At SPS IPC Drives 2018, TE Connectivity shows how NFC chip integration in cable connectors can power Industry 4.0
In industrial use in the field, the NFC chips will put much more power in the hands of users, enabling them to obtain data through this web-based solution.
DARMSTADT, Germany - Nov. 27, 2018 - TE Connectivity (TE), a world leader in connectivity and sensors, will demonstrate the power of near field communications (NFC) technology in industrial connector applications at SPS IPC Drives 2018 in Nuremberg Nov. 27-29. NFC chips embedded in connectors on display on TE Booth 440 in Hall 10.0 will show visitors how to pick up important information from the connectors on smartphones (if it is NFC enabled) to on dedicated web pages. The technology is user-friendly and easy to access, as it can be used via several devices with the scan technic.
In industrial use in the field, the NFC chips will put much more power in the hands of users, enabling them to obtain data through this web-based solution. This allows for preventive maintenance to minimize risk of downtime in an Industry 4.0 environment. So that components and systems are connected to the Internet of Things (IoT) in an easy manageable way.
NFC chips in connectors will be able to provide two types of data: type data and instance data. Type data, typically available on a web page, relates to complete connector batches; it can include such things as 3D models, test reports and product datasheets. Instance data is unique to each connector: mating cycles, temperatures, cable age and so on.
"Connectors with NFC chips will help industrial companies respond to many new challenges they have to face if they want to make their factories truly smart," says Siegfried Funk, application manager, Motor Connectivity at TE Connectivity. "Among those challenges is the need to make manufacturing more flexible and production more efficient."
Data collection, aggregation, visualization and analytics that enable immediate data-driven decisions can help to overcome these challenges, Funk says. Data-driven decisions lead to greater efficiencies in how manufacturers use energy, raw materials, people and money, while increasing quality and flexibility. "It all starts with the connector, because so much information passes through it. If we can tap into that information, communicate it and record it, we are well on the way to the digital factory. Our goal is to transform the concept of the smart factory into an operational reality.
Smart connector technology, based on something as simple as an NFC chip, is a first step toward that goal. We work on this and align ourselves closely with the needs and visions of our customers," Funk says.
Whats more, smart connector solutions can verify the authenticity of hardware for easy registration management and they can reduce time needed for machine documentation and spare part management.
ABOUT TE CONNECTIVITY
TE Connectivity Ltd. is a $14 billion global technology and manufacturing leader creating a safer, sustainable, productive, and connected future. For more than 75 years, our connectivity and sensor solutions, proven in the harshest environments, have enabled advancements in transportation, industrial applications, medical technology, energy, data communications, and the home. With 80,000 employees, including more than 8,000 engineers, working alongside customers in approximately 140 countries, TE ensures that EVERY CONNECTION COUNTS. Learn more at www.te.com and on LinkedIn, Facebook, WeChat and Twitter.
Featured Product
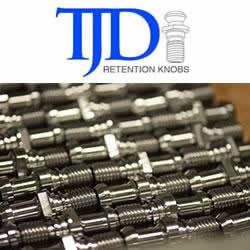