Semiconductor Manufacturing: Achieving Water Authority Compliance with Automated Wastewater Treatment
Automated wastewater treatment systems help semiconductor manufacturers remain in compliance with EPA and local standards, while significantly reducing the cost of treatment, labor and disposal
Over 200 organic and inorganic chemicals and large amounts of water are used by manufacturers to produce semiconductor chips. As a result, wastewater from semiconductor manufacture usually contains a broad range of contaminants including acids, alkalis, a variety of metals including copper, lead, arsenic, and antimony, ammonium, fine oxide particles, salts, solvents and other organic and inorganic compounds.
Nevertheless, semiconductor manufacturing facilities must meet local, state and EPA wastewater requirements for effluent discharge, including those under the Clean Water Act. Failing to do so can result in severe fines that quickly escalate.
Under the Clean Water Act, the US EPA has identified 65 elements and groups of compounds as "Toxic Pollutants", EPA has expanded this list to include 126 specific substances which have been designated "Priority Pollutants".
In order to meet discharge limitations for these priority pollutants semiconductor manufacturing facilities must either have their waste water hauled to a liquid hazardous waste disposal site, which is extremely costly, or have a wastewater treatment system that effectively separates the contaminants from the water so it can be legally discharged into sewer systems or even re-used.
Traditional wastewater treatment systems can be complex, however, often requiring multiple steps, a variety of chemicals and a considerable amount of labor. Too often, technicians must still monitor the equipment in person, even when the process is supposedly automated. This usually requires oversight of mixing and separation, adding of chemicals, and other tasks required to keep the process moving. Even then, the water produced can still fail to meet mandated discharge limits because the processes rely on polymer or inorganic chemical flocculants and coagulants. These separating agents produce very fragile chemical flocs that can release pollutants when put under pressure during dewatering. Chemical flocs also tend not to retain pollutants during EPA mandated TCLP (Toxic Characteristic Leaching Procedure) testing so the resulting sludge cannot be disposed of inexpensively as non-hazardous waste in a municipal landfill.
In contrast, it is much more cost effective to treat the industrial wastewater at its source, so treated effluent can go into a sewer and treated sludge passes a TCLP test and can be disposed of as non-hazardous waste in a local landfill.
Fortunately, complying with EPA and local wastewater regulation has become much easier with more fully automated wastewater treatment systems. Such systems not only reliably meet regulatory wastewater requirements, but also significantly reduce the cost of treatment, labor and disposal when the proper separating agents are also used.
Cost-Effective, Automated Wastewater Treatment
In contrast to labor-intensive multiple step processes, automated wastewater treatment can help to streamline production, usually with a one-step process, while lowering costs at semiconductor manufacturing facilities.
An automated wastewater treatment system can eliminate the need to monitor equipment in person while complying with EPA and locally mandated requirements. Such automated systems separate suspended solids, heavy metals, emulsified oil and encapsulate the contaminants, producing an easily de-waterable sludge in minutes. The water is typically then separated using a de-watering table or bag filters before it is discharged into sewer systems or further filtered for re-use as process water. Other options for de-watering include using a filter press or rotary drum vacuum. When dried, the resulting solids will pass the TCLP leaching test and are considered non-hazardous so they can be disposed of in a municipal landfill.
The treatment systems are available in batch, semi-automatic, or fully automatic form and can be designed to be part of a closed loop system for water reuse or to provide legally dischargeable effluent suitable for disposal in municipal a sewer system. A new, fully customized system is not always required. In many cases, it can be faster and more cost effective to add to or modify a facility's current wastewater treatment systems when this is feasible.
Because every wastewater stream is unique to its industry and application, each wastewater treatment solution must be specifically tailored to the application. The first step in evaluating the potential cost savings and effectiveness of a new system is to sample the wastewater to determine its chemical make-up. This is followed by a thorough review of applicable water authority requirements. The volume of wastewater that will be treated is also analyzed, to determine if a batch unit or flow-through system is required. Other considerations include size restrictions to ensure that the system fits within the facility's available footprint.
Separating Agents
Critical to the success of any automated wastewater treatment system is the use of an effective and efficient separating agent that can attract and bind dissolved contaminants and encapsulate suspended contaminants to allow rapid separation from the treated water.
Sabo Industrial Corp., a New York-based manufacturer of waste water treatment equipment, uses CLEARTREAT® bentonite-based separating agents manufactured by Wyo-Ben, Inc. These separating agents are formulated to break oil and water emulsions, electrochemically adsorb and sequester dissolved metals and other positively charged contaminates, create metal hydroxide precipitates and yield easily dewatered clay flocs that encapsulate suspended solids for rapid removal.
Bentonite has a large specific surface area with a net negative charge that makes it a particularly effective adsorbent and ion exchange medium for wastewater treatment applications to remove dissolved metals and other charged chemicals. Bentonite also creates durable flocs that effectively encapsulate suspended materials. This can usually be achieved in one-step treatment, which lowers process and disposal costs.
In contrast, polymer-based products create very weak flocs that allow encapsulated waste materials to easily leach back out over time or upon further agitation.
Today's automated systems along with highly effective CLEARTREAT separating agents can provide semiconductor manufacturers with an simple, cost-effective alternative for treating their waste water so they can compliant with local, state and federal regulations. Although there is a cost to these systems, they do not require much attention and can easily be more economical than paying fines or hauling.
For more information, call 845-562-5751; Fax: 845-562-5909; email: info@saboindustrial.com; visit http://saboindustrial.com; or write to Sabo Industrial at 2 Little Britain Road Newburgh, NY 12550.
Featured Product
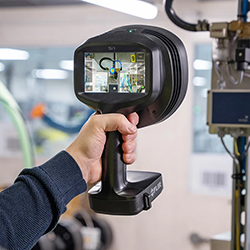