Introducing GE Additive’s Binder Jet Line and the Series 3
Industrialized additive technology delivers quality parts, at cost, at scale, safely
Cincinnati, OH, October 19, 2022 - GE Additive has today released more details of its Binder Jet Line and the Series 3 printer. With production deliveries expected to begin in the second half of 2023, the release of the system follows a four-year phase of customer discovery, collaboration and testing to ensure the system is ready and relevant for modern, high-volume, serial production environments.
"We remain focused on only bringing technology solutions to market when they are ready, and can help our customers demonstrate return on investment and total cost of ownership. That is certainly the case with our new Binder Jet Line and the Series 3, which is reliable, safe, and meets their needs today and tomorrow," he added.
Customer centric innovation
Over the past four years a select group of strategic customer partners have contributed to the development of the GE Additive Binder Jet technology platform. Core to this development and knowledge, sharing work remains a mutual commitment to formally identify, design and productionize specific applications at cost, quality, at needed scale, safely.
Quality
The Binder Jet Line Series 3 can additively manufacture complex, small and large parts both - repeatably and reliably, with outstanding material properties that exceed casting equivalents with achievable through-hole diameters and wall thicknesses less than 500 μm. GE's Binder Jet technology has regularly proven the ability to successfully print and sinter large parts which meet dimensional and feature resolution tolerances for production, with demonstrated capability in (but not limited to) parts up to 25 kg in stainless steel, and no known limitations on maximum wall thickness.
The Binder Jet Line also enables the user to:
• De-powder intricate parts without destroying fine features, enabled by GE's proprietary binder systems
• Sinter parts within the desired tolerances, enabled in part by GE Additive's Amp™ software's distortion prediction and compensation capability
• Develop casting equivalent or better, high-quality parts much faster than traditional methods
• Print and sinter parts with low surface roughness
Cost
As GE Additive strives to make industrial metal additive manufacturing an economical process, $/cc is a critical driver of the Binder Jet Line. The further the cost of a final part can be driven down, the more application space is available for the technology.
Part of those calculations include cost comparisons to conventional manufacturing technologies, in terms of tolerances and cost, from incoming raw material, to the final part in hand (total cost of ownership—not just the machine).
Other cost efficiency benefits include:
• Less spent on raw materials by recycling unused powder and leveraging less expensive material vs. other powder bed technologies
• Open space for new applications and innovation
• Utilization of the entire build box, top to bottom, edge to edge, with no need for supports
• Ability to introduce new innovative parts otherwise too costly or difficult to manufacture with conventional or other existing additive technologies
Scale
GE's Binder Jet Line offers high overall equipment effectiveness (OEE), automation readiness, predictive distortion and compensation, and material properties that meet and exceed industry standards. All of these come together with the goal of lowest total cost of ownership for metal additive production.
Based on input from customers and partners during the technology development phase, GE Additive is focused on enabling the eventual deployment of 40, 50, 100+ machine installations that will drive repeatable process quality, while minimizing operator contact with equipment and materials.
Other scale benefits include:
• Ability to print up to 100X faster than other additive manufacturing modalities
• Automation-ready technology that drives high productivity
• Process and hardware designed to optimize Takt times
• Seamless industrialization and integration into factory cells
Safety
The Binder Jet Line can be installed and operated without hazard zoning required and has been designed for minimal operator contact with the system and metal powders.
The system will be UL listed and CE certified, has a 100% inert and sealed environment, fully closed loop powder-free exposure and is designed for compatibility with reactive and flammable powder and binders.
Other safety benefits include:
• Zero operator powder exposure for powder load and operation
• Fully independent and real-time safety system on-board constantly monitoring machine conditions
• Real-time OPC UA data streaming for integration into factory MES and safety systems
Developed by additive users for additive users
"Fast-tracking solutions and bringing them to market too soon is not a sound strategy and is often the reason machines end up gathering dust in R&D labs. During the Series 3 and Binder Jet Line's development phase, we sought out customers who could give us honest, real-world insights from their high-volume manufacturing environments. We have taken their insights to complement our hands-on knowledge and experience of scaling additive production," said Brian Birkmeyer, product line leader for Binder Jet at GE Additive.
"The result is a modern, modular industrialized additive system - developed by additive users for additive users - that delivers quality parts, at cost, at scale and safely," he added.
Featured Product
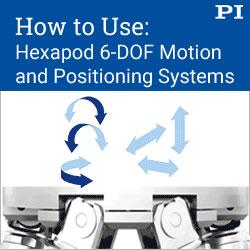
PI USA - Do you know Hexapods?
With six degrees of freedom and extremely versatile motion and positioning capabilities, hexapods find applications in Aero-Space, Automation/Assembly, Life Sciences, Microscopy, Optics, Photonics. How can a hexapod help your application?