ExOne Metal Binder Jetting Now Offered Through Xometry
Binder jetting offers Xometry customers a fast and cost-effective way to 3D print metal prototypes and production parts. With binder jetting, an inkjet printhead quickly deposits a bonding agent onto a thin layer of powdered particles -- either metal, sand, ceramics or composites. This process is repeated, layer-by-layer, using a map from a digital design file, until the object is complete.
The ExOne Company (Nasdaq: XONE), the global leader in industrial sand and metal 3D printers using binder jetting technology, and Xometry, the largest U.S. marketplace for custom manufacturing, today announced that they will partner to provide metal 3D printing services.
Binder jetting offers Xometry customers a fast and cost-effective way to 3D print metal prototypes and production parts. With binder jetting, an inkjet printhead quickly deposits a bonding agent onto a thin layer of powdered particles -- either metal, sand, ceramics or composites. This process is repeated, layer-by-layer, using a map from a digital design file, until the object is complete.
ExOne will be the exclusive provider of binder jetting services in Xometry's recently-launched Digital RFQ Marketplace. ExOne currently 3D prints more than 20 materials, including 316L and 17-4PH stainless steels, Inconel 718 and M2 Tool Steel.
"ExOne is proud to offer our metal 3D printing services to Xometry customers," said John Hartner, ExOne's CEO. "Our industrial binder jet machines can truly take products from prototyping all the way to final production with a single process that is fast, affordable and sustainable."
"We're excited to offer binder jetting to expand the range of services our customers can get from Xometry's new Digital RFQ Marketplace," said Randy Altschuler, Xometry's CEO. "ExOne is a true innovator in additive manufacturing and we believe this partnership is a big win for our customers."
Customers can secure a quote through Xometry for ExOne metal binder jetting services at https://www.xometry.com/manufacturing/exone.
About ExOne
ExOne is the pioneer and global leader in binder jet 3D printing technology. Since 1995, we've been on a mission to deliver powerful 3D printers that solve the toughest problems and enable world-changing innovations. Our 3D printing systems quickly transform powder materials — including metals, ceramics, composites and sand — into precision parts, metalcasting molds and cores, and innovative tooling solutions. Industrial customers use our technology to save time and money, reduce waste, improve their manufacturing flexibility, and deliver designs and products that were once impossible. As home to the world's leading team of binder jetting experts, ExOne also provides specialized 3D printing services, including on-demand production of mission-critical parts, as well as engineering and design consulting. Learn more about ExOne at www.exone.com or on Twitter at @ExOneCo. We invite you to join with us to #MakeMetalGreen™.
About Xometry
Xometry is the largest marketplace for custom manufacturing, connecting customers with optimal manufacturing solutions through proprietary AI algorithms. Xometry provides on-demand manufacturing and industrial supply materials to a diverse customer base, ranging from startups to Fortune 100 companies. Our nationwide network of thousands of partner manufacturing facilities enables us to maintain consistently fast lead times while offering a broad array of capabilities, including CNC machining, 3D printing, sheet metal fabrication, injection molding, and urethane casting. Xometry's customers include BMW, Dell Technologies, General Electric, Bosch, and NASA. Learn more about Xometry at www.xometry.com or on Twitter at @xometry.
Featured Product
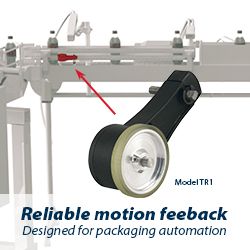