NEW AM POST PROCESSING TECHNOLOGY ARRIVES IN AM SOLUTIONS CUSTOMER EXPERIENCE CENTRE IN UK
The C1 now sits alongside an array of AM post-processing solutions in Knowsley, and customers are invited to come along and see them demonstrated and discuss which technology is best suited to their specific applications.
(31st October 2022, Knowsley, Merseyside, UK.) Leading AM post-processing solution innovator AM Solutions - 3D post processing technology UK is pleased to announce that it has just taken delivery of its C1 system, which will reside in the company's customer experience centre in Knowsley, UK. The C1 now sits alongside an array of AM post-processing solutions in Knowsley, and customers are invited to come along and see them demonstrated and discuss which technology is best suited to their specific applications.
Colin Spellacy, Head of Sales at AM Solutions - 3D post processing technology UK says, "Our customer experience centre plays to the fact that we are aware that companies in the AM sector more often than not need to assess the support technologies required when using AM as a production technology. It is unlikely that simply buying a post-processing technology off the shelf will produce optimal results, so we invite customers to come along, see what technology options we have for the finishing of both plastic and metal AM parts, and to discuss with our experienced team what solutions are best suited to particular products. The centre is equipped with our range of AM post processing solutions now including the C1 system, and we can offer advice to ensure the perfect treatment of your workpieces, and we carry out sample processing individually tailored to your specific requirements. This allows us to ultimately design the ideal process for you, which is a combination of the right machine system, the use of the right consumables, and the exact processing time needed for optimal outcomes."
AM Solutions - 3D post processing technology provides a range of automated post-processing technologies developed in order to overcome the sometimes, slow, costly, and disconnected AM process chain, and to ensure that AM is an efficient and viable production alternative to legacy manufacturing technologies. The company promotes innovative, customer-focused process development for AM operations, and collaborates with customers to ensure the optimal post-processing solution for each application.
The C1 system is an excellent tool for the automated and cost-efficient post processing of photopolymer components. It is equally effective on precision functional components, design objects with extremely fine structures, and complex prototypes.
Photopolymer-based AM processes are typically used when a higher level of detail or especially smooth surface finish is required, for intricate parts and components, and for mechanical attributes such as isotropy and water tightness. Support structures / resin are required to securely fix a part to the print bed and to prevent in-build warping, and these supports are usually very thin and only lightly touch the part being built. Supports can leave marks when removed, however, which means that specialist post-processing technologies are required.
Spellacy continues, "In the C1 system, the perfectly adapted compound and the interplay between mechanical and thermal effects results in a highly consistent, effective, and gentle removal of support structures / resin. The standard processing recipes, already stored in the PLC controller, can be individually modified and saved. In addition, our C1 machine contains various features to guarantee the optimal use of the compound and to minimize the operating costs. These include a fill level control system and an integrated saturation (contamination) sensor. Key process parameters such as temperature, cycle times and the degree of contamination of the compound are continuously recorded and saved with a data logger. This ensures full compliance with industry demands regarding quality control and consistency of the processing results. With the C1 system now in place in our customer experience centre we have a portfolio of post-processing technologies suitable for the full range of plastic and metal AM processes."
AM Solutions - 3D post processing technology is part of the Rösler Group which has been innovating surface finishing and post-processing technologies for over 80 years. Its range of AM post-processing technologies are focused on the removal of powder and support structures, surface smoothing, surface homogenisation, and polishing. The company also provides a wide range of consumables meaning that it is able to optimise the post processing of parts by customising the combination of machine and media to ideally suit specific applications. In this way AM Solutions' post-processing technologies promote outstanding quality, a high degree of result repeatability, and excellent cost efficiency.
www.solutions-for-am.com
About AM Solutions / Rösler Oberflächentechnik GmbH
For over 80 years, the privately owned Rösler Oberflächentechnik GmbH has been actively engaged in the field of surface preparation and surface finishing. As global market leader, we offer a comprehensive portfolio of equipment, consumables and services around the mass finishing and shot blasting technologies for a wide spectrum of different industries. Our range of about 15,000 consumables, developed in our Customer Experience Centers and laboratories located all over the world, specifically serves our customers for resolving their individual finishing needs. Under the brand name AM Solutions, we offer numerous equipment solutions and services in the area of additive manufacturing/3D printing. Last-but-not-least, as our central training center the Rösler Academy offers practical, hands-on seminars to the subjects mass finishing and shot blasting, lean management and additive manufacturing. Besides the German manufacturing locations in Untermerzbach/ Memmelsdorf and Bad Staffelstein/Hausen the Rösler group has a global network of 15 locations and 150 sales agents.
Featured Product
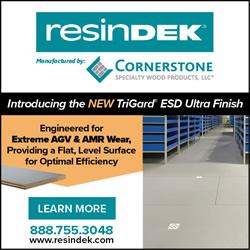