3D Systems Advancing High Performance Automotive Sector with Leading Industry-specific Workflow Solutions
- Rodin Cars, manufacturer of high performance open-wheel track cars, turns to 3D Systems to deliver increased speed and design advantages - Stewart-Haas Racing, winner of 12 Monster Energy Cup Series races in 2018, relies on 3D Systems' solutions to help them rapidly design, test, and perfect auto body parts to increase speed and improve performance
3D Systems (NYSE: DDD) today announces two customers - Rodin Cars and Stewart-Haas Racing - that are using the company's plastic and metal 3D printing solutions to dramatically improve speed and performance in their cars. With the help of 3D Systems, Rodin Cars and Stewart-Haas Racing, two industry leaders, can rapidly create durable parts -- including design and prototyping with faster iteration, and production. This approach enables quicker time to implementation, and lower total cost of operation. The integration of 3D Systems' additive manufacturing solutions into these automotive production workflows is one more example of how the company is expanding applications, use case by use case.
Accelerating Automotive Design and Production
Rodin Cars (North Canterbury, New Zealand) uses 3D Systems' direct metal printing (DMP), selective laser sintering (SLS) and stereolithography (SLA) technologies to design, develop and build the world's very best, maximum-performance open-wheel cars for racetracks.
"The extreme conditions of track racing leave no room for error," said David Dicker, founder, Rodin Cars. "Many components that we manufacture in-house have geometrical complexities that only 3D printing can provide. What we're able to accomplish through the breadth of solutions offered by 3D Systems' printers is second to none, providing build-speed and design advantages that are hard to match."
The high performance track-car manufacturer uses the sPro 230 for SLS production parts, the ProX® 800 for SLA tooling for carbon fiber forms with 3D Systems' Accura® Bluestone material, and the ProX DMP 320 with 3DXpert™ for titanium production parts of exhaust collectors and mufflers, uprights and hubs, as well as a wide range of component mount brackets. As a result, Rodin Cars is able to quickly manufacture full-size prototypes as well as production components without the need for tooling. It is also able to advance complex design concepts, and produce lighter weight metal parts not manufacturable in any other way.
Stewart-Haas Racing (Kannapolis, North Carolina) uses powerful 3D scanning with 3D Systems' Geomagic Wrap® reverse engineering software and the ProX 800 printer to produce aerodynamic components for race car component development and wind tunnel testing. For a NASCAR team, perfecting automotive components designed to increase speed and performance is a vital ingredient for success. Geomagic Wrap is used to collect scan data from the car components, process it, and create .stl files for shape deviation comparison. 3D Systems' 3D Sprint® software is used to prepare and optimize the CAD data and manage the additive manufacturing process on the ProX 800. Using 3D Systems' Accura 25 material, Stewart-Haas Racing's engineers are able to rapidly print large parts with a smooth surface finish and precise dimensional accuracy.
"Everything we do is related to putting more speed into our cars," said Reneau Van Landingham, aerodynamic design group manager, Stewart-Haas Racing. "Our most valuable asset is time. The faster we can develop concepts that improve the performance of our cars on the track, the better. The ProX 800 plays a big role in this effort because it enables us to produce parts efficiently and accurately during this development process."
3D Systems' extensive, integrated portfolio of additive manufacturing solutions - including materials, software, hardware and services - is enabling the transformation of digital manufacturing processes, and thus businesses. Through collaboration with its customers, 3D Systems continues to innovate, developing new materials and technologies to meet its customers' unique business needs.
"3D Systems' customer-specific, application driven approach is advancing the adoption of digital manufacturing," said Vyomesh Joshi, president and CEO, 3D Systems. "Our innovative materials and broad portfolio of hardware and software allows manufacturers to seamlessly integrate 3D printing into their production workflows. Our world-class experience and expertise, in collaboration with our industry-leading automotive customers, results in solutions that help them design and produce parts quickly, significantly reduce the product development cycle, drive down cost, and stay ahead of the competition."
About 3D Systems
More than 30 years ago, 3D Systems brought the innovation of 3D printing to the manufacturing industry. Today, as the leading additive manufacturing solutions company, it empowers manufacturers to create products and business models never before possible through transformed workflows. This is achieved with the Company's best-of-breed digital manufacturing ecosystem - comprised of plastic and metal 3D printers, print materials, on demand manufacturing services and a portfolio of end-to-end manufacturing software. Each solution is powered by the expertise of the company's application engineers who collaborate with customers to transform manufacturing environments. 3D Systems' solutions address a variety of advanced applications for prototyping through production in markets such as aerospace, automotive, medical, dental and consumer goods. More information on the company is available at www.3dsystems.com.
Featured Product
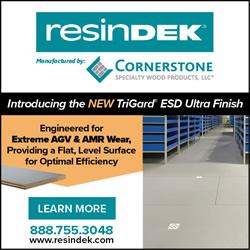