Tempus 3D now offers Cerakote finishing to Enhance the Performance of 3D Printed Parts for the Canadian market
Cerakote ceramic coating has been adopted by industry giants such as Boeing, SpaceX, Blue Origin, Ford and Lamborghini because of it's ability to enhance the performance and aesthetics of end-use parts. The many benefits include increased scratch resistance, wear resistance, waterproofing, chemical resistance, impact strength, and UV protection. This finish is now experiencing rapid adoption in the 3D printing world. Tempus 3D, a Canadian 3D printing service bureau, has now added Cerakote as part of it's product and service offering.
Tempus 3D is proud to announce the addition of Cerakote to it's product offering for the Canadian market. Cerakote Ceramic coating is a world-leading thin-film coating that is applied to plastic, metal and other materials to enhance their physical performance and appearance including scratch resistance, wear resistance, waterproofing, chemical resistance, and UV protection.
Industrial Applications of Cerakote
The performance-enhancing properties of Cerakote make it a logical choice for a wide variety of industries and manufacturing processes. For example, Cerakote is used for corrosion protection in the oil and gas industry, heat resistance in the aerospace sector, performance coatings in the automotive industry, extending the life of sporting and hunting equipment, and increasing the useful life of jigs and fixtures. Recommended applications include tools, consumer goods, eyeglasses, sporting equipment, robotics, electronics, fresh and saltwater applications and other applications where a durable performance coating is required.
A wide variety of manufacturers and suppliers rely on Cerakote coatings including Boeing, SpaceX, Blue Origin, Lockheed-Martin, US Department of Defence, Zipline, Ford, and Lamborghini.
Benefits of Cerakote
Destructive testing has shown the superiority of Cerakote to other standard finishes. For example, a Taber abrasion wear test was performed by NIC Industries to compare the durability of Cerakote to 6 other popular coatings. In this test, Cerakote lasted nearly twice as long as the nearest competitive finish and 24 times as long as the furthest competitive finish.
Another study tested the impact resistance of Cerakote. In this test, a 1 oz slug was fired from a 12-gauge shotgun at a piece of metal plate treated with Cerakote. The area behind and surrounding the impact site showed no cracking or loss of adhesion, even in the areas of greatest deformity.
Cerakote in Additive Manufacturing of Plastic Parts
Cerakote is an increasingly popular finish used in additive manufacturing because it's ability to enhance the performance and aesthetics of 3D printed plastic parts. This diversifies the potential end-use applications of the parts; for example, Cerakoted plastics are emerging as faster, less expensive alternatives to metal parts, especially for small-to-medium volume manufacturing. An example is provided in this case study, where HP and Aerosport re-designed 2 different metal assemblies to be 3D printed with Nylon 12. Each was able to reduce assembly time, weight, cost of manufacturing and overall production times by a significant amount.
To validate the performance of Cerakote when applied to 3D-printed plastic parts, the Cerakote Technical Training Team completed ASTM testing on Nylon PA12 plastic coated with 2 different types of Cerakote finishes. The tests showed excellent results, including no chipping or cracking in cross-hatch adhesion tests, and minimal effect after 24-hour immersion in water, acetone or diesel.
Get Started With Cerakote Coating for 3D Printed Parts
Tempus 3D is a qualified Cerakote applicator located in British Columbia, Canada. Tempus offers Cerakote finishing for clients across Canada and the US, both as an extension of it's additive manufacturing business and as an independent service.
If you are interested in learning more about Cerakote,and it's use in manufacturing you can visit our guide to Cerakote at www.tempus3d.com/cerakote-finish-for-3d-printed-parts.
To request a quote, please contact our team at info@tempus3d.com or through our contact us page. We look forward to working with you!
Featured Product
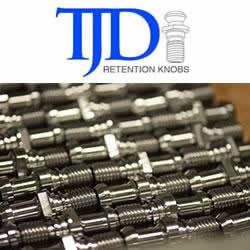