Transforming Additive Manufacturing with GEMCO’s Advanced Mixing and Drying Tech
GEMCO, a leading provider of engineered solutions for mixing and drying equipment, continuously enhances its equipment with a goal to accelerate and improve additive manufacturing (AM) powder. With over 100 years of experience in the powdered metal industry, GEMCO's mixing and drying technology delivers superior homogeneity, final chemistry, and flow properties of engineering-grade metallic, ceramic, and plastic powders for AM powder manufacturers.
Did you know that over 3000 years ago, Egyptians and Incas used iron powders to fabricate objects? And in India, metallurgists created a 6.5-ton Delhi column from iron powder, which still stands after 1,600 years without rusting or decomposing. Although using metal powders is an old practice, faster object production is accelerated with 3D printing. Thanks to newly developed mixing and drying equipment, 3D materials made of metal, ceramic, and plastic, now perform better in terms of strength and durability.
According to GEMCO's President and CEO Casey Bickhardt, "Mixing and drying have a direct correlation to the performance, strength, and durability of 3D metal, ceramic, and plastic-based materials. Our additive manufacturing mixing and drying equipment is a cost-effective and flexible alternative to designing and manufacturing 3D metallic, ceramic, and plastic powders for high-value components and critical applications in all the AM powder markets."
Design aspects unique to AM powders include gas purging and coating, which require an internal filtering system that delivers the carrier to the powder and not to the exhaust system. Vacuum integrity is critical to eliminating contamination ingress into the product. "While most manufacturers won't discuss leakage rates, it's critical," says Bickhardt.
GEMCO's success is attributed to the proven tumble technology pioneered by the company for 100 years. "Our experience as the No. 1 mixer in the pharmaceutical industry and being trusted by the FDA has let us become the leader in blending science and technology," says Bickhardt. "Our unique design facilitates the reaction, homogenizing, drying, cooling, and reclamation processes all in one machine. This equipment represents the shortest processing for AM metallic, ceramic, and plastic powder mixing and drying. Reclamation allows for the re-use of expensive, unused portions of the AM powders without the need to purchase additional equipment. Waste is significantly reduced."
GEMCO's AM mixing and drying equipment features a tough, proven design that guarantees outstanding service life and reliability, lower maintenance costs, vacuum drying that allows the process to proceed faster and at lower temperatures, lot sizes ranging from 10 kg to 1800 kg with full traceability of the different batches blended, and 316 stainless steel contact parts with pharma-grade finishes to prevent lot-to-lot contamination.
For those looking to develop new or improved processes for their powders, GEMCO's Tech Center is a large prototype-to-production facility that can bridge the gap between prototyping and manufacturing. As Bickhardt notes, "At GEMCO, we are dedicated to providing innovative solutions that help our customers achieve their goals."
To learn more about additive manufacturing and how mixing and drying technology can help manufacturers achieve superior results, visit us at the upcoming Rapid + TCT 2023 Conference at booth #4260 or contact GEMCO.
Featured Product
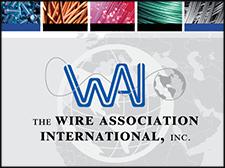