Smart3D launches Macro - a production 3D printing platform
A suite of 3D printers conceived to seamlessly transition from product development to manufacturing.
[September 21, 2020] Industry Supplies today announced the launch of the new Smart3D Macro platform. The Smart3D Macro offers the broadest material capabilities, a large build volume and a print speed that makes it a real manufacturing engine.
With its up-to-120°C actively heated 350 x 350 x 400mm chamber, Macro is more than a printer of high-performance materials. It is a solution to print any material at its highest performance. The Smart3D team has gone a long way to ensure material properties are optimized, regardless if it's ABS, nylon, PEEK or composites. From a professional drying solution that restores the material's optimal moisture level without being damaged by high heat or hydrolysis, to a system capable of printing the materials close to their glass transition temperatures, to an open material platform that enables a vast and constantly growing range of applications.
In the same way its hardware was designed with a scalable and modular approach, Smart3D offers software modules that serve diverse user needs. Businesses and educational institutions may benefit from the Smart3D Cloud, or install the Smart3D LAN printer management software locally if it better suits their IT requirements. To securely interconnect devices in production plants, the company has developed an IoT solution that works as a serverless neural network where communications take place without the need of a central server. This provides a new level of redundancy, as there is no danger of attack at one node that may compromise the rest of the network. Last but not least, the Factory Management module offers multiple packages to integrate Smart3D systems with the company's ERP, enabling management of the factory's full workflow.
Smart3D Macro is shipping. Interested customers may turn to their local resellers or contact Industry Supplies for further information and availability.
About Industry Supplies
Industry Supplies have created the Smart3D range to answer the demands of the rapidly growing industrial 3D printing industry. They have previously released the Smart3D Multimaterial Dryer, a filament drying solution capable to simultaneously drying a wide range of materials in less than 3 hours. Committed to Industry 4.0 guidelines and to high security and redundancy for use in industrial environments, the Smart3D range provides an opportunity to develop ¬-manufacturing with new technologies and materials. Visit smart3d.tech for more information.
Featured Product
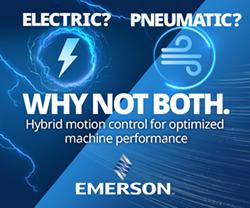
Elevate your manufacturing processes with data-driven insights
Join Emerson at Hannover Messe 2025, Hall 11, Booth C30 and discover how embracing a Floor to Cloud™ strategy can revolutionize your operations. This strategy integrates on-site devices and technologies with cloud analytics, providing the insights needed to enhance manufacturing efficiency, maximize workforce potential, and achieve sustainability targets. Our team of experts have a commitment to innovation and look forward to discussing your challenges to develop a customized solution. Claim your Free Ticket.