Sauber Motorsport optimizes the post processing of SLA parts on large build platforms with C1 Max
50 % faster, improved surface quality, and more environmentally friendly
Since February, Sauber Motorsport has been using a C1 Max from AM Solutions - 3D post processing technology for the post processing of SLA printed parts on their 3D Systems ProX 800 machines. The C1 Max is also compatible with the newer SLA 750 series. The system was developed as part of the existing technology partnership between the two companies and excels in many areas, particularly in terms of efficiency, surface quality, user-friendliness, environmental compatibility, and health protection.
The parts that Sauber Motorsport produces with SLA printing are highly complex and require maximum precision. This is evident from their application, as they are almost exclusively used in the wind tunnel for Formula 1 and are crucial for a vehicle's aerodynamics. To consistently and quickly deliver high-quality 3D printed parts - approximately 1,000 parts per week between October and February - efficient post-processing is essential. "In the past, we had to manually perform many steps in the chemical post processing of SLA parts," explains Vitor Sousa, Head of AM Plastic & CNC for AM at Sauber Motorsport. "This not only took a lot of time, especially with seven printers, but it was also a significant strain on the staff working with the solvents. Since February, we have been using two C1 Max machines from AM Solutions and are extremely satisfied."
50 percent time savings with significantly improved surface quality
The C1 Max is based on the C1 concept and was specifically adapted by AM Solutions - 3D post processing technology to meet the needs of Sauber Motorsport for using large build platforms. SLA-printed parts are immersed in the treatment tank using an automatically lowering build plate and are surrounded by a specially temperature-controlled process fluid. A propeller, working in tandem with perfectly coordinated but individually controllable nozzles, ensures optimal flow around the parts and maximum flexibility. A mesh basket also ensures that no parts are lost or damaged in the immersion tank. The perfectly coordinated interaction of chemical, thermal, and mechanical processes softens the support structures, allowing them to be easily and gently removed. In the past, each part had to be laboriously processed by hand with a spatula, requiring extended PPE equipment. "This saves us a lot of time. We used to need an entire day to post process the output of our seven machines. Now, half a day is enough," explains Sousa. "Scrap is also minimized, and the surface quality is significantly higher, requiring much less effort in further post processing."
More environmentally friendly process fluid and improved health protection
The C1 Max uses a specially developed process fluid from AM Solutions - 3D post-processing technology that is more environmentally friendly than conventional fluids. This also has a positive effect on the health of the staff, who can now work in the room without wearing masks. "The health protection of our employees was a very important argument for us," Sousa emphasizes. Another practical advantage is that no additional equipment is needed when emptying the system. Once the medium is saturated, it is safely pumped out via the integrated pump and disposed of by a service provider. Overall, the cleaning effort for the system has been significantly reduced compared to before.
Future-oriented customer solution specifically developed for large build platforms
The development process of the C1 Max spanned about a year and a half, during which data and parts were continuously exchanged. An important aspect was determining the optimal size of the system. This allows the processing of a build volume of 750 mm (length) x 750 mm (width) x 550 mm (height) and thus the processing of a complete build plate of the 3D Systems ProX 800 or the SLA 750. Another advantage is that the "bare" plates can be easily placed in the system overnight for cleaning. "We used to have to laboriously dry-ice blast around 25 plates every Friday. Now, we can repurpose the space and time for other tasks," Sousa explains. To be prepared for future printer versions, adapters were used to make the machine flexible and adjustable to future needs. "Formula 1 is the pinnacle of motorsport, which means we operate at the highest technical level. Safe and efficient processes are crucial for us, and with the C1 Max, we've taken another big step in that direction," Sousa concludes.
Rösler Oberflächentechnik GmbH / AM Solutions
For over 80 years, the privately owned Rösler Oberflächentechnik GmbH has been actively engaged in the field of surface preparation and surface finishing. As global market leader, we offer a comprehensive portfolio of equipment, consumables and services around the mass finishing and shot blasting technologies for a wide spectrum of different industries. Our range of about 15,000 consumables, developed in our Customer Experience Centers and laboratories located all over the world, specifically serves our customers for resolving their individual finishing needs. Under the brand name AM Solutions, we offer numerous equipment solutions and services in the area of additive manufacturing/3D printing. Last-but-not-least, as our central training center the Rösler Academy offers practical, hands-on seminars to the subjects mass finishing, shot blasting and additive manufacturing. The Rösler group has a global network of 15 locations and approx. 150 sales agents.
For more information, please visit: www.solutions-for-am.com
About Sauber Group of Companies:
The Sauber Group of Companies is composed of two operational entities: Sauber Motorsport AG, which operates and manages its Formula OneTM team; and Sauber Technologies AG, which focuses on third-party business in the areas of advanced engineering, prototype development and additive manufacturing, in addition to full and model-scale testing in the factory's state-of-the-art wind tunnel and ground-breaking innovation in the field of aerodynamics. The companies collaborate closely and share know-how to apply the expertise of all the dedicated individuals at the headquarter in Hinwil, Switzerland, to all internal and external projects.
The Sauber Group puts sustainability at the heart of its mission; its business, operating under the ISO 14001 environmental management standard, has been carbon neutral since 2011 and the company has achieved the Three-Star level in the FIA Environmental Accreditation Framework.
Since its founding in 1970, the innovative Swiss company has been setting standards in the design, development and construction of race cars for various championship series, such as Formula One, DTM, and WEC. Following its own Formula One debut in 1993, Sauber Motorsport AG has established one of the few traditional and privately held teams in the sport. A member of the exclusive club of teams which competed in more than 500 F1 races, it celebrated 30 years in the sport in 2022 and continues to go from strength to strength on and off the track.
For more information, please visit: www.sauber-group.com
Featured Product
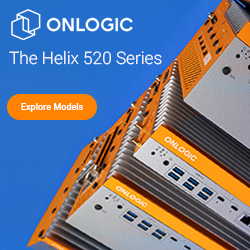