Renishaw helps Tronosjet Manufacturing achieve FAA certification
These include an engine thrust control pulley bracket — one of the first additively produced metallic parts to be certified by the Federal Aviation Administration (FAA) under its Parts Manufacturer Approval (PMA) scheme.
When Tronosjet Manufacturing wanted to boost its additive manufacturing (AM) capabilities and achieve regulatory compliance for its metallic aerospace parts, it turned to global engineering technologies company Renishaw for support. Renishaw supplied multiple laser powder bed fusion (LPBF) AM systems, which Tronosjet uses to produce various aircraft components. These include an engine thrust control pulley bracket — one of the first additively produced metallic parts to be certified by the Federal Aviation Administration (FAA) under its Parts Manufacturer Approval (PMA) scheme.
Background
Founded in 2001, Tronosjet is a Canadian aircraft leasing, major modification and aircraft maintenance provider. Historically the company has owned and managed a fleet of over 60 BAe 146/Avro RJ aircraft, including engines and spare parts on behalf of third parties.
In 2016, the company founded its advanced manufacturing division, established to use AM to produce different aerospace components for its customers. As part of its AM service, its team designs, prints, heat treats, post-processes and metallurgically tests parts to deliver qualified components along with the required certification data. Its manufacturing facility carries approval as an Aerospace Manufacturing Organisation under Transport Canada 561, along with AS9100 approval for design and development.
Although more manufacturers are starting to use AM to produce aerospace components, very few components have received regulatory approval from the FAA — preventing customers from flying them. To demonstrate the capability of AM production, Tronosjet selected a BAe 146 part to produce using AM — a cast magnesium engine thrust control pulley bracket that suffers from corrosion. The bracket holds a pulley, which redirects engine cables that travel from the cockpit to the pylon connecting the engine to the airframe. Statically, the bracket is usually loaded with 60-100 lb of tension from the cable.
"The thrust control pulley bracket was determined by the FAA to be a Class 1 (critical) part, essential for the safety of the aircraft," explained Jeff Campbell, Director of Maintenance and Manufacturing at Tronosjet Manufacturing. "We knew that additive manufacturing could provide the required strength and that having our new bracket certified by the FAA would validate the use of additive in aerospace production."
Challenge
With AM still a relatively new technology, Tronosjet knew it would need to demonstrate the quality, strength and reliability of printed parts to the FAA and its regulatory groups, comprised of material scientists, aerospace engineers and other airworthiness specialists.
"Over the years, we have communicated with the FAA many times on different projects, and we understand how it works as a regulatory body," added Campbell. "This gave us an advantage because we knew what to expect. We knew that we'd need to prove the bracket's safety using tensile, fatigue and non-destructive testing (NDT) and to show that it wouldn't degrade over time."
As well as proving that the bracket could pass NDT , tensile and fatigue testing, Tronosjet needed to demonstrate the repeatability of the titanium alloy and its manufacturing process. Therefore, it required a high-quality AM system that could produce complex metallic components and instill confidence with the regulators in the company's production team. At this point, it turned to Renishaw.
Solution
"Our relationship with Renishaw goes way back, and we first came to the UK to meet with its CEO in 2018," added Campbell. "The reason we decided to go for a Renishaw system is the brand - it's a trust marker and we knew it was a company that offers excellent engineering and process capability. Its RenAM 500 series are world-class AM machines, and of the quality we needed to achieve FAA certification. Also, we were impressed with Renishaw's presence across North America, and its local support was important for us as a small business taking on new technology."
Over time, Tronosjet purchased three RenAM series machines from Renishaw — the AM250, the 500S Flex and the 500Q. All use LPBF for metal component volume production and have a build volume of 250 mm x 250 mm x 350 mm. The AM250 and RenAM 500S Flex are both single-laser machines, while the RenAM 500Q is a four-laser system, with the latter offering automatic powder recycling.
To produce the thrust control pulley bracket, Tronosjet chose the AM250, which can produce complex metal components directly from computer-aided designs (CAD) models using materials including titanium, aluminum and nickel. It chose this system because the AM250 can produce parts with the high material properties expected by the FAA, and it doesn't employ multiple lasers or reuse powder — these are still highly innovative production features, which may have sparked caution among some of the FAA's regulators.
Result
Renishaw supplied the three RenAM systems, and Tronosjet printed the engine bracket on the AM250 using a Ti-6Al-4V titanium alloy. Its team then conducted extensive NDT, static, functional and destructive testing and compared its performance with the original cast magnesium bracket, finding that the titanium-printed version was five times stronger. The printed bracket survived loads over 22,000 lb, while the original broke at just 4,000 lb.
"The numbers put things into perspective," continued Campbell. "The bracket's superior tensile strength shows that the titanium print is capable of withstanding significantly higher loads then required, when the aircraft is in flight. This helped convince the regulators that AM was more than up to the job."
After Tronosjet demonstrated the part's strength, safety and quality, the engine bracket was eventually certified by the FAA and has received Parts Manufacturer Approval (PMA). Certification demonstrates that the bracket has received adequate testing in line with FAA standards for airworthiness and means that Tronosjet can now produce and supply it to customers. Significantly, it is one of the first FAA PMA certified metallic AM components — giving Tronosjet a competitive edge.
"We're grateful for Renishaw's engineering prowess and support — it delivered great products, which have been critical for us achieving certification," concluded Campbell.
For more information on the RenAM 500 series and its laser powder bed fusion technology, visit https://www.renishaw.com/en/renam-500-metal-additive-manufacturing-3d-printing-systems.
About Renishaw:
Renishaw is a world leading supplier of measuring systems and production systems. Its products give high accuracy and precision, gathering data to provide customers and end users with traceability and confidence in what they're making. This technology also helps customers to innovate their products and processes.
It is a global business, with over 5,000 employees located in the 36 countries where it has wholly owned subsidiary operations. The majority of R&D work takes place in the UK, with the largest manufacturing sites located in the UK, Ireland and India.
For the year ended June 2023 Renishaw recorded sales of £688.6 million of which 95% was due to exports. The company's largest markets are China, USA, Japan and Germany.
Renishaw is guided by its purpose: Transforming Tomorrow Together. This means working with customers to make the products, create the materials, and develop the therapies that are going to be needed for the future.
Further information at www.renishaw.com
Featured Product
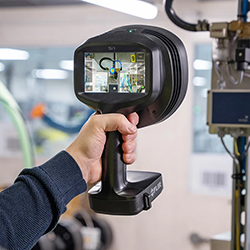