PBC Linear Demonstrates Deeper CNC Integration for Its Applied Cobotics Cobot Feeder
By reliably loading and unloading dunnage trays that a UR cobot can consistently access, this versatile CNC machine-tending tool provides a standardized platform for storing, staging, and delivering parts into a position that the UR cobot can reach for loading and unloading.
PBC Linear (Pacific Bearing Company), a global leader in linear motion solutions, is pleased to announce that it will demonstrate deeper CNC integration for its Applied Cobotics Cobot Feeder at FABTECH 2023, in the Universal Robots (UR) Booth #B17063 in Chicago, September 11-14.
The Cobot Feeder demonstration combines a UR10e with a Flexxbotics FlexxCNC™ to control the process of loading and unloading trays of PBC Linear FL-12 bearings into a pneumatic vise. The modular, flexible, and easily re-taskable Cobot Feeder empowers one machinist to do the work of up to eight while also increasing the amount of raw materials available to cobot machines tending workcells.
"By increasing the amount of raw materials to a workcell, the Cobot Feeder's 17-tray, high-density, part-storage solution enables a machining, welding, stamping, forming, or deburring center to operate for longer periods of time without human interaction, significantly increasing productivity by up to 300% or more," explains Beau Wileman, Applied Cobotics and 3D Platform Product Manager, PBC Linear. "In many cases, this means a cobot workcell operating 8 hours a day during normal business operations can continue to work through shifts two and three, providing lights-out operation around the clock. This considerably increases the cobot workcell's productivity, while overcoming the ‘labor gap' in machine tending manufacturing operations."
Visit us at FABTECH in the UR Booth #B17063 in Chicago, September 11-14.
About Universal Robots
Universal Robots is a leading provider of collaborative robots (cobots) used across a wide range of industries and in education. Founded in 2005 and headquartered in Odense, Denmark, Universal Robots aims to create a world where people work with robots, not like robots. Its mission is simple: Automation for anyone. Anywhere.
Since introducing the world's first commercially viable cobot in 2008, Universal Robots has developed a product portfolio reflecting a range of reaches and payloads and has sold over 50,000 cobots worldwide. An extensive ecosystem has grown around the company's cobot technology creating innovation, choice for customers, and a wide range of components, kits and solutions to suit every application.
For more information, please visit www.universal-robots.com
About PBC Linear
PBC Linear has been a proud member of the Rockford-area manufacturing community since 1983. The company has created and patented innovative linear motion solutions and has greatly expanded its technology, expertise, and services to become a complete linear motion manufacturer. Through its partnerships in Europe and Asia and its worldwide network of distributors, PBC Linear has positioned itself as a trusted global leader in bearing products and linear motion technology.
Featured Product
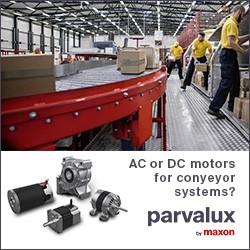
Strain Wave Gearheads by maxon - Highly precise, compact, and efficient.
Strain wave gearheads are ideal for use in applications requiring precision motion control and high torque transmission in a compact design. maxon strain wave gearheads are a specialized type of gearhead where precision and compact design are crucial. This type of gearhead is often used in applications in a confined space. With their advanced gear tooth design, maxon's strain wave gearheads provide high efficiency and good back drivability. Typical applications include:
Robotics, Aerospace, Medical technology and Optical systems
.