Replique at Formnext 2024: Expanded Technology Portfolio, Material Hub Upgrades, and New Healthcare Applications
Users can browse materials based on specific application requirements and access detailed property data to make informed decisions in a short period of time.
Mannheim, Germany, October 29, 2024 - Replique, the end-to-end platform for industrial sourcing, returns to Formnext 2024 (Hall 12.1, Booth B117) to showcase its latest platform upgrades and innovative applications across diverse industries. Expanding beyond 3D printing, Replique now provides clients with access to additional manufacturing technologies, such as forging, metal casting, and injection molding. This expansion gives customers access to over 250 production partners, enabling them to meet their sourcing needs with even greater flexibility. Attendees can also explore updates to Replique's Material Hub, which now includes metal materials and a direct comparison feature for seamless material selection.
Expanding the Production Network with Traditional Technologies
The ongoing expansion of the production network is a strategic response to the growing demand for decentralized manufacturing solutions beyond 3D printing. To meet the diverse needs of customers, Replique is now incorporating traditional methods such as forging, casting, and injection molding into its offerings. "With this expansion, we are responding to our customers' desire to source all their manufacturing needs - from individual parts to serial production - centrally and using the most suitable technology for each application. This enables companies to quickly adapt to any customer requirements in a complex procurement environment," says Dr. Max Siebert, CEO and Co-Founder of Replique.
Enhanced Material Hub for 3D Printing: Now with Metals and Enhanced User Experience
Since its launch at Formnext 2023, Replique's Material Hub has attracted over 400 active users. The hub now offers a more intuitive experience with a new comparison feature, allowing users to easily assess materials side-by-side and quickly choose the best option for their applications. With the addition of metal materials for additive manufacturing, customers can now qualify complex, high-strength parts with precision. Users can browse materials based on specific application requirements and access detailed property data to make informed decisions in a short period of time.
"The integration of metal materials and usability enhancements of our Material Hub represent another step toward democratizing additive manufacturing. We are excited to establish new partnerships with metal manufacturers at Formnext who want to make their materials available on our platform," says Jan Weickel, Technical Sales Manager and Project Manager of the Replique Material Hub.
Highlighting Innovations for Healthcare and Pharma
This year, Replique puts a special focus on the healthcare sector at Formnext. In partnership with Zermec Pharma AG, provider of secure powder transfer systems, Replique has developed a fully 3D-printed containment valve, specifically designed to meet the high standards of powder manufacturers and pharmaceutical companies focused on minimizing contamination and enhancing production quality. Visitors can see this innovative valve at Replique's booth.
"Thanks to the co-engineering with Replique, we were able to prototype the containment valve quickly and effectively. From the start of development to the launch at Achema 2024, it took just four months. The material we used is PFAS-free, meets stringent food and pharmaceutical standards, and has sliding properties similar to PTFE. This wouldn't have been feasible with traditional CNC manufacturing," says Jochen Knoll, Chief Customer Officer at Zermec Pharma AG.
Replique is also excited to present new developments in its partnership with RehamedPower, a pioneer in rehabilitation equipment. Following the successful integration of 3D printing for the RP1 electric wheelchair - from prototyping to full-scale production - they will unveil a new rollator with a 3D-printed frame. This design not only meets the rising demand for mobility aids that combine style with functionality but also simplifies assembly with fewer parts and connectors.
About Replique GmbH
Replique GmbH provides a secure digital manufacturing platform that enables OEMs to provide parts on-demand to their customers through a global and decentralized 3D printing network of more than 250 facilities. As an end-to-end solution, Replique supports its customers along the entire value chain, including design, technology and material selection, as well as digital warehousing. The solution easily integrates into the existing system landscape (e.g. ERP systems, e-commerce), and is already used by several OEM, such as Alstom, MAN, Danfoss and Miele. Replique was founded by BASF employees from the fields of material science and digitization.
For further information on Replique, please visit: www.replique.io
Featured Product
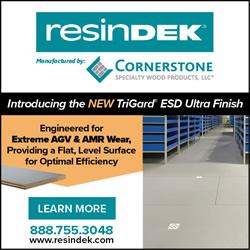