RpProto Expands Advanced Manufacturing Capabilities with Vacuum Casting Services
Ideal for industries needing cost-effective, high-quality prototypes, RpProto's vacuum casting supports agile production, digital workflow compatibility, and sustainability by minimizing waste and allowing for reusable molds. The service integrates seamlessly with digital design files, enabling a quick transition from CAD to physical prototype and helping clients streamline their product development cycle.
RpProto has introduced state-of-the-art vacuum casting services, underscoring its commitment to providing innovative, adaptable solutions that meet the demands of Industry 4.0. As manufacturers strive to increase efficiency, accuracy, and agility, RpProto's vacuum casting service offers an ideal approach for rapid prototyping and low-volume production of high-quality, detailed parts.
Vacuum casting stands out as an efficient, highly precise method for creating detailed prototypes and low-volume production parts. By pouring liquid materials like polyurethane or silicone into a mold under vacuum, the process eliminates air bubbles and produces components with exceptional detail and surface quality. This level of precision is essential for industries such as automotive, aerospace, consumer electronics, and medical devices, where accurate prototypes are critical to the product development process.
Vacuum casting's ability to replicate complex designs with fine details makes it a top choice for manufacturers seeking an affordable, flexible, and high-quality solution for creating limited runs of parts that closely resemble their final versions.
Key Advantages of Vacuum Casting for Industry 4.0
RpProto's vacuum casting services align with the core principles of Industry 4.0, providing the following benefits to clients in advanced manufacturing:
Digital Integration and Workflow Compatibility
Vacuum casting is fully compatible with digital workflows. Clients can submit CAD files directly to RpProto, which are then used to create precision molds. This seamless transition from digital design to physical prototype is crucial for manufacturers adopting Industry 4.0 practices, where connectivity and data integrity are paramount.
Efficiency for Low-Volume Production
Unlike traditional manufacturing methods requiring significant investment in tooling, vacuum casting offers a cost-effective solution for small batches or prototypes. This makes it an ideal choice for low-volume production and rapid prototyping, allowing manufacturers to produce highly detailed parts without the expense and lead times of full-scale production.
Agility and Customization
The vacuum casting process allows for quick adjustments between production runs, making it easy to iterate on designs and customize parts. This flexibility supports the agile production models central to Industry 4.0, where rapid response to market demands and shorter lead times are essential.
Sustainability
Vacuum casting supports sustainable manufacturing by minimizing material waste. Its precision helps reduce the need for rework, and reusable molds further reduce material consumption, making it a greener choice for companies looking to optimize resources.
Elevating Product Development with Vacuum Casting
For companies across sectors, RpProto's vacuum casting services offer a reliable way to bring products from concept to market faster. The precision of vacuum casting allows for the creation of parts that can be tested for form, fit, and function, ensuring that prototypes meet design expectations. These high-quality prototypes are especially valuable for performance testing, marketing displays, and customer feedback, supporting an efficient product development cycle.
By enhancing agility and reducing costs, RpProto's vacuum casting is a strategic asset for manufacturers who need a rapid, flexible process without compromising quality. Clients benefit from shorter lead times, cost savings, and the ability to respond quickly to new design requirements.
RpProto: Leading the Future of Advanced Manufacturing
As the manufacturing industry embraces digitalization and automation, RpProto continues to innovate with solutions like vacuum casting that support the principles of Industry 4.0. This service complements RpProto's portfolio of advanced manufacturing offerings—including injection molding, pressure die-casting, and carbon fiber manufacturing—providing clients with a comprehensive set of tools to meet modern production challenges.
RpProto's commitment to quality, precision, and customer satisfaction is evident in its dedication to advanced, cost-effective manufacturing solutions that empower clients to remain competitive. With vacuum casting, RpProto enables manufacturers to realize their visions efficiently, bringing complex designs to life with speed, precision, and reliability.
This expansion of services reinforces RpProto's position as a trusted partner in advanced manufacturing, equipping clients to thrive in a fast-evolving industry.
Featured Product
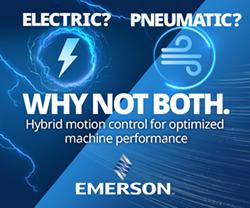