Manufacturing Transparent Prototypes: 5 Questions to Help You Pick the Right Process
There are many technologies available to make clear transparent prototypes, including 3D printing, CNC machining, injection moulding, and vacuum casting. Learn how to choose the right process to make your transparent parts.
When deciding which technology to use for your transparent prototypes, a good place to start is by asking yourself these five questions:
1. What degree of clarity do I need?
You might just need translucent or clear parts for decorative or aesthetic purposes. For such cases, SLA 3D Printing will do the trick, although it's worth noting that SLA parts use UV- sensitive materials and are prone to yellowing and degradation when exposed to sunlight for prolonged periods. If you need optically transparent and scratch-resistant parts, acrylic (PMMA) machining and injection moulding are the best choices. It's also worth establishing if only certain areas require clarity (or the whole part).
2. What is my budget?
Budget constraints often dictate the choice of prototyping process. While SLA, vacuum casting, and CNC machining can be more affordable for small quantities, injection moulding becomes cost-effective at higher volumes despite its higher initial setup costs. Careful evaluation of your financial limits will help in selecting the most suitable method.
3. How many parts do I need?
The number of parts you require will heavily influence your choice of manufacturing process. For instance, achieving optimal transparency in SLA parts requires multiple rounds of hand polishing, which can be time-consuming, especially for large quantities. It's also challenging to achieve the same level of clarity on each part compared to processes like injection moulding or vacuum casting, where the high-polish finish is textured directly into the mould to create identical copies.
If you need a 1-off piece or a handful or parts, SLA is perfect. If you need a handful to batch of parts, CNC and vacuum casting are great options. If you need quantities from 100 and up, injection moulding is a cost-effective choice.
4. How complicated is my design?
CNC can easily fabricate and shape parts to precise dimensions, and is preferred for most applications, but it may require splitting your design into multiple sections to machine and then joining them together with glue. Although this can be done with great skill by professional model makers, there is still going to be a visible join and inherent weakness. For very complex designs and intricate designs, 3D printing (SLA) and injection moulding are ideal.
5. How urgently do I need it?
How many (extra) days can you afford? Ultimately, the goal of rapid prototyping is to quickly create prototypes or models of a product so you can test and validate the features and functionalities as soon as possible. 3D printing is the easiest way to achieve quick iterations. Although injection moulding will result in the best clarity, it takes the most time.
By asking the five questions above, you'll be able to narrow down your options. If you would like to consult with our team about getting your prototype manufactured, contact us at info@hlhrapid.com or visit our website at hlhrapid.com .
Featured Product
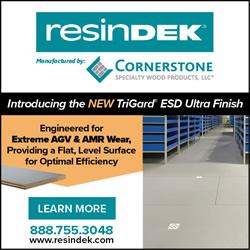
ResinDek® TRIGARD® ESD ULTRA FOR HIGH-TRAFFIC ROBOTIC APPLICATIONS
To maximize the productivity of an autonomous mobile robot (AMR) or automatic guided vehicle (AGV) deployment, it's critical to create the optimal environment that allows the vehicles to perform at their peak. For that reason, Cornerstone Specialty Wood Products, LLC® (www.resindek.com) created the TriGard® ESD Ultra finish for its ResinDek® engineered flooring panels. The TriGard ESD Ultra finish is ideal for high-traffic robotic applications characterized by highly repetitive movement patterns and defined travel paths.