Spark Laser was able to reduce time-to-market and development costs with Industrial 3D printing
Spark Laser was able to transition seamlessly from product development to on-demand manufacturing when releasing their new commercial laser cutter, with the help of industrial 3D printing and Tempus 3D.
Spark Laser is a Vancouver, BC based manufacturer of commercial and industrial lasers. They are building desktop lasers for customers across Canada and the United States. Their lasers are designed specifically to address a gap in the laser market by providing a high-quality and cost-effective solution for customers not wanting to spend hundreds of thousands of dollars on industrial-sized products. The founder of Spark Laser, Yousef Javaher, was looking to manufacture these lasers locally in Canada. A mutual business connection introduced him to Tempus 3D, a Canadian 3D printing Service Bureau specializing in manufacturing industrial plastics.
Challenge
Spark laser was needing approximately 40 internal parts for the lasers and needed to be able to iterate the design quickly and cost-effectively to come up with an optimal product ideally suited to their target market. These parts needed to be robust enough to withstand long-term use in an industrial environment, and they needed to be able to manufacture the parts or revise the design with minimal cost and lag time. Due to the relatively low volume of initial production, most traditional methods of manufacturing products were not viable options.
Solution
Spark Laser recognized very early on that the cost of producing molds for each of the parts and then changing the design and iterating with traditional manufacturing methods was not viable. The cost of having molds produced for each part would have ranged from as low as $5,000 per part up to $20,000 for some of the more complex parts, and this would have been multiplied by the number of iterations to the parts. Additionally, the complexity of design of some of the parts was not feasible for injection molding processes.
Spark Laser was an early adopter of 3D printing as a solution to the design challenges of building a complex product like a laser from the bottom up. They began using desktop 3D printers for quick in-house iteration, but when it came to producing the final product they needed parts that were comparable in quality, consistency, and aesthetics to injection molding. The parts produced by the desktop printer were not precise or robust enough for an end-use product. This is where Tempus 3D was able to really deliver value.
Spark Laser had Tempus produce its first set of parts in the summer of 2021, which were used to build the first functioning prototype laser. These parts were produced on Tempus 3D's in-house HP Multi Jet Fusion 5200 3D printer, which is capable of producing large volumes of high-quality parts with accuracy and aesthetics comparable to injection molding.
Result
Using industrial 3D printing allowed Spark laser was able to get their product to market quickly, and secure significant orders through a distribution partner. This has allowed Spark to test the market early without incurring massive research and design costs while keeping their inventory and raw materials costs near zero. They can essentially just order parts and raw materials on an as-needed basis and scale in a way that only 3D printing would allow.
Spark Laser and Tempus 3D continue to work together with the production of parts, and are both heavily invested in bringing manufacturing back to Canada. As Spark continues to see increasing demand for their products, Tempus is there to help them scale and meet their needs.
Featured Product
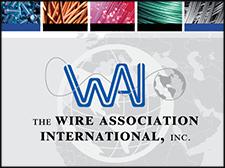
The Wire Association International (WAI), Inc.
The Wire Association International (WAI), Inc., founded in 1930, is a worldwide technical society for wire and cable industry professionals. Based in Madison, Connecticut, USA, WAI collects and shares technical, manufacturing, and general business information to the ferrous, nonferrous, electrical, fiber optic, and fastener segments of the wire and cable industry. WAI hosts trade expositions, technical conferences, and educational programs.