AM Solutions at the Formnext exhibition 2023
Innovative post processing systems ensure higher productivity and cost efficiency for high volume 3D printing
November 7 - 10, 2023, the Formnext exhibition becomes again the international platform for 3D printing by offering access to the latest developments in the field of additive manufacturing. At its booth (hall 12.0, D59), AM Solutions - 3D post processing technology - one of the global leaders in post processing equipment - presents its latest developments. They are characterized by a significantly higher degree of automation and a streamlining approach to the entire process chain. This represents a valuable contribution to a more sustainable and more cost-efficient production.
David Soldan, Head of AM Solutions - 3D post processing technology, enthusiastically explains: „For us the Formnext is the highlight of the year. It is the most important international event in the field of 3D printing and allows the professional exchange of the latest technological developments at the highest level". Besides two innovative new developments the company also presents proven, further developed post processing systems on its 150 square meter booth:
• S1: The most productive and cost-efficient 2-in-1 system for cleaning and surface finishing of polymer parts.
• S2: The solution for high volume production that allows simultaneous cleaning and surface finishing of plastic parts in continuous flow operation.
• S1 Wet: The versatile and consistent wet blasting solution for cleaning and surface finishing of 3D printed metal parts.
• C1: Thanks to perfectly adapted thermal and mechanical effects, the C1 system removes support/resin from photopolymers faster and more effectively than any other system currently available on the market.
Streamlining of the entire process chain thanks to the efficient 2-in-1 solutions
Soldan comments: „Our focus is increasingly on volume production. With our 2-in-1 solutions, we can run two post processing steps in one single machine. This, combined with a higher degree of automation, streamlines the entire process chain and substantially reduces the costs per piece. Such an approach allows us to perfectly fulfill the requirements of customers who are looking for high volume production with 3D printing technologies. One good example is the Italian job shop company Weerg. With the S1 system this company saved not only money by not having to invest in additional equipment but also saved valuable manufacturing space. Above all, the processing time for 3D printed parts could be reduced by over 60%. In the past most of the post processing of delicate, large and geometrically complex components had to be done manually. Thanks to the S1 system, these manual operations could be drastically reduced. The share of mechanically processed components increased from 60 to 90%. „These impressive statistics show that with our unique technological approach we are on the right path and can consistently assist our customers in meeting the additive manufacturing challenges they are facing every day", emphasizes David Soldan.
Product highlights: Chemical smoothing and dyeing in one single process and presentation of the new M4 system
The new C2 system that allows the chemical smoothing and dyeing of 3D printed plastic parts in one single process, is also based on the 2-in-1 principle. Soldan explains: „Our focus is always on developing the best solution for the challenges faced by our customers and the market. Compared to already existing post processing systems we want to generate a substantial added value. For this reason, for the development of the C2 we have taken enough time to develop the best possible process for our customers and make sure that the C2 is productive, cost-efficient, has a small footprint and consistently produces high-quality results".
Besides the C2 system AM Solutions - 3D post processing technology also presents the new and compact M4. This machine is ideal for surface finishing, such as surface grinding, smoothing and, even, polishing of small to midsize metal and plastic parts. The compact system is designed on the plug & play principle, so that time-consuming assembly on site is not necessary. In a smart way, the processing unit and the process water treatment are combined in one system and thus offer optimum ease of operation including an easy-to-understand machine control. The integrated process water cleaning & recycling system with cleaning centrifuge - incl. suitable dirty and clean water tanks - requires no extra fresh and waste water connection. The M4 concept ensures absolute process stability and excellent finishing results. It is also extremely eco-friendly and cost-effective thanks to the recycling of process water.
Close to the customers: New partnerships and customized solutions
Strategic partnerships and networking are also important factors for developing innovative and, at the same time, practical post processing systems. In this respect AM Solutions - 3D post processing technology is very active and will be able to present a few positive surprises at the Formnext exhibition.
Because of non-existing 3D printing standards our customers are frequently faced with numerous challenges. In this respect AM Solutions - 3D post processing technology considers itself not merely as a supplier but also as a valuable partner and consultant. Soldan explains: „We are not only looking at a specific post processing task but, in close cooperation with our customers, are analyzing the entire process chain. Based on this analysis we develop the best possible post processing solution". As an example of this approach at the Formnext exhibition we will present a custom-engineered solution for Sauber Motorsports. The fact that AM Solutions - 3D post processing technology can also realize such projects is possible thanks to a strong and independent parent company. The Rösler Oberflächentechnik GmbH has been active in the demanding field of surface processing for over 80 years with its own development, mechanical engineering, PLC programming in a wide range of industries and at various levels of automation - from high-quality individual part processing to series production.
Visitors interested in the latest post processing developments will find more valuable information at the exhibition booth of AM Solutions - 3D post processing technology in hall 12.0, booth D59 or online under: www.solutions-for-am.com
For over 80 years, the privately owned Rösler Oberflächentechnik GmbH has been actively engaged in the field of surface preparation and surface finishing. As a global market leader, we offer a comprehensive portfolio of equipment, consumables and services around the mass finishing and shot blasting technologies for a wide spectrum of different industries. Our range of about 15,000 consumables, developed in our Customer Experience Centers and laboratories located all over the world, helps our customers to fulfill their individual finishing requirements. Under the brand name AM Solutions, we offer numerous equipment solutions and services in the area of additive manufacturing/3D printing. Last but not least, as our central training center the Rösler Academy offers practical, hands-on seminars on the subjects mass finishing and shot blasting, lean management and additive manufacturing. Besides the German manufacturing locations in Untermerzbach/ Memmelsdorf and Bad Staffelstein/Hausen the Rösler group has a global network of 15 locations and 150 sales agents.
For detailed information please go to: www.rosler.com
Featured Product
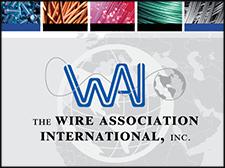