Revolutionizing Winter Sports: CRP USA's 3D Printed Bobsled Parts Propel USA Bobsled/Skeleton Team to Victory
After the officialization of the technology partnership, US-based 3D printing company CRP USA manufactured some functional, race-ready 3D printed parts for the USABS's bobsled to use in the sliding season and Olympic games. The parts improve the athletes' performance guaranteeing increased stress resistance, flexibility, strength, easy changing out.
CRP USA, a leading U.S.-based 3D printing company, has collaborated with USA Bobsled/Skeleton (USABS) to manufacture cutting-edge, race-ready 3D printed bobsled parts, leveraging the innovative Windform family of high-performance materials.
Following the officialization of the technology partnership, CRP USA has played a crucial role in advancing Winter Olympics athletes' performance through the creation of functional, stress-resistant, and flexible 3D printed components for the USABS's bobsled. These parts, including push handles, hand grips, and seats, have been pivotal in optimizing acceleration, minimizing forces, and ensuring enhanced performance during races.
The partnership between CRP USA and USABS aligns with the ongoing project initiated by USABS to develop new bobsleds for the upcoming Olympic Winter Games in 2026. All components are proudly made in the USA through the collaborative efforts of various partners participating in the Made in-USA project.
CRP USA was introduced to USABS by one of their technical partner, a local company specializes in carbon fiber products. Since then CRP USA team of experts and USABS team had different meetings which resulted in a joint effort from both parties on determining the right materials for their components.
The 3D printed parts supplied by CRP USA include: push handles, hand grips, seat.
All these parts are manufactured in Windform materials. While the Push handles are manufactured from Windform SP, hand grips and seats use Windform XT 2.0.
Windform XT 2.0 and Windform SP are two Carbon fiber filled composites from the Windform TOP-LINE range of materials for professional 3D printing, that is Selective Laser Sintering, created by the Italy-based company CRP Technology.
"The big advantage of 3D printing for the USA Bobsled/Skeleton team is that no mold's need to be made" van den Berg specifies, "so a huge amount of time is saved and the costs remain much lower. Not to mention a much faster delivery of the parts because no mold is required. The 3D process also has many advantages because more complex parts can be made."
Saving time and money, together with the possibility of creating complex shapes, are some of the most innate characteristics of 3D printing and undoubtedly the most appreciated. However, the use of 3D printing technology is not the right solution for many of the projects without the right materials.
So specifically, which were the critical issues that the USABS team had to face and overcame with 3D printing and Windform?
"Complying with the regulations, in terms of shapes and dimensions" Marc van den Berg replies "was the main constraint."
Another factor, very important, was the stress resistance.
"During the start of the races" continues van den Berg "there is large forces on the bobsled. Also, bobsled crashes must be considered. For those reasons, the construction materials have to be flexible and strong, in order to avoid parts breakage."
The manufacture of push handles are an excellent example of the efficiency of the 3D printing process combined with the right construction material, especially when supported by a skilled technical staff who is also attentive to the customer's needs.
Nathanael "Nate" Baker, Senior Project Coordinator for CRP USA, comments, "The USABS team needed to easily produce the push handles, in addition to customize the handles based on each athlete and easily change them out."
For these specific components, the CRP USA's evaluation led to the identification of Windform SP as the most suitable construction material for its valuable characteristics of resistance to shock, vibrations and deformation (Density 68 °F: 1.106 g/cc, Density 20 °C: 1,106 g/cc; Melting Point: 380 °F, Melting Point: 193,3 °C; HDT 1.82 Mpa: 368 °F, HDT 1.82 Mpa: 186,5 °C; Tensile Strength: 11000 psi, Tensile Strength: 76,10 Mpa; Elongation at Break: 11.38% just to cite some properties).
As soon as the handles were 3D printed, CRP USA shipped them to USABS, receiving praise for the speed of manufacturing and delivery.
Marc van den Berg and the USABS team were thus able to study, test and modify the parts according to their needs in record time.
Marc explains: "By avoiding the construction of expensive molds, we were able to quickly carry out several tests using slightly different shapes based on the needs that arose from time to time. The speed of execution and delivery by CRP USA allowed us to test the push handles to evaluate their resistance to stress and ergonomics, carrying out the necessary iterations until we achieved the optimal result for us."
"We don't have - says Marc - an official test program, we assemble the parts and use them in a race. And so we did with the 3D printed parts in Windform: This means that the seat, hand grip and rear push handle were immediately tested in a real race!"
Van den Berg and the team were impressed by the performance of the 3D printed bobsled push handles.
"The biggest requirement of the rear push levers - adds Marc - is that they must remain intact if the bobsled crashes, and that is what happened in this race, the bobsled crashed and the handles were not broken!"
"The final results - highlights Marc - were perfect, fast delivery and endless design possible. Hopefully we can 3D print more parts in the future, perhaps even a complete bobsled!"
USA Bobsled/Skeleton is the national governing body for the sports of bobsled and skeleton racing in the United States. Based in Lake Placid, NY, USA Bobsled/Skeleton oversees the development and training of American athletes at all levels of competition, from grassroots programs to the national team.
The 3D printed parts in Windform made their official debut at the IBSF North American Cup (NAC) - from the 15th to the 19th November 2023 - with excellent result: the USABS team won 2-man bobsleigh, Women's monobob, 2-woman bobsleigh and 4-man bobsleigh.
As reported by Abby Slenker on the USABS's website:
The IBSF North American Cup (NAC) kicked off at Mt. Van Hoevenberg, marking the first outdoor competition of the 2023/2024 sliding season for the stars and stripes.
"The athletes have waited a long time to get back on the ice and begin competing," shared Curt Tomesevicz, Director of Sport Performance for USABS. "So, it was very rewarding to see so many great results. It is the reward of a lot of hard work in the off-season."
Featured Product
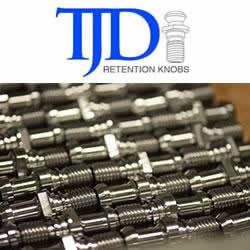