6K ADDITIVE INTRODUCES ULTRA-LOW OXYGEN TITANIUM POWDER HELPING CUSTOMERS INCREASE QUALITY WHILE LOWERING OVERALL PRINT COST
The availability of 500-700 ppm titanium powder significantly expands the number of parts that can be printed from a manufactured lot while maintaining material specifications
North Andover, MA, November 15th, 2022 - 6K Additive, a division of 6K, a leader in the sustainable production of engineered materials for additive manufacturing and lithium-ion batteries announced today the immediate availability of ultra-low oxygen titanium 64 with parts per million range of 500 - 700. 6K Additive's ability to deliver titanium at these low oxygen levels at production scale greatly surpasses what is available for additive manufacturing today. 6K Additive's ultra-low oxygen titanium provides customers with an extremely high-quality material that enables them to get additional print jobs through their additive manufacturing systems without sacrificing quality. The low oxygen Ti64 effectively lowers users' overall cost for titanium parts with powder that stays with-in printable specification longer.
Mark Barfoot, director of AM programs at EWI commented, "When we talk to Ti64 users in the market, quality always is top priority with costs following a close second. Increasing the value of their Ti64 purchase by extending the life of the powder with more uses is a definite win."
6K's UniMeltĀ® platform offers multifaceted sustainability benefits like no other material production platform in the world. 6K Additive recently commissioned Foresight Management to conduct a life cycle assessment of both their titanium and nickel powders. This study was conducted to quantify the environmental impacts associated with the production of printable metal powders and specifically compare atomization technology methods to 6K Additive's. It was found that for Ti64, 6K's UniMelt process at minimum delivered a 74% energy reduction and 78% carbon emission reduction from traditional processes. The independent studies can be download here.
In addition to low oxygen (500-700ppm) Ti64, 6K Additive produces a full suite of AM powders including Ni718, Ni625, stainless steel 316/17-4, copper 18150, GRCOP, refractory powders including tungsten, tantalum, and rhenium.
Notes for Editors
6K press releases are available here: https://www.6kinc.com/about/news/
About 6K
With sustainability at its core, 6K was founded in North Andover, Massachusetts, has developed UniMeltĀ®, a proprietary advanced microwave plasma production system, to transform engineered materials into revolutionary products that advance industries across additive manufacturing, renewable energy, aerospace, consumer electronics, and more. 6K represents 6000 degrees, both the temperature of the operation of UniMeltĀ®, the world's only microwave production scale plasma system, and the temperature of the sun's surface.
The 6K Energy division is focused on the production of low-cost, sustainable, and domestically produced battery material accelerating the pace of battery production and adoption of electric vehicles. The 6K Additive division specializes in sustainably sourced, AM metal powders production and reclamation, using a proprietary milling and cleaning process that ensures contamination-free, high-quality powders. For more information, visit www.6Kinc.com and follow @6KInc on Twitter.
Featured Product
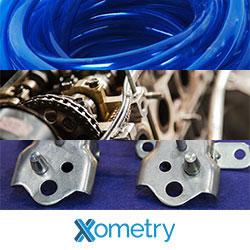