Manufacturing Metamorphosis: How AI is Redefining Safety on the Factory Floor
Looking ahead, the evolution of AI in manufacturing safety is bound to bring even more transformative changes. With advancements in generative AI, factories can simulate and optimize safety protocols, ensuring that every scenario is accounted for.
Welcome to the era where artificial intelligence (AI) is not just a futuristic concept but a present-day reality transforming factories! Did you know that incorporating AI-driven safety systems in manufacturing settings can enhance the EBDITA growth of 4-5%? According to a recent study by McKinsey & Company, AI technologies are set to enhance manufacturer's productivity by 10-15% annually through improved safety measures and efficiency.
In line with Bill Gates' insight, "The first rule of any technology used in a business is that automation applied to an efficient operation will magnify the efficiency. The second is that automation applied to an inefficient operation will magnify the inefficiency," it becomes clear that AI not only enhances well-organized operations but can also spotlight areas needing improvement, which is extremely important for upgrading factory floors.
๐๐๐๐๐ญ๐ฒ ๐.๐ ๐๐จ๐ซ ๐๐๐ง๐ฎ๐๐๐๐ญ๐ฎ๐ซ๐ข๐ง๐ ๐๐ง๐๐ฎ๐ฌ๐ญ๐ซ๐ข๐๐ฌ
As part of Manufacturing 4.0, AI integrates seamlessly into factories, creating a safer and more efficient environment. Imagine predictive maintenance systems that foresee equipment failures before they happen, significantly reducing downtime and accidents. According to a Deloitte report, manufacturing produces approximately 1,812 petabytes (PB) of data annually, surpassing the data generated by industries such as communications, finance, and retail, when used to train AI for various predictive maintenance purposes can increase production line reliability by up to 20% and reduce maintenance costs by 10%. Furthermore, AI-driven analytics can monitor worker behavior and machinery in real time, identifying potential safety hazards and preventing accidents before they occur.
But that's not all. AI-powered safety systems are taking worker protection to new heights. Real-time data analysis and machine learning algorithms identify potential hazards, alerting workers instantly and suggesting corrective actions. For instance, a recent PwC study highlighted that companies adopting AI-driven safety measures saw a 27% decrease in workplace injuries. Additionally, the integration of AI with wearable technology can monitor workers' health indicators, ensuring immediate response in case of emergencies. This holistic approach safeguards employees and also boosts productivity, as healthier, safer workers contribute to more efficient operations.
Are you envisioning the future of AI-driven safety practices? There are many interactive scenarios depicting potential advancements of AI on factory floors.
๐๐ ๐ข๐ง ๐๐๐ญ๐ข๐จ๐ง ๐จ๐ง ๐ ๐๐๐ญ๐จ๐ซ๐ฒ ๐ ๐ฅ๐จ๐จ๐ซ๐ฌ
Imagine a factory where AI isn't just a tool but a dynamic partner in ensuring safety. Video analytics, powered by AI, can monitor production lines in real time, detecting anomalies and potential hazards. For instance, cameras equipped with AI can identify if a worker is not wearing proper safety gear or if a machine is operating abnormally, immediately alerting supervisors. This proactive approach not only prevents accidents but also enhances overall operational efficiency.
Machine learning algorithms further enhance safety by analyzing historical data to predict and prevent potential hazards. By learning from past incidents, these algorithms can suggest safety improvements and help optimize workflows for maximum safety. Generative AI adds another layer of innovation by simulating various scenarios and their safety implications. This allows manufacturers to anticipate risks and implement preventive measures, ensuring a safer working environment for all. With AI as a vigilant ally, factory floors are not just safer but smarter than ever before, ushering in a new era of manufacturing safety.
In addition to AI, smart site safety systems are revolutionizing safety on factory floors. These systems integrate IoT devices and sensors to monitor environmental conditions and worker activities in real-time. For example, wearable devices can track biometric data and detect fatigue or stress levels, alerting workers to take breaks or adjust their workload accordingly. Moreover, these systems can automatically shut down machinery if unsafe conditions are detected, preventing accidents before they happen. But the future doesn't stop there. The concept of smart factories, epitomized by initiatives like Alat in Saudi Arabia, takes safety and efficiency to new heights. By leveraging AI, IoT, and robotics, Alat aims to transform traditional factories into interconnected hubs of innovation. Imagine machines that can not only perform tasks autonomously but also anticipate and prevent accidents. This is the promise of smart factories - a future where safety is not just a priority but a fundamental aspect of every operation.
But will this replace humans from factory floors?
๐๐๐ฏ๐ข๐ ๐๐ญ๐ข๐ง๐ ๐๐ก๐๐ฅ๐ฅ๐๐ง๐ ๐๐ฌ & ๐ ๐ฎ๐ญ๐ฎ๐ซ๐ ๐๐จ๐ซ๐ข๐ณ๐จ๐ง๐ฌ
As we navigate the challenges of integrating AI into manufacturing, one prevalent misconception is the fear of job loss. However, the reality is far from it. The advent of AI in manufacturing has not led to massive job losses but rather to a transformation of roles. While some repetitive tasks may be automated, new opportunities arise in managing and maintaining these AI systems. It's a shift towards more skilled and meaningful work, where humans and AI collaborate to enhance productivity and safety. Additionally, ensuring data security and privacy remains a critical challenge, as AI systems rely heavily on data collection and analysis. Implementing robust cybersecurity measures and transparent data policies is essential for overcoming these hurdles.
Looking ahead, the evolution of AI in manufacturing safety is bound to bring even more transformative changes. With advancements in generative AI, factories can simulate and optimize safety protocols, ensuring that every scenario is accounted for. Furthermore, the integration of AI with robotics opens up new possibilities for safer and more efficient operations. For instance, collaborative robots, or cobots, can work alongside humans, taking on the most dangerous tasks and reducing the risk of accidents. The future of manufacturing safety is not about replacing humans with machines but about enhancing human capabilities and creating a safer, more sustainable future for all.
Featured Product
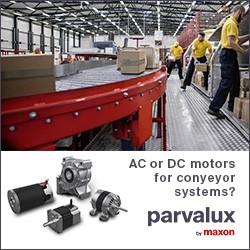