AMADA WELD TECH Releases WM-200A Industry 4.0 Ready Networked Weld Monitor
Simplifies resistance welding data capture, storage, and analysis on a network platform
MONROVIA, CA - AMADA WELD TECH, Inc., a leading manufacturer of welding, marking, cutting, sealing, and bonding technology, announces the release of the IIoT ready WM-200A Networked Resistance Weld Monitor, which enhances resistance weld monitoring capability by simplifying data capture, storage, and analysis on a networked platform, paving the way to next generation artificial intelligence and machine learning features.
Whether connected to a standalone resistance welding station, or implemented in a fully automated system, the WM-200A enables users to collect large amounts of high-resolution process data to be used for manufacturing traceability, statistical data analysis, equipment efficiency and health. Data can be stored on an on premise or cloud based server and viewed or downloaded from a remote location using the remote graphic user interface.
The WM-200A monitored inputs include current, voltage, displacement, and force. The monitor features an intuitive user interface for easy programming and quick access to view waveform and numeric data. Configurable monitoring screens enable custom viewing. The WM-200A offers high resolution data capture (up to 200 kHz sample rate) and can simultaneously monitor eight different inputs and up to four distinct windowed process limits per primary channel.
The WM-200A communicates with direct I/O and TCP/IP communication protocols; optionally, configure with an EtherNet/IP field bus to allow automated systems to communicate easily over a single communications cable. Typically, WM-200A is connected to a large display on a personal computer for easy setup and viewing of waveforms and data via WM-Inspect software GUI. Stored data is accessible by third party software suites for analysis for SPC, OEE, and equipment health. The data is also available for current and future AI/ML software algorithms.
Featured Product
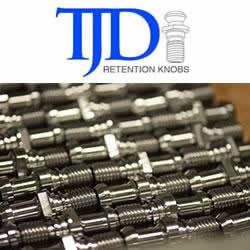
T.J. Davies' Retention Knobs
Our retention knobs are manufactured above international standards or to machine builder specifications. Retention knobs are manufactured utilizing AMS-6274/AISI-8620 alloy steel drawn in the United States. Threads are single-pointed on our lathes while manufacturing all other retention knob features to ensure high concentricity. Our process ensures that our threads are balanced (lead in/lead out at 180 degrees.) Each retention knob is carburized (hardened) to 58-62HRC, and case depth is .020-.030. Core hardness 40HRC. Each retention knob is coated utilizing a hot black oxide coating to military specifications. Our retention knobs are 100% covered in black oxide to prevent rust. All retention knob surfaces (not just mating surfaces) have a precision finish of 32 RMA micro or better: ISO grade 6N. Each retention knob is magnetic particle tested and tested at 2.5 times the pulling force of the drawbar. Certifications are maintained for each step in the manufacturing process for traceability.