Greene Tweed Highlights Custom Life Sciences Sealing Solutions
Custom-engineered seals for pharmaceutical processing maintain inert nature in demanding conditions
Kulpsville, PA - Greene Tweed, a leading global manufacturer of high-performance seals, thermoplastics, composites, and engineered components, highlights its sealing solutions for pharmaceutical processing.
Greene Tweed closely collaborates with customers to design, prototype, and test sealing solutions for life sciences applications in the pharmaceutical manufacturing, analytical instrumentation, and hygienic fluid handling sectors. Greene Tweed's expanded portfolio of sealing solutions meet the stringent cleanliness, traceability, FDA, and regulatory compliance needs of the pharmaceutical processing industry.
Greene Tweed custom-engineers solutions with its chemical-resistant Chemraz® FFKM, Fusion™ FKM, Fluoraz® FEPM, and other materials to meet or exceed quality requirements, including United States Pharmacopeia (USP), FDA, and ISO product standards. With low leachable profiles, these specialty compounds maintain their inert nature in highly demanding conditions.
Greene Tweed products include custom-engineered seals, gaskets, and o-rings. For pharmaceutical, biotechnology, and aseptic processing, Greene Tweed sanitary gaskets enable fast and reliable connection of flanged tubes that periodically open. Their non-sticky elastomer formulation enables quick and easily gasket installation.
Greene Tweed Metal Spring Energized (MSE®) seals create a leak-free seal without excessive friction and wear by applying calculated spring force directly over sealing lips. MSE® seals operate from cryogenic to 625°F (329°C) and available in custom sizes.
To learn more about Greene Tweed custom life sciences solutions, visit www.gtweed.com/capabilities.
Featured Product
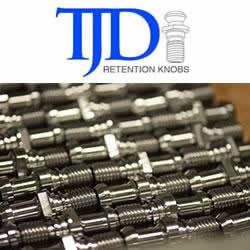
T.J. Davies' Retention Knobs
Our retention knobs are manufactured above international standards or to machine builder specifications. Retention knobs are manufactured utilizing AMS-6274/AISI-8620 alloy steel drawn in the United States. Threads are single-pointed on our lathes while manufacturing all other retention knob features to ensure high concentricity. Our process ensures that our threads are balanced (lead in/lead out at 180 degrees.) Each retention knob is carburized (hardened) to 58-62HRC, and case depth is .020-.030. Core hardness 40HRC. Each retention knob is coated utilizing a hot black oxide coating to military specifications. Our retention knobs are 100% covered in black oxide to prevent rust. All retention knob surfaces (not just mating surfaces) have a precision finish of 32 RMA micro or better: ISO grade 6N. Each retention knob is magnetic particle tested and tested at 2.5 times the pulling force of the drawbar. Certifications are maintained for each step in the manufacturing process for traceability.