Aerobotix and FerRobotics to exhibit new Active Taping Kit (ATK) tool at Automate 2023
First public demonstration in North America of revolutionary robotic tool for precision application of masking tape
Aerobotix and FerRobotics, two leading robotics companies based in the U.S. and Austria respectively, today announced they will exhibit their new Active Taping Kit (ATK) tool at Automate 2023 in Detroit, Michigan, from May 22-25. This will be the first public demonstration of the ATK in North America.
Aerobotix and FerRobotics partnered on the ATK in response to aerospace industry demand for an automated tool for precision application of masking tape. Collaboration between engineers from the two companies led to the development of a revolutionary End of Arm Tooling (EOAT) after months of prototypes and testing.
FerRobotics' patented Active Compliant Technology (ACT) enables a robot to use varying force when applying tape to an aircraft. The ATK allows for smooth masking on parts varying in shape, putting down perfectly straight tape lines where the customer needs them.
"Customer demand for masking-tape automation was always there, but until now, the technology wasn't," said Kent Pfeifer, Aerobotix lead process engineer. "The ATK solution we've developed with FerRobotics has the smarts and sensitivity to apply tape repeatably every time.
The ATK features precision control of all individual process parameters - contact force, cutting, and tape consumption. The ready-to-use solution is highly durable and designed to apply various kinds of tapes on any part or surface with exact repeatability. It delivers perfect results without bubbles or wrinkles.
The ATK exceeded expectations for precision and reliability when it underwent testing at Aerobotix's in-house process laboratory - a facility housing a range of automated systems used to paint, cure, sand and inspect products for aerospace and defense customers.
In November, the ATK was honored as one of only five projects to be nominated for the Econovius, a special prize under the Austrian National Innovation Award. The successful nominees were selected from more than 400 entries. The Austrian Federal Ministry of Science, Research and Economy presents the ANI Award annually to encourage companies to develop innovative products that contribute to the country's economic growth.
Aerobotix and FerRobotics will exhibit in Booth 3813 at Automate 2023.
To watch a video about the Active Taping Kit (ATK) tool, click here: https://www.youtube.com/watch?v=gM4216UHQas
About Aerobotix
Headquartered in Huntsville, Alabama, Aerobotix is an innovative leader in robotic solutions for the aerospace and defense industries. The company specializes in the creation of cutting-edge automated robotic solutions for high-value, high-precision components, aircraft and vehicles. Aerobotix has more than 130 robotic systems installed in the U.S. and abroad, providing exceptional results and savings for our clients.
About FerRobotics
FerRobotics is the global leader in the development and distribution of sensitive robotic elements (for robotic material removal end-of-arm tooling/surfacing finishing end-of-arm tools/end-effectors) that equip an industrial robot or cobot with contact intelligence and real force control. We give robots feeling with our patented Active Compliant Technology. And this ensures more efficient, finer, and more valuable production results. Our products close automation gaps seamlessly and are trendsetters in flexible automation in numerous industries on the international market. Our experts will happily show you solutions for your applications (robotic grinding, sanding, polishing, brushing, deburring, taping, etc.) or other requirements.
Featured Product
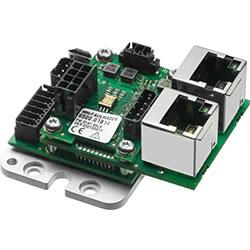
MOTION CONTROLLERS FOR MINIATURE DRIVES AND MICRODRIVES
FAULHABER has added another extremely compact Motion Controller without housing to its product range. The new Motion Controller is ideal for integration in equipment manufacturing and medical technology applications. With 36 V and 3 A (peak current 9 A), it covers the power range up to approx. 100 W and is suitable for DC-motors with encoder, brushless drives or linear motors.