SECS/GEM on Applied Materials P-5000 Metal Through the EIGEMBox
In the rapidly evolving semiconductor industry, automation and efficient data management are critical for success. One of the most effective ways to enhance manufacturing processes is through the integration of SECS/GEM (SEMI Equipment Communications Standard/Generic Equipment Model) protocols. This article explores the application of SECS/GEM on the Applied Materials P-5000 Metal etching tool, utilizing the innovative EIGEMBox to optimize operations.
SECS/GEM is a set of communication standards developed by SEMI (Semiconductor Equipment and Materials International) to facilitate real-time data exchange between semiconductor manufacturing equipment and factory control systems. These standards enable manufacturers to monitor equipment status, performance, and critical parameters, leading to improved productivity, reduced downtime, and enhanced process control.
The SECS/GEM architecture consists of two main components:
SECS (SEMI Equipment Communication Standard): This part defines the communication protocol for equipment and host systems.
GEM (Generic Equipment Model): This provides a standard framework for equipment capabilities and data structure.
By implementing SECS/GEM, semiconductor manufacturers can achieve seamless integration of various tools, providing them with the data necessary for informed decision-making.
The Applied Materials P-5000 Metal Etching Tool
The P-5000 Metal is a state-of-the-art etching system designed for high-performance applications in semiconductor fabrication. It supports various processes, including metal etching, dielectric etching, and more. Key features of the P-5000 include:
High Precision: The tool offers exceptional etch uniformity and critical dimension control, making it ideal for advanced semiconductor devices.
Versatility: Capable of handling various materials, the P-5000 is adaptable to different manufacturing needs.
User-Friendly Interface: The intuitive interface simplifies operation and enhances usability for technicians.
Integrating SECS/GEM capabilities into the P-5000 allows for real-time monitoring and control, optimizing its performance and reliability.
The Role of EIGEMBox
The EIGEMBox is an advanced automation solution that simplifies the integration of SECS/GEM protocols into semiconductor manufacturing equipment. Designed for ease of use and flexibility, the EIGEMBox acts as a bridge between the P-5000 and the factory's host system.
Key Features of EIGEMBox
Plug-and-Play Integration: The EIGEMBox can be easily connected to the P-5000, enabling quick setup without extensive modifications to existing equipment.
Data Collection and Analysis: It continuously collects critical parameters such as temperature, pressure, and etch rates, providing valuable insights for process optimization.
Real-Time Communication: With SECS/GEM protocols, the EIGEMBox ensures seamless data exchange between the P-5000 and the factory control system.
Scalability: The EIGEMBox can be utilized across various tools and systems, making it an ideal solution for factories looking to enhance their automation capabilities.
Benefits of Implementing SECS/GEM on the P-5000 with EIGEMBox
Integrating SECS/GEM through the EIGEMBox on the Applied Materials P-5000 Metal offers numerous advantages for semiconductor manufacturers:
1. Enhanced Process Visibility
Real-time data collection and monitoring provide insights into equipment performance, allowing for immediate identification of issues and trends. This visibility empowers operators to make informed decisions, improving overall process efficiency.
2. Improved Equipment Utilization
By leveraging SECS/GEM data, manufacturers can optimize scheduling and maintenance, leading to increased equipment utilization rates. The EIGEMBox helps ensure that the P-5000 is operating at peak performance, reducing idle time.
3. Data-Driven Decision Making
Access to comprehensive data analytics enables manufacturers to analyze performance metrics and identify areas for improvement. With the EIGEMBox, teams can generate reports that facilitate data-driven decision-making, ultimately enhancing production outcomes.
4. Reduced Downtime
Early detection of anomalies or performance issues allows for proactive maintenance, minimizing unplanned downtime. The EIGEMBox not only monitors equipment status but also provides alerts for any deviations from normal operating conditions.
5. Streamlined Compliance
In the semiconductor industry, compliance with industry standards is critical. SECS/GEM implementation simplifies compliance reporting by providing standardized data formats and communication protocols, ensuring manufacturers meet regulatory requirements.
Real-World Application: Case Study
A leading semiconductor manufacturer implemented SECS/GEM on their Applied Materials P-5000 Metal tool using the EIGEMBox. Before integration, the manufacturer faced challenges with equipment downtime and inconsistent process performance.
After deploying the EIGEMBox, they achieved the following results:
30% Reduction in Downtime: Early detection of issues led to timely interventions, significantly reducing production interruptions.
15% Increase in Throughput: Enhanced process control and data analytics resulted in improved production efficiency.
Higher Quality Products: Improved etch uniformity and precision contributed to better-quality semiconductor devices.
These outcomes demonstrate the powerful impact of integrating SECS/GEM with the EIGEMBox on manufacturing performance.
In an industry where precision and efficiency are paramount, the integration of SECS/GEM protocols on the Applied Materials P-5000 Metal through the EIGEMBox represents a significant advancement in semiconductor manufacturing. By enabling real-time monitoring, data analysis, and enhanced process control, manufacturers can drive productivity and achieve greater operational excellence.
Call to Action
Are you ready to transform your manufacturing processes? Discover how eInnoSys can help you implement SECS/GEM solutions tailored to your needs. Contact us today to learn more about our innovative automation solutions and take the first step towards optimizing your semiconductor operations!
Featured Product
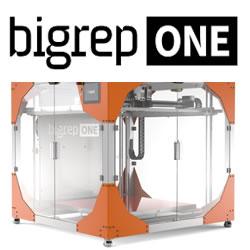