Sandvik and BEAMIT join forces at Formnext 2022 – presenting their latest advancements in the industrialization of additive manufacturing
Sandvik and BEAMIT Group are once again co-exhibiting at the world-leading additive manufacturing (AM) event, Formnext 2022. The Sandvik-BEAMIT booth D21 in hall 11 will demonstrate the very latest from the companies’ offering along the additive value chain, including new materials within Sandvik’s market-leading Osprey® metal powder range – and several additive customer cases from both companies.
Sandvik and part-subsidiary BEAMIT Group - a world-leading AM service provider including 3T Additive Manufacturing - will visit Frankfurt, Germany, to showcase their expertise along the additive value chain. This year, materials authority Sandvik will present the latest news from their wide range of Osprey® metal powders, tailored to various AM process technologies, alongside a variety of industrial customer cases that highlight the joint offering of Sandvik and BEAMIT Group.
Kristian Egeberg, President of Sandvik Additive Manufacturing, says:
"We are delighted to meet our customers and partners at Formnext again this year, and to display and discuss how we can further develop our on-going business relationships - and build new ones. We have strong expertise within AM materials, powders, and processes, and our team of experts are keen to provide their support. Together, we want to drive the shift toward more sustainable manufacturing."
Andrea Scanavini, Chief Commercial Officer at BEAMIT, agrees:
"At BEAMIT, we are very much looking forward to visiting Formnext alongside Sandvik again. We thoroughly enjoyed our participation last year, and expect this years' event to be every bit as fruitful. The Sandvik-BEAMIT joint offering is a force to be reckoned with and we can't wait to demonstrate it in full to our customers and the additive market."
The widest range of Osprey® metal powders: including copper and cobalt-free maraging steel
With more than 160 years of materials expertise and 45 years' experience in powder atomization, Sandvik is a leading provider of gas-atomized metal powders for additive manufacturing, with the widest alloy range on the market. New at Formnext 2022 from the
ever-evolving range of Osprey® metal powders, is copper. Manufactured in-house, both pure and in a variety of alloyed variants, the material allows for greater control over factors such as thermal and electrical performance, size, shape, and weight of end components. The Osprey® copper powder comes in fine as well as medium-sized particle sizes. It's optimized for high thermal and electrical conductivity, which results in better heat transfer and coefficient of thermal expansion (CTE) matching.
Also featured in booth D21 is Sandvik's well-renowned maraging steels, now also available cobalt-free - allowing for substantial benefits in sustainability as well as in shipping.
Luke Harris, Sales Director at Sandvik Additive Manufacturing, comments:
"Sandvik is a materials technology company by heritage and being able to continuously evolve our offering to make our materials even more sustainable, while benefitting our customers, is just fantastic. As part of our everyday operations, we tailor materials to meet customer-specific needs - and develop new alloys to cover up for deficiencies on the market."
Maraging steel is typically used in high-cycle environments such as tooling - where the materials need to withstand wear and tear, as well as extreme temperature changes.
Luke Harris continues:
"Cobalt-free maraging steel is excellent combined with additive manufacturing. The AM process inherently decreases cycle times which, with a material that offers high strength without losing ductility, will greatly benefit our customers."
Additively manufactured super-duplex stainless steel
In 2021, Sandvik and BEAMIT announced themselves uniquely positioned in terms of producing additively manufactured components in super-duplex stainless steel, offering optimized performance for the most demanding marine environments while enabling minimal downtime and no capital tied up in parts. Outperforming several traditionally manufactured counterparts, Sandvik's super-duplex components are 3D printed in the company's flagship material Osprey® 2507 - a strong, corrosion-resistant super-duplex metal powder, tailored for AM and manufactured in-house to the highest international standards.
On display at Formnext 2022 will be not only the "impeller reinvented", that Sandvik printed in Osprey® 2507 alongside energy giant Equinor and Norwegian Eureka Pumps, but also a larger size impeller created in collaboration with BEAMIT Group.
Daniel France, Business Development Director at BEAMIT, says:
"The super-duplex impeller was a great project to realize with our partners at Sandvik Additive Manufacturing. We set out to develop process parameters on new platforms, to meet the demand for bigger applications. The new impeller measures 380 mm in diameter - and to our customers in the offshore- and energy sectors the ability to combine larger sizes with the outstanding strength and corrosion resistance attained through additively manufactured Osprey® 2507, is a massive step forward."
