Arnold Magnetic Technologies Highlights Custom Electromagnetic Capabilities
Solenoids ideal for critical waveguide applications in medical, scientific, aerospace and telecommunications
Rochester, NY: Arnold Magnetic Technologies Corporation (Arnold), a subsidiary of Compass Diversified (NYSE: CODI) and leading global manufacturer of high-performance magnets and precision thin metals, highlights its custom electromagnetics used in medical, scientific research, telecommunications, and aerospace and defense applications. From exploring the deepest parts of space in search of near-Earth objects, to saving lives by providing critical components for oncology equipment, Arnold's electromagnets (also known as solenoids) provide the flexibility needed in generating magnetic fields so necessary for critical waveguide applications.
As one of NASA's founding partners, Arnold's electromagnetics have been an integral part of nearly every government-sponsored satellite, including Doppler weather and radar systems and the US Air Force (USAF) Airborne Warning and Control System (AWACS). Arnold is also bringing its deep expertise to the development of the next generation quadrupoles and dipoles being used in electromagnetics for large fusion and pulsed power projects.
Arnold manufactures a wide variety of custom electromagnets that generate uniform or proportioned magnetic field shapes and with a wide range of magnetic field intensities. These electromagnets are either made up of tape wound foil wafers or built up from coils of wire.
All Arnold tape wound electromagnets feature coils that are electrically controlled to the precise field strength desired. Depending upon specific requirements, magnetic field distribution may be uniform, or it may have peaks, plateaus, and valleys along the axial length of the electromagnet, Shaped field electromagnets can be custom-designed to specific configurations with great precision. Coils may be of various widths within the electromagnet and they can be made interchangeable.
Customers can select nominal ID and OD to meet application size requirements. Also available are special designs that use chilled oil or liquid nitrogen to allow higher than normal current, generating up to 200 percent greater field intensity than an uncooled design.
For more information on Arnold's custom electromagnetic capabilities or to inquire about solenoid refurbishment, visit https://www.arnoldmagnetics.com/products/electromagnets/.
###
About Arnold Magnetic Technologies
Based in Rochester, NY with an operating history of more than 125 years, Arnold is a leading global manufacturer of engineered solutions for a wide range of specialty applications and end-markets, including aerospace and defense, general industrial, motorsport, oil and gas, medical, and energy. From its Technology Center and manufacturing facilities located in the United States, the United Kingdom, Switzerland, and China, the company produces engineered magnetic assemblies in addition to high-performance permanent magnets, precision foil products, and highly loaded composites that are mission critical in motors, generators, sensors, and other systems and components. Based on its long-term relationships, the company has built a diverse and blue-chip customer base totaling more than 2,000 clients worldwide. Arnold's Precision Thin Metals division is ISO9001:2015/AS9100RevD certified, Nadcap® certified for heat treatment, ITAR registered and able to adhere to DFARS clauses. For more information on Arnold, visit https://www.arnoldmagnetics.com.
Featured Product
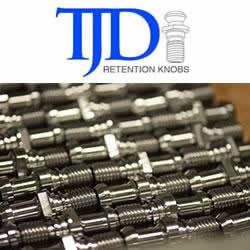