Hypertherm Associates heads to FABTECH 2022 with all new Hypertherm plasma, OMAX waterjet, and software products
The company’s Hypertherm and OMAX technology brands will welcome show visitors from two halls at Atlanta’s Georgia World Congress Center on November 8, 9, and 10.
HANOVER, N.H.—Aug. 2, 2022—Hypertherm Associates, a U.S. based manufacturer of industrial cutting products and software, is preparing for FABTECH 2022, North America's largest fabricating, welding, and finishing exhibition. The company's Hypertherm and OMAX technology brands will welcome show visitors from two halls at Atlanta's Georgia World Congress Center on November 8, 9, and 10.
The Hypertherm and OMAX technology brands will exhibit from one combined booth to offer show visitors a comprehensive array of plasma and waterjet products. Visitors to Booth B8309 will have an opportunity to see the world's only X-Definition plasma and a new HPR cartridge for HPRXD plasma systems. In addition, they can see the OptiMAX, considered the world's most accurate waterjet, along with the ProtoMAX, a compact, self-contained cutting system perfect for prototyping and low volume cutting. Hypertherm Associates will also feature its ProNest CAD/CAM nesting software, providing show visitors with live demonstrations of its recently released ProNest 2023.
Powermax air plasma products, including the innovative Powermax SYNC plasma with built-in intelligence and a single-piece consumable cartridge, will be available in Booth B11237. Attendees will have the opportunity to try the Powermax SYNC and its SmartSYNC torch. They can also meet Metal Artist, TV Personality, and Author Rae Ripple who plans to unveil her newest creation, an intricately cut vintage car hood that she made with her Powermax65 SYNC.
Finally, Hypertherm Associates will exhibit its Robotmaster offline programming software for robots from Booth C10827. The Robotmaster team will demonstrate new software that bridges the gap between CAD/CAM and robotics by enabling seamless integration between a user's chosen CAD/CAM software and Robotmaster.
"We are excited to return to Atlanta for FABTECH 2022," said Kristy Gerwig who is managing this year's show for Hypertherm Associates. "We can't wait to see our partners and loyal customers in person and meet new customers to discuss how our plasma, waterjet, and software products can support their business goals."
Hypertherm Associates is a U.S. based manufacturer of industrial cutting products and software. Its products, including Hypertherm plasma and OMAX waterjet systems, are used by companies around the world to build ships, airplanes, and railcars; construct steel buildings, fabricate heavy equipment, erect wind turbines, and more. In addition to cutting systems, the company creates CNCs and software trusted for performance and reliability that result in increased productivity and profitability for hundreds of thousands of businesses. Founded in 1968, Hypertherm Associates is a 100 percent Associate-owned company, employing approximately 2,000 Associates, with operations and partner representation worldwide. Learn more at www.HyperthermAssociates.com.
Featured Product
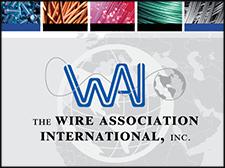
The Wire Association International (WAI), Inc.
The Wire Association International (WAI), Inc., founded in 1930, is a worldwide technical society for wire and cable industry professionals. Based in Madison, Connecticut, USA, WAI collects and shares technical, manufacturing, and general business information to the ferrous, nonferrous, electrical, fiber optic, and fastener segments of the wire and cable industry. WAI hosts trade expositions, technical conferences, and educational programs.