JFD Global Unveils Groundbreaking Submersible with Immersive 3D Printed Model by Malcolm Nicholls Ltd
JFD Global partnered with Malcolm Nicholls Ltd to create a stunning 3D printed model of their new submersible. The model features lights, a submerged TV, and is designed to immerse viewers in the ocean experience. MNL's expertise and advanced technology ensured a high-precision, long-lasting exhibit.
JFD Global, a world leader in subsea technology and maritime solutions, partnered with Malcolm Nicholls Ltd (MNL) to create a captivating 3D printed scale model of their revolutionary agile submersible. This collaboration underscores MNL's reputation for precision engineering in intricate models and prototypes, aligning perfectly with JFD's commitment to pushing boundaries in underwater technology.
Beyond Display: An Immersive Journey
JFD's vision extended far beyond a simple product showcase. They desired to transport exhibition attendees to the ocean depths, alongside the agile submersible. MNL delivered within a demanding six-week timeframe, crafting a functional model complete with integrated lighting on the submersible, a submerged TV replicating the ocean environment, and an illuminated stand proudly displaying the word "Agile."
Uncompromising Precision for Enduring Impact
MNL utilised their state-of-the-art Neo 800 printer and Somos Watershed material to achieve exceptional detail and surface finish. The critical clear viewing portal, a vital component, was vacuum cast to ensure UV stability, guaranteeing the exhibit's longevity. The meticulously crafted 1:10 scale model allowed viewers to appreciate the submersible's intricacies in their entirety.
Advanced Technology Meets Rigorous Standards
Stereolithography (SLA) was selected as the manufacturing process due to its unparalleled accuracy, superior surface finish, and the ability to create all four sections simultaneously. MNL further implemented internal carbon fibre reinforcements within the SLA print to guarantee long-term stability, addressing a potential drawback of the technology. Alternative technologies like Selective Laser Sintering (SLS) and Fused Deposition Modelling (FDM) were deemed unsuitable due to their inherent surface roughness, necessitating extensive post-processing and potentially delaying the project beyond JFD's exhibition schedule.
Collaboration Fuels Success
MNL played a pivotal role in the Computer-Aided Design (CAD) stage, strategically integrating supporting structures for steel support rods. This meticulous approach ensured the model's stability within the demanding exhibition environment. Overcoming technological challenges, MNL utilised detailed renders for client approval, model reinforcements, and meticulous scaling adjustments. Additionally, they created a comprehensive step-by-step assembly guide to expedite the setup process at the exhibition.
A Testament to Collaboration and Innovation
The final exhibit transcended a mere display, becoming a testament to the power of collaboration and innovation. It not only showcased cutting-edge technology but also created an unforgettable experience for all who witnessed it.
Featured Product
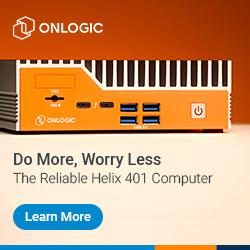