Osprey® titanium- optimized for additive manufacturing
Sandvik will also display their Osprey® titanium powder which, being both durable and light, is a material frequently used across a variety of industries such as aerospace and medical. Sandvik's titanium powders are manufactured in highly automated, state-of-the-art facilities, with quality management systems certified to, for instance, AS9100-D and ISO 13485:2016. Managing the full process chain in-house, from raw material through to metal powder and finished component, allows for Sandvik to offer unique levels of traceability - which is key in many of the most demanding industries. Processing the Osprey® titanium in their own additive manufacturing workshop, Sandvik will be displaying skull implants, acetabular cups, and suppressors in titanium at Formnext 2022.
3D printed cemented carbides by Sandvik
Apart from metal powders, Sandvik will also showcase one of the newer additions to their additive offering: 3D-printed cemented carbides. Stating "freedom of design has never been harder", the materials giant has been working with cemented carbide since 1932. Today, Sandvik is a world leader in hard materials, providing for instance metal cutting- and mining tools such as turning inserts, end-mills, and drill bits - and are now also able to additively manufacture one of their very most long-standing flagship materials into virtually any shape, through a unique and patented process.
Anders Ohlsson, Product Manager at Sandvik Additive Manufacturing, says:
"The most critical factor in our process is working with powders that have the just-right properties. We have developed both a cemented carbide powder and a proprietary process that are truly unique. Our powders are optimized to print components that look great, work well, and are fit for use in actual applications, demanding environments, and serial production."
Additively manufactured cemented carbide is a potential gamechanger across several industries - since wear is a common challenge in basically any segment.
Anders Ohlsson continues:
"By shifting to 3D-printed cemented carbide, you're not only enjoying the benefits of design freedom, but also the impact of increasing the lifetime of your components by up to 20 times, compared to those manufactured with any other steel or alloy."
A selection of cemented carbide impellers, wire-drawing nibs, and nozzles - developed in cooperation with Varel - will be on display in Frankfurt.
The Sandvik-BEAMIT booth D21 will be filled with industrial customer cases covering a wide range of materials and additive processes, as well as the leading metal powder and AM experts of Sandvik and the BEAMIT Group - ready to discuss customers' specific needs and challenges. For further information about Sandvik's presence at Formnext 2022, please visit our Formnext website.
ABOUT SANDVIK ADDITIVE MANUFACTURING
Sandvik Additive Manufacturing has a world-leading position in metal powder with the widest range of AM-alloys on the market. The company has also made sizeable investments into a wide range of AM printing technologies since 2013. Adding 160 years of leading expertise in materials technology, 75 years in post processing methods like metal cutting, sintering and heat treatment, Sandvik has well established and leading competence across the entire AM- value chain. In 2019, Sandvik acquired a significant stake in BEAMIT, a leading European- based AM service provider, and after this, the BEAMIT Group has acquired 100% of ZARE and 3T Additive Manufacturing, bringing together three leading AM service bureaus in Europe - to create one of the largest independent AM service providers in the world, serving the most demanding industries.
Sandvik AB is a global, high-tech engineering group with approximately 39,000 employees and sales of approximately 86 billion SEK in about 150 countries (2021). The company was founded in Sweden in 1862 and is listed on the Stockholm stock exchange since 1901.
ABOUT BEAMIT GROUP
BEAMIT Group is one of the most advanced Additive Manufacturing (AM) service providers in the world and serves the most demanding industries, like aerospace, automotive, medical, energy, racing and industrial engineering. It has recently become the first One-Stop Shop in metal AM, offering globally a fully integrated value chain. In 2019, Sandvik acquired a significant stake in BEAMIT. With 24 years' experience in AM with metal powders BEAMIT is an approved supplier for serial production by many leading OEMs, and holds a significant number of quality certifications, including AS/EN 9100:2018 for aerospace, IATF automotive, NADCAP accreditation for heat treatment processes and laboratories, and NADCAP accreditation for welding - additive manufacturing commodity.
BEAMIT Group consists of the original BEAMIT organization, ZARE (acquired in 2020) and 3T Additive Manufacturing (acquired in 2021) as well as a participation in PRES-X, specialized in high-end post processing for 3D printing. BEAMIT Group HQ are in Fornovo di Taro (Parma, Italy). Today the company counts around 130 employees and close to 60 dedicated AM systems distributed across 7 facilities in Italy and the UK.
Featured Product
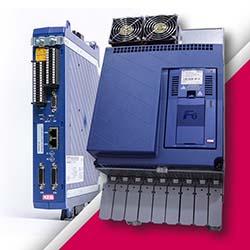