Bastian Solutions Launches New Robot Warehouse Picker with Parts Designed and Built Through Additive Manufacturing
Forty-five percent of the Bastian Solutions robotic arm is made using 3D printing parts produced at Fast Radius
Today, Bastian Solutions debuted the Bastian Solutions Shuttle System, a robotic materials handler with unparalleled efficiency and flexibility made possible with parts designed and built through additive manufacturing. The additive parts of the robotic Shuttle System—including the fingers, joints and elbow—are made with polymers, giving the robotic materials handler more dexterity and efficiency, as the lightweight material allows for a smaller motor and requires less power to execute its daily operations than with its previous metallic parts.
Bastian Solutions, a Toyota Advanced Logistics company, worked with Fast Radius to fully implement additive design and manufacturing into the Shuttle System. The additive parts for the product are made at Fast Radius' Chicago headquarters, one of the most advanced industrial-grade additive manufacturing facilities in North America. Forty-five percent of the final build-of-material (BOM) for the arm of the Bastian Solutions Shuttle System robotic picker will be produced using additive manufacturing. The parts are manufactured using HP Multi Jet Fusion 3D printers and Carbon® printers.
"We envisioned that additively manufacturing specific parts would make the Bastian Solutions Shuttle System the most efficient and agile robotic picker available on the market," said Ron Daggett, Vice President of Technology and R&D, Bastian Solutions. "The additive manufacturing process will enable us to customize each robot picker to fit a customer's particular warehouse environment."
Fast Radius' platform supports companies like Bastian Solutions in identifying potential applications, conducting engineering and economic evaluations, accelerating new product development, and ultimately manufacturing industrial-grade parts in Fast Radius factories at-scale with the latest additive technologies.
"Developing a new process for a robotic arm and using advanced additive materials to design lifelike fingers and joints is a reflection of Fast Radius' mission to ‘make new things possible,'" said Lou Rassey, Chief Executive Officer, Fast Radius. "The nature of additive manufacturing enabled us to create and test over a thousand prototype parts for Bastian Solutions in under 20 months until we arrived at just the right ones for this unique piece of equipment."
A portion of the Bastian Solutions Shuttle System's parts and prototypes, including the durable polymer joints that give the robotic arm its power and dexterity, were made with HP 3D printers using Multi Jet Fusion industrial-grade technology. Additional parts, including the proprietary fingers/gripper for the robotic arm were developed using Carbon's® Digital Light Synthesis™ (DLS™) technology and unique materials, notably EPU 40.
"Multi Jet Fusion is a viable solution for everything from prototyping and small-run 3D production to large-scale, full-production 3D manufacturing," said Michelle Bockman, global head of 3D printing commercial expansion and development, HP. "The genie has left the bottle on the adoption of industrial-scale 3D production, and it keeps accelerating."
"We're excited that Carbon DLS™ technology and innovative materials are playing a critical role in bringing the Bastian Solutions Shuttle System to market," said Dana McCallum, Head of Production Partners for Carbon. "Carbon DLS technology and EPU 40 resin made it possible for Fast Radius to manufacture a texture on the robot's finger that allows the robot to pick up any part, of any size. This couldn't have been achieved using traditional manufacturing methods and is a great example of what kind of innovation is possible with digital manufacturing, specifically Carbon DLS technology and unique materials."
Bastian Solutions will display the new additively manufactured Shuttle System at ProMat 2019, held April 8-11 at McCormick Place in Chicago.
Featured Product
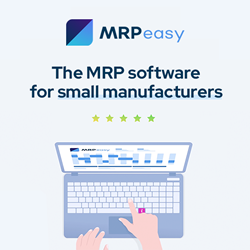