DCM Tech to Exhibit Automated Metal Grinding Equipment at FABTECH 2023
The categories the company will feature are precision metal grinding, punch and die maintenance, and metal additive manufacturing (AM). DCM Tech plans to demonstrate how important segments of FABTECH’s core audience can quickly and easily incorporate automation to streamline their process.
To assist metal fabricators and finishers in dramatically increasing quality and productivity, DCM Tech will exhibit state-of-the-art, automated metal grinding equipment in three key categories at FABTECH 2023, Chicago, September 11-14, 2023, in Booth A6431.
The categories the company will feature are precision metal grinding, punch and die maintenance, and metal additive manufacturing (AM). DCM Tech plans to demonstrate how important segments of FABTECH's core audience can quickly and easily incorporate automation to streamline their process.
For high-efficiency precision metal grinding, the IG 282 SD rotary surface grinder - with 24" table diameter, servo driven precision Z- and X-Axis, and 20HP or 30HP grinding spindle motor - has numerous new features that will bring precision, efficiency, and technology to industrial grinding processes. These include "robot-ready" versions for easy connection and integration with third party robotic arms; a variable speed rotary table and grinding spindle; variable strength electromagnetic chuck with electronic sensed demag cycle; thru-table vacuum hydraulic/pneumatic port, programmable speed & feed rates; and convenient storage of grind recipes for rapid changeover.
For automated punch and die maintenance to boost productivity, DCM Tech's Punch and Die Grinder (PDG), a 5-HP rotary table surface grinder, is a turnkey package that features autofeed control, self-dressing CBN abrasives, through-spindle coolant, and universal fixturing that accepts Amada, Trumpf, Salvagnini, Finnpower, Weideman, Whitney, and other style tooling. The PDG's automatic feed eliminates potential problems due to inconsistent manual operation. Once an operator sets up the tooling to be sharpened and starts the machine, he can leave and tend to other work. The PDG will automatically stop after feeding the selected amount of material and shut down the machine on completion of the process.
To streamline metal AM with improved 3D printer, build plate resurfacing, DCM Tech's IG series offers variable speed grinding with automation and controls that allow virtually any operator to successfully manage a unit. These units can control the initial contact between the abrasive wheel and the build plate, which in the past had to be finessed by the operator. Advanced sensor technology detects vibration and can automatically fine-tune not only the pressure of the spindle motor but also how quickly it moves the wheel down onto the build plate. When the machine senses the abrasive wheel has contacted the build plate, it automatically begins the grind cycle.
DCM Tech is a leading designer and builder of industrial rotary surface grinders and is based in Winona, MN.
For more information: call (800) 533-5339; email info@dcm-tech.com; visit www.dcm-tech.com; or write to DCM Tech at 4455 Theurer Blvd, Winona, MN 55987.
Featured Product
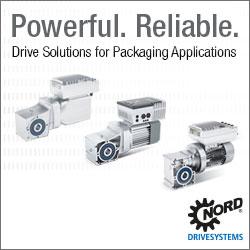
NORD Delivers Powerful, Reliable Drive Solutions for Demanding Packaging Applications
When you need quality, flexibility and high efficiency, NORD has you covered with complete drive solutions for primary and secondary packaging, end-of-line packaging, and higher-level applications. NORD supports you through the entire life cycle of your drive systems with pre-sales engineering support, online tools, and a global service network. Drive systems for both vertically and horizontally networked technology with all the options for sensor incorporation and integration into the higher-level control system.