S.S. White Technologies Announces Custom Flexible Shafts for Automotive Applications
S.S. White Technologies, the worldwide leader in the design and manufacture of flexible shafts and related assemblies, announces their flexible shaft solutions for automotive industry applications. Flexible shafts are a technology that transmit rotary motion much like a solid shaft, but can be routed over, under, and around obstacles that would make using a solid shaft impractical.
S.S. White Technologies Announces Custom Flexible Shafts for Automotive Applications
St. Petersburg, FL - S.S. White Technologies, the worldwide leader in the design and manufacture of flexible shafts and related assemblies, announces their flexible shaft solutions for automotive industry applications. Flexible shafts are a technology that transmit rotary motion much like a solid shaft, but can be routed over, under, and around obstacles that would make using a solid shaft impractical. Flexible shafts are used in a variety of automotive applications, including in power seats, power sliding doors, pedal adjuster systems, and power rear lift gates, among others. S.S. White provides customers with custom flexible shaft solutions designed for specific applications, all backed by S.S. White's wealth of experience and expertise.
Among the many automotive applications for which S.S. White flexible shafts are used is to transmit rotary motion generated by electric motors in various "powered" amenities in vehicles. The most common application of S.S. White flexible shafts in this area is in power seats. This is one example of how flexible shafts can be widely customized to fit their application, as the shafts in this application are specialized "flocked" shafts, which are coated in flocked yarn to dampen the noise created during operation - a critical feature in the automotive industry. In addition, compared to the use of rigid shafts, flexible shafts used in power seats feature a number of advantages. The assembly process is easier with flexible shafts, and, due to their flexibility, flexible shafts give the movement of the power seats a greater degree of smoothness compared to rigid shafts.
Flexible shafts are the preferred rotary motion technology in many automotive applications because they help eliminate alignment problems, are less costly in terms of installation and needed parts, and they provide greater design freedom than rigid shaft technologies.
S.S. White provides flexible shaft assemblies as part of a custom solution. Every application in which a flexible shaft would be beneficial is different, and S.S. White not only manufactures the flexible shaft technologies, but also provides the technical expertise to create solutions to engineering challenges.
About S.S. White Technologies
S.S. White Technologies is a world leader in the design, engineering, manufacturing and testing of a variety of flexible shaft products for aerospace, medical, industrial and automotive markets. The majority of commercial and military aircraft platforms in the air today contain at least one S.S. White Technologies flexible rotary shaft, and more than one-half of US manufactured cars and second tier global automotive suppliers rely on S.S. White flexible rotary shafts. The company currently has design, engineering and manufacturing facilities in the United States and the United Kingdom, and manufacturing facilities in India. For more information, visit www.sswhite.net/
Featured Product
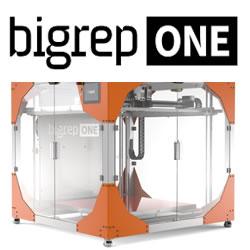
BigRep ONE: Large-Scale 3D Printing
The BigRep ONE is an award-winning, large-format 3D printer at an accessible price point. With over 350 systems installed worldwide, it's a trusted solution for prototyping and production by designers, innovators, and manufacturers alike. Featuring a massive one-cubic-meter build volume, the fast and reliable ONE brings your designs to life in full scale.