UltiMaker Launches the S7 - The New Flagship S-Series 3D Printer
The UltiMaker S7 builds on the award winning S-Series printers, with new features including an integrated Air Manager and a flexible build plate which takes ease-of-use and reliability to a new level
UltiMaker, a global leader in desktop 3D printing, today announced the launch of the UltiMaker® S7 - the latest entry in the company's best-selling series of 'S' 3D printers.
"Over 25,000 customers innovate with the UltiMaker S5 every day, making the award-winning machine one of the market's most used professional 3D printers," says UltiMaker CEO Nadav Goshen. "With the S7, we took everything our customers loved about the S5 and made it even better." The UltiMaker S7 introduces a range of new features designed for ease of use and print reliability. A new flexible build plate makes removing prints a breeze and the integrated Air Manager filters out up to 95% of UFPs and improves temperature regulation. The S7 also features improved automated bed leveling for reliable first-layer adhesion.
Material partner, igus - who aims to deliver plastic materials for longer life - had the opportunity to preview the S7 and test the system. Their AM Development Engineer, Niklas Eutebach states: "We saw that the new bed leveling system on the S7 really helps us print very precise parts with the right mechanical properties using our materials."
Advances in temperature regulation on the S7 allow users to capitalize on the large 330 x 240 x 300 mm build volume - with reliable accuracy from the first printed layer to the last. The flexplate also provides easy part removal post printing, reducing labor so users can get on with other tasks.
Luke Taylor, Marketing Manager at Polymaker - a producer of high-performance 3D printing materials - also had the chance to test the S7 with a real customer application, printing a carbon fiber mold for the spoiler of a race car. "This part is just about as big as you can print on the S7," he explains. "It has some sharp corners, so I thought we could test out the adhesion to the new flexplate, and see how our CoPA material works with such a large part. And the results were great!"
The S7 will be compatible with the UltiMaker ecosystem of over 200 materials and offers seamless integration with industry-leading software, UltiMaker Cura, easy printing with the widest range of materials on the market, and support dedicated to customer success. "Of all the ecosystems that are available, the UltiMaker ecosystem is the most comprehensive," states Taylor.
With the S7 Pro Bundle, users can also pair the S7 with the UltiMaker Material Station to print with up to six spools with automatic material switching and humidity control.
"The UltiMaker S7 is a fantastic addition to our S-Series of printers," says Goshen, concluding, "As more customers are using 3D printing to grow and innovate their business, our goal is to provide them with a complete solution to be successful. With the new S7, customers can be setup and running in minutes: managing printers, users, and designs with our Digital Factory software, improving their 3D printing knowledge with e-learning courses on the UltiMaker Academy, and choosing from hundreds of materials and plugins using the UltiMaker Cura Marketplace."
To learn more about the S7, visit https://ultimaker.com/s7
Featured Product
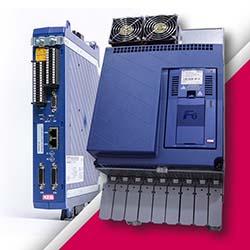
KEB VFDs for High Speed Motor Control
KEB's VFDs are the key to unlocking peak performance in your high-speed machinery. Engineered for precision control, even without feedback sensors, our F6 and S6 drives utilize advanced software and high-frequency output. This ensures smooth operation, reduced vibration, and optimal efficiency. Whether you're building turbo blowers, power generation systems, or other high-speed applications, KEB VFDs deliver the reliability and performance you need.