KUKA Robotics to Showcase Advanced Solutions for Packaging and Processing At Pack Expo International
The live cell demonstrations will include autonomous mobile robot (AMR) solutions for intralogistics, robotic palletizing/depalletizing, a robotic bottle capping operation and a food handling system.
SHELBY TOWNSHIP, Mich., July 31, 2024 - Highlighting speed, versatility and flexibility for the packaging and processing industry, KUKA Robotics will feature four innovative robotics cells at PACK EXPO International, Nov. 3-6, at McCormick Place in Chicago, Illinois. The live cell demonstrations will include autonomous mobile robot (AMR) solutions for intralogistics, robotic palletizing/depalletizing, a robotic bottle capping operation and a food handling system.
In booth N-5414, located in the North Building, system integrator Stac Material Handling will use a KMP 1500P AMR and KR CYBERTECH a compact palletizing cell simulating a palletizing process for cardboard boxes in the food industry. The KMP 1500P is KUKA's latest generation of AMRs for Logistics 4.0 and features intelligence, safety and easy commissioning to navigate complex, dynamic environments with the SLAM (Simultaneous Localization and Mapping) navigation method. The AMR platform automatically identifies loads with QR code readers, and 3-D cameras detect obstacles in three-dimensional space.
Automation solution provider Technica International will use a KR IONTEC in the booth to demonstrate depalletizing open-top cardboard can trays. The cell's KR 70 R2100 IONTEC has a maximum reach of 2,101 mm and a rated payload of 70 kg that can subsequently be adjusted even after mounting. KR IONTEC provides users the highest output with a low total cost of ownership and high life cycle efficiency.
KUKA's IONTEC family of robots is an extremely versatile six-axis medium payload robot that can be floor, wall, ceiling or angle mounted, and its optimized design is well-suited to compact cells with a small footprint. Boasting a best-in-class work envelope and equipped with a waterproof and dustproof in-line wrist and protected motors, IONTEC is suitable for virtually any application. The HO variant uses food-compatible H1 oil in all axes to eliminate the potential for contamination in the food processing and manufacturing sectors. Refrigerated and freezer packing applications can also be accomplished with KUKA's QUANTEC PA Arctic, which does not require a cover or heater while working in temperatures down to -30 F.
Additionally, PACK EXPO International attendees will experience the speed and precision of KUKA's high-performance SCARA robot family in a bottle capping cell. The ultra-compact KR 6 R500 Z200-2 SCARA will cap small spray bottles with a cycle time of less than 0.36 seconds. With a maximum payload of 6 kg and a 500 mm reach, the four-axis KR 6 R500 Z200-2 has a serial mechanism with rotational joints in the first two axes, and the remaining axes are combined to allow rotation and linear movement in the Z-axis. The KR SCARA industrial robots are available in a variety of payloads, reaches and Z-axis strokes and are also available in an HO variant for safe food and beverage applications.
To demonstrate how KUKA automation provides food-processing companies with increased production control while avoiding failures and reducing costs, KUKA will highlight a primary food handling solution using a KR DELTA HMhygienic robot. The KR DELTA hygienic robot provides outstanding performance and value for pick-and-place applications in the food, packaging, electronics and pharmaceutical industries. The KR DELTA combines precise grip, corrosion resistance and minimal maintenance requirements to excel in sensitive high-speed production applications. This ceiling-mounted robot offers a reach of 1200 mm, a maximum payload capacity of 3 kg and cycle times as low as 0.5 seconds.
The robot is made entirely from corrosion-resistant stainless-steel that protects against dust and moisture. The design accepts alkaline or acidic high-pressure cleaning and disinfection up to 100 kPa for simplified upkeep and shorter downtimes. Food-sector certified for material safety, the entire robot carries IP 67 high-protection certification, with IP 69K for axis 4 that is also ISO 3 rated for cleanroom applications. The KR DELTA is equipped with KUKA's new KR C5 micro robot controller that reduces full load power consumption by 35%.
PACK EXPO International visitors will be able to see KUKA robots in action and learn more from KUKA representatives from 9 a.m. to 5 p.m., Nov. 3 - 5, and 9 a.m. to 3 p.m. on Nov. 6.
All KUKA automation solutions are backed by the company's expert service and support for training, complete system engineering and simulation, readily available spare parts, robot refurbishment and more, all of which are easily accessible through the my.KUKA.com site.
KUKA
KUKA is a global automation corporation with sales of around 3.3 billion euro and roughly 14,000 employees. The company is headquartered in Augsburg, Germany. As one of the world's leading suppliers of intelligent automation solutions, KUKA offers customers everything they need from a single source: from robots and cells to fully automated systems and their networking in markets such as automotive, electronics, metal & plastic, consumer goods, e-commerce/retail and healthcare.
Featured Product
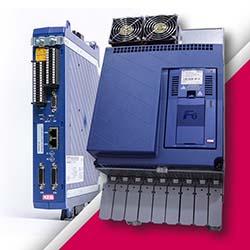