AutoStore Releases New Research Report: “Five Challenges for Warehouse Management and Fulfillment in 2023”
Survey of 300+ C-level executives finds that reducing costs and investing in automation technology are top priorities
NEDRE VATS, Norway - January 26, 2023 - Today AutoStore™ launches a new benchmark report with insights from over 300 C-level business leaders in warehouse management and fulfillment. Survey participants identified the top three current challenges facing organizations as: rising energy costs (32%), increasing labor costs (27%), and supply chain and shipping constraints (26%).
"There is a need to operate more efficiently, which is perhaps why nearly 9 in 10 organizations either have, or are planning to install, automation technology in their warehouse in 2023," said Ellen Brune, Head of Global Strategic Accounts at AutoStore. "The intention to meet a challenging macro environment with a technology uptake is good news for customers who want their products quickly."
AutoStore surveyed executives from North America, Europe, and Asia Pacific for the report. European respondents (44%) cited energy costs as a top challenge, compared to North American and Asia Pacific respondents (24%). Conversely, rising labor costs are more of a concern in APAC (34%) and North America (27%), compared to Europe (22%).
Efficiency-Enhancing Technology
According to the industry business leaders, the most important focus areas for 2023 are improving customer satisfaction levels (34%), investing in automation technology (31%), sustainable solutions (31%), greater workforce efficiency (31%), and delivering goods-to-person faster (30%).
A large majority of respondents (88%) shared that they will implement an automated storage and retrieval system by 2024. Thirty-two percent have some sort of automation technology in place already and 56% are making plans to deploy it in the next 12 months.
"Automation technology has shifted to where it is no longer a ‘nice to have' in the warehouse, but an absolute must have," said Marcus Mogéus, Chief Marketing Officer at AutoStore. "This report shows that the investment plan for companies when it comes to automation technology has increased dramatically from previous reports."
Push for Space Efficiency
The report shows that approximately one in three industry business leaders cite sustainability as a key priority for 2023. Energy efficiency (55%), reducing waste (46%), employee well-being (43%), reducing storage footprint (39%), and recycling (36%) were the most important initiatives. Conversely, when asked what brands are looking for from AS/RS providers, sustainability decreased in priority (13%).
In comparison, respondents cited reliability (24%), simplicity (22%), and space utilization (20%) as more important attributes. In fact, 43% said space saving/utilization will be mission critical to their business and 49% cited it as a very important business priority.
"Space is critically important for organizations. We help businesses reduce costs, become more efficient, and deliver a complete ROI in one to three years, while reducing a warehouse footprint by 75% when compared to conventional storage," said Brune. "Optimizing space closely aligns with the challenge of rising costs."
For more information about the report, go to https://www.autostoresystem.com/insights.
About AutoStore | www.autostoresystem.com
AutoStore™, founded in 1996, is a warehouse robot technology company that invented and continues to pioneer cube storage automation, the densest order-fulfillment solution in existence. Our focus is to marry software and hardware with human abilities to create the future of warehousing. AutoStore is global, with over 1,000+ systems in 46 countries in a wide range of industries. All sales are distributed, designed, installed, and serviced by a network of qualified system integrators referred to as "partners". The headquarters is in Nedre Vats, Norway, with offices in Oslo (Norway), the U.S., UK, Germany, France, Spain, Italy, Austria, South Korea, Japan, and Singapore.
The AutoStore System consists of an aluminum Grid, Robots, Bins, Ports, and a Controller. The stacked Bins are arranged in a Grid. Robots ride on rails along the top of the Grid, retrieving Bins as needed. The Bins are then delivered to a Port, where warehouse operators are stationed to pick up or fill in products, tag, pack and send them out. A Controller acts as the brain behind the whole operation.
Featured Product
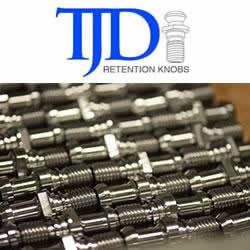
T.J. Davies' Retention Knobs
Our retention knobs are manufactured above international standards or to machine builder specifications. Retention knobs are manufactured utilizing AMS-6274/AISI-8620 alloy steel drawn in the United States. Threads are single-pointed on our lathes while manufacturing all other retention knob features to ensure high concentricity. Our process ensures that our threads are balanced (lead in/lead out at 180 degrees.) Each retention knob is carburized (hardened) to 58-62HRC, and case depth is .020-.030. Core hardness 40HRC. Each retention knob is coated utilizing a hot black oxide coating to military specifications. Our retention knobs are 100% covered in black oxide to prevent rust. All retention knob surfaces (not just mating surfaces) have a precision finish of 32 RMA micro or better: ISO grade 6N. Each retention knob is magnetic particle tested and tested at 2.5 times the pulling force of the drawbar. Certifications are maintained for each step in the manufacturing process for traceability.