The Commonly Used Metal 3D Printing Materials
Metal 3D printing uses a variety of metal powders, wires, and even liquid resins infused with metal. Almost any metal can be 3D printed, from stainless steel to nickel-based alloys, and in practice, about 8 are most commonly used.
The most common question about metal 3D printing is: Will the final part have the same mechanical properties as a machined, moulded or forged metal part? The answer is yes, and sometimes even better mechanical quality, but it depends a lot on the metal 3D printing technology you use, the type of feedstock used, post-processing and the shape of the part. In addition, the comparison depends on the aspects you are concerned about: for example, tensile strength, static load strength, high cycle fatigue, and so on.
In general, the material properties of metal parts made by metal bond jetting are equivalent to those of metal parts produced by metal injection moulding, and it is one of the most widely used manufacturing methods for the mass production of metal parts. These 8 metal alloys below are just the beginning of what is possible today as metal material producers continue to push the boundaries and customize metal alloys for specific needs using specific metal 3D printing technologies.
1.Stainless Steel
Feature: All-round
Stainless steel is not the material most commonly used in 3D printing, but many alloy varieties. The first two are 316L and 17-4 PH, but also 304L, 15-5 PH, 420, 254, PH1, GP1, 630, and 410 can be printed, as well as custom blends produced by material manufacturer. These steels are specifically designed to resist corrosion. They are a lightweight and affordable metal that is ideal for 3D printing. This is because it is faster and cheaper than traditional methods and can print small batches and complex parts. 3D printing is the preferred option for companies that need a single tool or several replacement parts. Stainless steel can be used in almost any type of 3D printing, from economical wire for extruded 3D printing on benchtop machines to powder for binder jetting and laser powder bed fusion, and even resin.
2.Tool Steel
Feature: High hardness, good wear resistance
Tool steels, like stainless steels, come in different varieties with different tensile strengths, ductility, hardness and other properties. Tool steels are a variety of alloy steels designed specifically for the manufacture of tools. They are known for their hardness, wear resistance and ability to hold a cutting edge at high temperatures. This 3D printing steel is commonly used in the manufacture of injection mould inserts, aerospace components, military applications, manufacturing tools, as well as construction and architecture. The main advantage of 3D printed tool steel is not only its strength, but also its unique ability to create parts with internal channels (e.g. cooling channels in moulding tools) and lattice fillings that cannot be manufactured by traditional methods.
3.Low-Alloy Steel
All 3D printing steels are alloys, but this category includes steels with low or less than 5 per cent of other elements. These low alloy steels are designed to have higher mechanical properties and greater resistance to wear and corrosion than other steels which are commonly used in automotive, aerospace and structural applications.
4.Aluminum
Feature: Lightweight and corrosion resistant
For aerospace, automotive and industry, the design freedom and cost efficiency of 3D printing further enhances the lightweight and chemical resistance of aluminum components. The use of aluminum and aluminum alloys in 3D printing is surging because the metal is economical and easy to 3D print. Like most metals, aluminum can be used as wire or powder for a variety of 3D printing techniques. Aluminium has good chemical resistance, is very light and has one of the best strength-to-weight ratios of any metal. Combined with silicon and magnesium, it is the choice of many in the aerospace and automotive industries because of its ability to withstand harsh conditions.
5.Titanium
Feature: Lightweight and biocompatible
As strong as steel but half the weight, titanium is a complex metal that is practically made for 3D printing. Titanium has become one of the most commonly used metals in additive manufacturing, with a wide range of applications in aerospace, joint replacement and surgical tools, racing car and bicycle frames, electronics and other high-performance products. Titanium and titanium-based alloys offer high mechanical strength, high strength-to-weight ratios and better corrosion resistance than stainless steel. It makes rockets and aircraft lighter, thus saving fuel and increasing payload capacity. In the medical industry, 3D printed titanium implants have been successfully used in the spine, hips, knees and extremities due to the inherent biocompatibility and good mechanical properties of the metal, coupled with the ability to customize porous structures with 3D printing, allowing for osseointegration and mass customization for better patient outcomes.
6.Copper
Feature: Electrical and thermal conductivity
3D printing using pure copper and space-age copper alloys is available with a range of metal 3D printers and services. You can create rapid copper prototypes using copper filament on an FDM 3D printer and large copper rocket boosters using copper alloys on a laser powder bed fusion 3D printer. There is also copper wire and copper resin for micro 3D printing. In fact, copper plays a huge role in the global sustainable development goals as a key component of electric motors, charging infrastructure, solar energy and batteries.
7.Nickel Alloy
Feature: Extreme environments resistant
Nickel-based alloys and "high-temperature alloys" are known for their excellent high-temperature strength, corrosion and oxidation resistance. These alloys retain their strength and mechanical properties at high temperatures. They are commonly used in demanding applications such as aerospace, gas turbines, chemical processing and marine environments. In recent years, these alloys have also become increasingly popular in 3D printing, especially in the aerospace and automotive industries. When referring to nickel alloys, you may hear the term inconel. Inconel is the trade name for a range of nickel-chromium-based high-temperature alloys, including IN625, IN718 and IN939. Nickel alloys are generally more expensive than other materials such as steel and aluminium and may not be suitable for low temperature applications.
8.Cobalt Chrome
Feature: High temperature and corrosion resistance
3D printed cobalt chrome has a high strength-to-weight ratio and excellent corrosion resistance, making it a good material choice for aerospace components and industrial machinery. It is also biocompatible and is often used in orthopaedic implants, dental prosthetics and medical devices that require long-term contact with biological tissue. Cobalt-chromium alloys can be processed using additive manufacturing techniques such as selective laser melting (SLM) or electron beam melting (EBM). This allows complex geometries and customized parts to be produced with minimal material waste, making it attractive to industries adopting advanced manufacturing techniques.
To sum up, metal 3D printing uses a wide range of metal powders and wires, including stainless steel, tool steel, etc. to print complex parts with superior mechanical properties. Commonly used metals in 3D printing include aluminum, titanium, copper, nickel alloys, tool steel, cobalt-chromium alloys, stainless steel for aerospace, medical and jewelery applications and more.
Featured Product
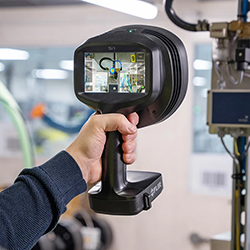