The Experience Economy in the Context of Design to Production Process Chains
Today's consumers expect to feel personally and emotionally addressed by products and services, and digitalization can confirm that expectation. Werner Busenius, VP Global Sales at Digital Manufacturing Solutions, outlines the challenges that the so-called experience economy holds for manufacturing.
The term experience economy sounds very modern, but it actually dates back to the late 1990s. In a 1998 article for the Harvard Business Review, authors Joseph Pine II and James Gilmore suggested that product features per se are less and less decisive for consumers and customers, and that as a consequence they are not necessarily prepared to pay higher prices for supposed differences in product characteristics.
Sentimental rather than rational choices: Experience as a motivator for purchasing decisions
Instead, say the authors, the chief distinguishing aspect is whether a customer associates positive personal experiences with a product, a service, or a combination of the two.
In principle, this means that product perceptions, previously related merely to specific but dispassionate services, are changing in favor of true emotion. Thus, people will only become satisfied, loyal customers if one can truly touch their hearts and minds.
Numerous companies have successfully followed this idea. One renowned example is Starbucks. The company's founder, Howard Schultz, wanted to offer customers an overall experience, staging the numerous coffee variations against elegantly designed interiors and just the right background music. Anybody can brew a cup of coffee. Starbucks, however, gets to its customers at an emotional level.
The Experience Economy in the 5G Era
For business, the task of addressing this phenomenon is just as relevant today as it was 20 years ago. But now, digitalization offers an entirely new range of ways in which companies can capture and shape the perceptions of their clients. In the days of platform economics, managing customer experience is a business-critical IT topic - just consider the way SAP has positioned itself.
But what are the effects of this trend on the product engineering and production process? Emotion is rarely triggered by uniformity and immobility. For successful, widely effective brand loyalty, a company needs a broad variety of constantly changing products that customers can configure according to their own ideas, needs and requirements.
Dimensions, materials, functions: How to keep variant management under control?
This development thus leads to ever-increasing product variance and ever shorter product cycles. Markets become dominated by innovation and novelty. This applies especially to consumer goods like computers, mobile phones or cars. In some parts of the TV segment, barely six months go by before a new generation arrives on the market. For computers, only three to four months elapse between models.
To be able to address this complexity in a financially viable way, production plants in the discrete manufacturing industry must be designed for maximum flexibility: Growing product variety leads to smaller lot volumes, unless one wants to break the fundamental rules of lean manufacturing, with its smoothly synchronized material flows and low inventories, and risk major detriments to competitiveness.
To satisfy these requirements, companies are deploying an ever-increasing number of robots in production. Individual programming makes them flexible enough to cope with a variety of components and perform a multitude of handling tasks - without ever growing tired or delivering erratic quality.
The task for management: Taking a comprehensive view of processes
Obviously, production planning times for the robot cells (including programming) must be kept as short as possible in order to avoid unnecessary delays when switching from one component to another, because such delays which would cause a loss of valuable production capacity.
Generally, robots should be programmed offline - well-established solutions are available for this purpose. Today, manual on-the-ground robot teaching should only be done where it cannot be avoided.
But targeting the issue of robot programming cannot be the first step, because production preparation and planning also includes activities that have to be contributed by other company divisions first.
The main aspect here is engineering, which first has to construct and design the component with reference to the respective technical requirements and producibility criteria.
Regarding the efficiency and speed of the overall process (we refer to this as "design-to-production"), the key question is: In what form does engineering provide the production planning information required for programming purposes?
If engineering only provides 3D geometry without supporting manufacturing information, the programmers must either devote a great deal of effort to generating these essential data on their own, or the component must be taught online via programming software. Software teaching may be more efficient than on-the-ground teaching at the physical facility, but it is likewise slow and error-prone.
One major difficulty is that the production planning time one must devote to setting up a robot cell often exceeds the production time which the component actually spends within the facility (see also our use-case on special-purpose vehicle engineering).
Design-to-Production: Optimizing the overall process for a substantial ROI boost
What can we conclude from these observations? One cannot attain a sustainably successful "digital transformation" by only making selective improvements and optimizing individual process steps. The goal must be to examine the overall process chain and find a suitable approach that addresses the entire production sequence.
The investments involved in this effort are well worthwhile. To assess cost effectiveness, one simply has to calculate how much additional turnover and profit a company can generate per unit of time by achieving x percent of additional productivity, and then compare that value to the total costs incurred over the same unit of time.
If you examine this question for your own enterprise, you may well encounter impressive business cases with enormous return-on-investment dimensions.
CENIT is ideally positioned to provide sound support to companies in their digital transformation. Our overall competence includes not only the necessary IT expertise, but above all the experience in the various production processes and technologies, which is essential for the design of a successful end-to-end solution.
This lets us support our clients right from the start, providing consulting and implementation services based on their specific IT environment - no matter whether they ultimately choose a greenfield approach that reinvents the wheel, or a conservative brownfield approach that aims to transfer as much of the legacy system into the new solution as possible.
The bottom line: Well-equipped for the Experience Economy and better operative results
The experience economy began trending many years before the first smartphone was introduced. In those days, the Internet played a far lesser role in the lives of most consumers, and the digitalization wave that is towering ever higher today could hardly have been imagined.
For this reason, one may assume that the phenomenon will - independently of the digital transformation and the social and technological developments it triggers - stay with us in the years to come.
With a view to discrete manufacturing, one may say that a sustainably successful digital transformation of the pre-manufacturing design-to-production process chain is the ideal way to address the experience economy and may intensify and accelerate its development.
Businesses which exploit the opportunities of digital transformation with the right approach (and partner) not only serve their core markets better and achieve higher customer satisfaction - they also benefit from an excellent business case.
Read this article about the Experience Economy in the context of the "design-to-production" process chain also in the CENIT Newsroom (www.cenit.com).
Featured Product
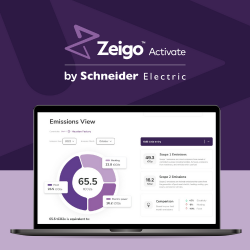
Zeigo Activate by Schneider Electric: Energy efficiency software for manufacturing facilities.
Whether you're responding to new legislation and regulations or getting pressure from stakeholders and customers, Zeigo Activate empowers companies to effectively calculate, track, and reduce their carbon footprint and become more energy efficient. By providing valuable insights, actionable data, and intuitive tools, Zeigo Activate is tailored for businesses at any stage in their energy efficiency journey. Our easy-to-use software allows you to set your emissions baseline and target, receive a customizable project roadmap, and connect to a network of regional solution providers in energy efficiency and renewable energy so that you can put your ambitions into action.