Toyota Cuts Manufacturing Costs with Zortrax 3D Printers
Toyota’s factories in Poland mount engines in the cars assembled in Europe, where the vehicles hit the roads, satisfying all the customers, who value comfort and reliability most. Toyota hires more than 3 thousand employees, and thanks to optimized processes, they meet the needs of the ever-growing automotive market. To shorten the manufacturing time of various instruments and reduce the production costs, the factories use Zortrax 3D printing solutions.
Toyota's factories in Poland mount engines in the cars assembled in Europe, where the vehicles hit the roads, satisfying all the customers, who value comfort and reliability most. Toyota hires more than 3 thousand employees, and thanks to optimized processes, they meet the needs of the ever-growing automotive market. To shorten the manufacturing time of various instruments and reduce the production costs, the factories use Zortrax 3D printing solutions.
Toyota's facilities in Poland have been using Zortrax 3D printers for years, investing more than 100 thousand PLN into additive manufacturing equipment. Zortrax M300 Plus is a part of their 3D printing lab. Due to the printer's reliability and low maintenance costs, it is used for manufacturing tools optimizing workflow at assembly lines. More and more percentage of such factory tools are now being 3D printed in LPD technology.
"3D printing is not that much about manufacturing time, as it is not the fastest technology on the market, but it surely is the most flexible. We do not have to store spare parts, because we can 3D print them on demand. We can optimize our projects freely since 3D printers materialize nearly all geometries imaginable. We can start a 3D printing process whenever such a need occurs. We don't have to wait until our tooling department, or an outsourcer, has the capacity to take care of our orders. 3D printing shortens waiting time for needed tooling from weeks to days, or sometimes even hours," says Łukasz Kondek, the engineer responsible for 3D printing in Toyota.
The parts 3D printed at the Toyota plant fall into four categories: positioning jigs, assembly jigs, assembly tools and covers. The components 3D printed on Zortrax M300 Plus are often combined with parts, which are made using other manufacturing technologies. One of the gauges used at Toyota has a 3D printed body and pins that contact metal surfaces, which were made of nylon on CNC machine tools to increase durability. This way, Toyota engineers have managed to significantly extend the life of these instruments. Early prototypes were used for more than six months before they wore out. And when that happened, it took just 7 hours to print new ones.
"One of the key benefits of implementing Zortrax 3D printers in manufacturing & industry is their tried and true, stable construction and ease of maintenance. That means that global manufacturers like Toyota can rely on them while printing equipment critical to keeping the assembly line running. Reliability is essential, as even short delays can generate losses that far exceed the value of the printers themselves. Therefore, what we offer large industrial customers is the assurance that our 3D printers will perform as they should every time." - says Michał Siemaszko, Head of Research and Development at Zortrax.
Before Toyota started using 3D printers, assembly line jigs were manufactured by a separate department equipped mainly with CNC machines. Therefore, engineers had to design these tools with the constraints imposed by traditional manufacturing technologies. 3D printers, such as Zortrax M300 Plus solved this problem, significantly reduced costs, and shortened lead times. The entire investment in 3D printing equipment used at Toyota's factories in Poland paid for itself in one year.
About Toyota Motor Manufacturing Poland (TMMP):
TMMP has two plants located in Lower Silesia. The Walbrzych plant produces electric transmissions for low-emission hybrid cars with 1.8-liter, 1.5-liter and 1-liter gasoline engines, as well as manual and semi-automatic transmissions. Its current annual production capacity reaches 350,000 electric hybrid transmissions, 258,000 engines and 633,000 transmissions. The Jelcz-Laskowice plant produces 1.5-liter and 2.0-liter TNGA gasoline engines, with an annual production capacity of 312,000 drive units. TMMP's factories supply the car assembly plants of Toyota, the Stellantis concern and Lotus, operated by European companies in the Czech Republic, the United Kingdom, France, Turkey and Russia, and outside Europe: in South Africa and Japan.
About Zortrax
Zortrax is an established manufacturer of 3D printers for both desktop and industrial sectors. The products offered by the company operate in four technologies: LPD, LPD Plus, UV LCD and SVS. The brand has built a strong position on the market by offering comprehensive solutions for 3D printing, including: printing materials and peripherals as well as dedicated Z-SUITE software and Zortrax inCloud platform for remote management of the printing process and personnel. Zortrax machines are used by thousands of customers around the world in industries ranging from architecture, medicine, education, design, automotive, engineering, industry to aerospace. This has enabled the company to build a business on an international scale. The company achieves this goal by providing devices that are reliable and precise, adapted to work in harsh environments, meeting the most stringent standards, and at the same time, are intuitive and easy to use. The company manages to create such quality 3D printers by cooperating with three key sectors: education, medicine and space. Zortrax engineers developed the technology to print composite models from two PEEK blends in collaboration with the European Space Agency. Zortrax specialists in cooperation with ESA, have also developed 4D printing technology, where 3D models can change their geometry under the influence of external stimuli. Within the project, the first successful demonstrators with electrically activated movement were printed on Zortrax M300 Dual. Zortrax solutions are used by such giants as: NASA, Toyota and Bosch.
Featured Product
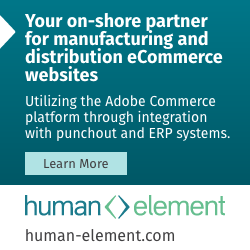