Spark Laser gets their product to market faster with Tempus 3D's industrial 3D printing service
Spark Laser was able to transition seamlessly from product development to lon-demand manufacturing when releasing their new commercial laser cutter, with the help of Tempus 3D's industrial 3D printing service.
Spark Laser is a business based in Vancouver, BC that specializes in the design and manufacturing of commercial laser cutting machines. Spark Laser was looking for a local manufacturer that was able to rapidly produce low-volume production runs of prototypes and end-use plastic parts that were robust enough for an industrial environment, and affordable enough to keep their production costs down. With approximately 40 unique plastic parts to manufacture, traditional methods like injection molding would costs thousands of dollars and months to produce, without the flexibility to do on-the-fly design modifications.
Spark Laser approached Tempus 3D to find a quicker and more adaptable manufacturing solution. With HP Multi Jet Fusion 3D printing technology, Tempus 3D was able to quickly build multiple iterations of their prototype parts with Nylon PA12, which provides the quality, consistency, and aesthetics they needed. The same 3D printing technology is used to manufacture the end-use parts on an on-demand basis, allowing Spark Laser to seamlessly scale production and bring their product to market more quickly and easily.
Tempus 3D continues to support Spark Laser with the production of parts and are both heavily invested in bringing manufacturing back to Canada. As Spark continues to see increasing demand for their products Tempus is there to help them scale and meet their production needs. We at Tempus feel this is just the beginning of what manufacturing will look like in the future and it will be more responsive, more custom, and more local allowing innovators across sectors to bring products to market quicker and in a more environmentally friendly way.
Featured Product
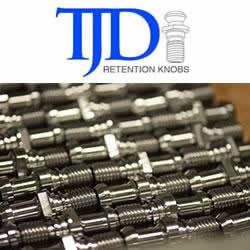