Upwing Energy Announces Cutting-Edge Additive Manufacturing Process for SCS Compressor Module
Upwing Energy, a gas tech innovator and service company, today announced the successful integration of metal additive manufacturing (AM) to its manufacturing process, consistent with the company's commitment to embracing cutting-edge technology.
Upwing Energy, a gas tech innovator and service company, today announced the successful integration of metal additive manufacturing (AM) to its manufacturing process, consistent with the company's commitment to embracing cutting-edge technology. Leveraging Laser Power Bed Fusion (LPBF), Upwing has optimized manufacturing time needed to support its Subsurface Compressor System's (SCS) gas well deployment schedules and maintained exceptional quality and durability in manufactured parts, as demonstrated through extensive testing with Velo3D, a metal 3D printing technology company.
Upwing's patented SCS, which increases the production and recoverability of natural gas from existing wells, employs a multistage hybrid axial compressor, which effectively increases drawdown at the intake and boosts pressure at the discharge. The SCS's compressor module is aerodynamically designed to match well-specific flow parameters for maximum production gain. The rotor design is particularly challenging to manufacture as it requires extremely complex surface geometries. All of the compressor components are manufactured from Inconel 718.
By leveraging metal AM and Velo3D's expertise, Upwing can move from engineering design to full SCS compressor rotor assembly in just 10 weeks' time. Metal AM also allows for the creation of more intricate designs and provides geometric and material benefits resulting in improved part performance and increased part lifecycle. Tensile tests have demonstrated that the material properties of AM Inconel 718 meet the ASTM F3055 requirements as well as the requirements specific to the downhole compressor application.
"All of our work at Upwing is underscored by the belief that continuous improvement is always possible," said Robert McKeirnan, Vice President of Supply Chain and External Manufacturing at Upwing Energy. "Our decision to integrate additive manufacturing makes us more scalable and adaptable. It allows us to create parts that are not only durable, but intricately designed and finished with the highest level of precision."
To compare the mechanical properties of AM components to those produced through machined billet, a standard method across many industries, Upwing performed several tests simulating the conditions found in the SCS's gas compression process. AM parts and billet-produced parts were tested at rotational speeds of 55K RPM or higher, representing the operational overspeed for the SCS.
The parts were then subject to detailed inspection, including using dye penetrant to reveal any surface defects, were balance checked and inspected for dimensional precision. The parts were finally subject to spin-to-burst testing to validate the integrity of each manufacturing method. The additive manufactured parts successfully endured standard operating conditions, and even exceeded overspeed conditions by 2.1 times before failure.
About Upwing Energy
The leading gas tech innovator and service company for responsibly sourced natural gas, Upwing Energy provides a comprehensive integrated End2End (E2E) service, leveraging world-leading subsurface compression technology to help natural gas companies of all sizes boost the production and recoverability of natural gas from existing wells while lowering emissions intensity. The company was formed in 2015 as an innovative offshoot of Calnetix Technologies, the leader in high-speed rotating systems, and exists to secure global energy needs in an economically and environmentally sustainable way. For additional information, visit: https://www.upwingenergy.com/.
Featured Product
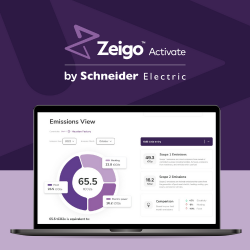