Essentium Introduces New Materials for High Temperature Industrial Applications at Rapid + TCT 2020
High-performance materials meet the rigors of the factory floor to drive industrial-scale Additive Manufacturing
AUSTIN, Texas, February 20, 2020 - Essentium, Inc., a leading provider of 3D printing technology for Additive Manufacturing, will introduce new ULTEM™ AM9085F and ABS materials which will be showcased on its award-winning Essentium High Speed Extrusion (HSETM) 3D Printing Platform at Rapid + TCT 2020. The high-performance materials offer superb properties at high temperatures making them an ideal choice for many aerospace, automotive, and medical applications. By delivering a complete and no compromise solution, the Essentium HSE combined with innovative materials finally unlocks the promise of industrial applications of Additive Manufacturing.
Findings from independent global research on the current and future use of industrial 3D printing showed that 50% of companies said they need high quality and affordable materials to meet the growing demand for industrial 3D printed parts. However, the survey commissioned by Essentium revealed that 51% of executives view the high cost of materials as a key obstacle to adopting 3D printing for large-scale production.
Essentium developed the new ULTEM™ AM9085F and ABS materials to address this issue and offer manufacturers a cost-effective alternative to closed-system materials which are prohibitively expensive to buy and maintain. Essentium's high-performance materials offer excellent resistance to heat and chemicals, while providing high strength making them ideal for industrial applications such as machine parts, tools, jigs and fixtures.
About Essentium
Essentium, Inc. provides industrial 3D printing solutions that are disrupting traditional manufacturing processes by bringing product strength and production speed together, at scale, with a no-compromise engineering material set. Essentium manufactures and delivers innovative industrial 3D printers and materials enabling the world's top manufacturers to bridge the gap between 3D printing and machining and embrace the future of additive manufacturing.
Featured Product
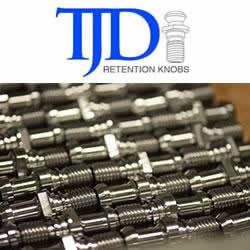