Making Injection Molding Cost-Effective
This article explains how to make injection molding cost-effective by comparing it with 3D printing for manufacturing plastic parts. It highlights the high initial mold costs in injection molding and how these costs spread out over larger production volumes, reducing the cost per unit. The article also examines factors affecting cost-effectiveness, including mold material, part design, and plastic type. By comparing the variable costs of injection molding with the fixed costs of 3D printing, the article provides guidance on choosing the best method for different order sizes.
Making Injection Molding Cost-Effective
Injection molding is renowned as a cost-efficient manufacturing method, especially for large production volumes. The reason lies in its cost structure: while the initial expense of creating a mold is substantial, the cost of producing each part afterward is minimal. This means that as the order quantity rises, the cost per unit falls, making it increasingly economical.
For example, if a steel mold for a toy car costs $5,000 and each car costs $0.50 to produce, then ordering just one unit costs a staggering $5,000.50. Ordering two units would cost $5,001, while ordering 1,000 units would reduce the average cost to $5.50 per unit. Thus, higher quantities make the process more cost-effective as the high mold cost gets distributed across more units.
The Scale for Cost-Effectiveness
But what quantity qualifies as "large" in injection molding? For businesses weighing options for mid-sized production runs, knowing the point where injection molding becomes more cost-effective than alternatives like 3D printing is crucial. This crossover point, however, isn't always clear-cut, as it varies based on several factors.
RpProto, a company specializing in injection molding and on-demand manufacturing, offers insights into how order size impacts the choice between injection molding and 3D printing.
Injection Molding vs. 3D Printing: Key Initial Considerations
For companies needing plastic parts for prototyping or production, both 3D printing and injection molding offer advantages. However, in certain cases, one method clearly stands out.
For instance, if only a small number of prototypes is needed and material properties are of little consequence, 3D printing is generally the best choice for its lower costs and rapid production times. Conversely, if prototypes must closely mimic the final product, such as for investor presentations, the extra cost of injection molding might be worthwhile to better showcase the product's functionality and appearance.
Comparing Costs: Injection Molding vs. 3D Printing
Injection molding and 3D printing involve different cost structures. Injection molding has a high initial cost due to mold fabrication, but the per-part cost is very low once the mold is in place. For smaller businesses, the upfront mold cost can be prohibitive.
In contrast, 3D printing does not require a mold, making it a one-step process with no significant initial cost. However, each printed part tends to be more expensive because 3D printing materials are costly, and the printing process is time-intensive. This results in a fixed per-part cost regardless of order size, making 3D printing economical only for smaller quantities, while injection molding becomes cheaper with larger volumes.
Determining Cost-Effectiveness: Key Factors to Consider
Mold Cost
The mold is often the most expensive part of injection molding, sometimes costing thousands of dollars. However, this cost can be reduced with rapid tooling, which uses CNC machining or 3D-printed metals to create prototype molds. Additionally, opting for an aluminum mold instead of steel can reduce costs, though aluminum is less durable.
For example, if a steel mold costs $5,000, an aluminum mold might cost only $1,000. Assuming a $0.50 production cost per part, a 3D-printed toy car costing $20 would make injection molding cost-effective at higher volumes. For a 50-unit order, 3D printing is cheaper; however, for 60 units or more, injection molding with an aluminum mold becomes more economical.
Material Considerations
The type of plastic used also affects the cost-effectiveness of each manufacturing method. Some plastics are easier to mold than to print and vice versa. Generally, plastic pellets for injection molding are less expensive than the filament used in 3D printing. For high-end materials like nylon, a lower quantity may be enough to make injection molding more economical than 3D printing, whereas cheaper plastics may require a larger order volume to reach cost-effectiveness.
Part Design
Complex part designs can also influence the choice of manufacturing process. For instance, parts with overhangs may be more suited to 3D printing, which doesn't require complex mold modifications. If the design demands costly molds, a larger quantity may be needed to justify the mold's expense.
Manufacturing Process Type
While Fused Deposition Modeling (FDM) is the most common 3D printing process, more advanced options like Stereolithography (SLA) or Selective Laser Sintering (SLS) offer higher-quality finishes but at a higher cost. For example, ordering 200 FDM parts might be cheaper than 200 injection-molded parts, but 200 parts made using SLS could be more expensive than injection molding.
Conclusion
Choosing between injection molding and 3D printing depends on multiple variables, including mold cost, material, and part complexity. Injection molding's per-unit cost decreases with volume, while 3D printing has a consistent per-unit cost, making it ideal for smaller orders. To find the best solution, RpProto recommends requesting quotes for both methods to identify the most cost-effective approach for your project.
Get in touch with RpProto for personalized advice on your project's manufacturing needs.
Featured Product
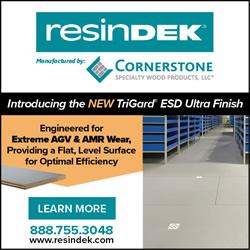