infusion, with a higher phenolic loading than the standard phenolic-impregnated carbon ablator (PICA) and open porosity.
The most challenging part of HEEET development for heatshields was the need for seams between the woven tiles due to weaving width limitations. To solve the problem, the team designed a gap filler between tiles to provide structural relief for all load cases by increasing compliance in the joint and to provide an aerothermally robust joint.
Two factors inherent to the HEEET material and its mission applications drive the system seam requirements. Aerothermal environments for HEEET mission architectures require minimization of unsupported adhesive joint widths to prevent runaway failure at the seam. Also, as the carrier structure deflects, the HEEET architecture must have sufficient compliance to maintain compatibility with the carrier without inducing excessive stress in the system. HEEET material characteristics enable spacecraft to endure the highest heating environment that NASA missions experience.
3-D weaving used in HEEET is efficient and uses less mass for a heat shield than heritage materials. The material is twice as efficient for most missions at as much as half the mass, depending on application specifics.
In addition, HEEET is replacing the commonly used heritage fully dense carbon phenolic resin system, a type of plastic that has flown in NASA Galileo missions to Venus and Jupiter. That system is inefficient and uses raw materials that are no longer readily available and are even considered toxic to manufacture. In HEEET, NASA researchers found a way to enable high heating using materials that have more modern properties, are more available, less toxic, and are based on modern manufacturing processes.
Exciting future for 3-D woven materials
NASA's investment in 3-D woven TPS has resulted in the successful development of materials scheduled for use in numerous current or planned space missions. What is more, many new products were enabled by processes created as part of 3D-MAT development, including hypersonic vehicles and defense, Formula 1 race car structural parts, security from explosives/ threat mitigation unit, composite overwrap pressure vessels, mortar baseplates, and rocket motor casings.
For more information, visit www.ballyribbon.com
Featured Product
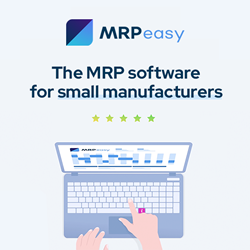
MRPeasy - ERP for Small Manufacturers That Delivers Results
Always know what you have in stock and what you'll need to fulfill orders. Never forget to order parts on time or fail to notice a late delivery from your vendor. Easily create manufacturing orders and schedule them automatically according to resource availability or delivery deadline. Generate accurate cost and lead time estimates and provide customers with quick quotes. Receive notifications when orders are late or inventory levels reach a critical point. Ensure seamless communication between sales, production, warehousing, procurement, administration, and finance. Integrate with popular accounting, CRM, and e-commerce apps. MRPeasy is an ERP software for small manufacturers that gives you all that and more. Our users report a 54% average improvement in the overall performance of their business and a 42% increase in on-time deliveries. Try for free, no credit card needed.