The Future of AI in Predictive Maintenance: How Technology is Revolutionizing Equipment Monitoring
In today's fast-paced industrial environment, maintaining the health and efficiency of machinery is crucial. Downtime can lead to significant financial losses, and traditional maintenance strategies often fall short in predicting equipment failures. Enter Predictive Maintenance powered by Artificial Intelligence (AI) and Machine Learning (ML) - a game-changer in the realm of equipment monitoring and maintenance.
In today's fast-paced industrial environment, maintaining the health and efficiency of machinery is crucial. Downtime can lead to significant financial losses, and traditional maintenance strategies often fall short in predicting equipment failures. Enter Predictive Maintenance powered by Artificial Intelligence (AI) and Machine Learning (ML) - a game-changer in the realm of equipment monitoring and maintenance.
What is Predictive Maintenance?
Predictive Maintenance (PdM) is a proactive approach that utilizes data analysis to predict when equipment will fail, allowing for maintenance to be scheduled just in time to prevent downtime. Unlike traditional reactive or preventive maintenance, PdM leverages advanced technologies to monitor the real-time condition of machinery, thereby optimizing maintenance schedules and reducing costs.
The Role of AI and ML in Predictive Maintenance
AI and ML are at the heart of modern Predictive Maintenance systems. These technologies analyze vast amounts of data from sensors and other sources to identify patterns and predict potential failures before they occur. Here's how they transform maintenance processes:
1. Real-Time Monitoring and Data Collection
AI-powered systems continuously collect data from equipment through sensors that measure various parameters such as temperature, vibration, and pressure. This data is analyzed in real-time, providing insights into the equipment's health and operational status.
2. Advanced Analytics and Pattern Recognition
ML algorithms process the collected data to recognize patterns that indicate normal versus abnormal behavior. By learning from historical data, these algorithms can predict when a component is likely to fail, allowing maintenance teams to intervene before issues arise.
3. Automated Alerts and Notifications
AI-driven systems can automatically alert maintenance teams to potential problems, providing them with actionable insights. These systems can also prioritize maintenance tasks based on the severity and impact of the predicted failure, ensuring that critical issues are addressed promptly.
Benefits of AI and ML in Predictive Maintenance
The integration of AI and ML into Predictive Maintenance offers numerous benefits, making it a preferred choice for many industries:
1. Reduced Downtime and Increased Uptime
By predicting equipment failures before they happen, AI-driven Predictive Maintenance minimizes unplanned downtime. This leads to more efficient operations and increased uptime, ultimately boosting productivity and profitability.
2. Cost Savings
Predictive Maintenance helps in optimizing maintenance schedules, reducing the frequency of unnecessary maintenance activities. This not only lowers maintenance costs but also extends the lifespan of equipment by preventing premature replacements.
3. Improved Safety
By identifying potential failures early, Predictive Maintenance enhances workplace safety. It allows maintenance teams to address issues before they become hazardous, reducing the risk of accidents and ensuring a safer working environment.
4. Enhanced Decision-Making
AI and ML provide maintenance teams with valuable insights into the condition of their equipment. This data-driven approach supports better decision-making, enabling teams to prioritize maintenance activities and allocate resources more effectively.
Real-World Applications of Predictive Maintenance
Predictive Maintenance is revolutionizing various industries, from manufacturing and energy to transportation and healthcare. Here are a few examples of how it is being applied in the real world:
1. Manufacturing
In the manufacturing sector, Predictive Maintenance is used to monitor and maintain machinery such as CNC machines, conveyors, and robotics. Companies like Siemens and General Electric have implemented AI-driven systems to predict equipment failures and optimize maintenance schedules, leading to significant cost savings and improved operational efficiency.
2. Energy
For the energy industry, Predictive Maintenance is crucial for monitoring critical assets like wind turbines, transformers, and power plants. AI technologies are used to predict failures in these assets, helping companies like IBM and Schneider Electric to reduce downtime and maintenance costs while ensuring continuous power supply.
3. Transportation
In transportation, Predictive Maintenance is applied to monitor vehicles, airplanes, and trains. Companies like Rolls-Royce and Delta Air Lines use AI to analyze data from engines and other components, predicting failures and scheduling maintenance to avoid disruptions in service.
4. Healthcare
Healthcare facilities use Predictive Maintenance to ensure that critical equipment, such as MRI machines and ventilators, operate reliably. AI-powered systems help predict potential issues, allowing for timely maintenance and preventing equipment failures that could impact patient care.
The Future of Predictive Maintenance with AI and ML
As AI and ML technologies continue to evolve, the future of Predictive Maintenance looks promising. We can expect more sophisticated algorithms, improved data collection methods, and greater integration with other industrial systems. This will lead to even more accurate predictions, reduced downtime, and optimized maintenance processes across various industries.
Start Your Predictive Maintenance Journey Today!
Are you ready to harness the power of AI and ML to revolutionize your maintenance processes? Our Xpump solution provides cutting-edge Predictive Maintenance capabilities tailored to your needs. Contact us today to learn how we can help you reduce downtime, lower costs, and boost your operational efficiency.
By embracing AI and ML technologies, businesses can transform their maintenance strategies and stay ahead in the competitive industrial landscape. Predictive Maintenance is not just a trend; it's the future of efficient and effective equipment management.
Explore how Einnosys can elevate your maintenance strategy with advanced Predictive Maintenance solutions. Contact us to schedule a consultation or request a demo of our Xpump platform today!
Featured Product
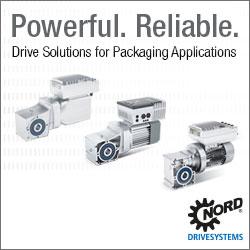