Piezo actuators – the driving force for additive manufacturing
Additive manufacturing is no longer simply a niche technique for rapid prototyping, and is establishing itself in industrial production.
Although injection moulding is still the method of choice for producing large volumes of plastic components, additive manufacturing is well suited to creating individual parts or small batches. It is being used across an increasingly diverse range of sectors - from automotive and consumer goods to medical technologies - as product lifecycles becomes shorter, model variations increase and the demand for individuality grows.
ARBURG GmbH and Co KG, a machine construction and engineering company in Lossburg, Germany, has developed a new process for additive manufacturing called ARBURG Plastic Freeforming (APF). This novel technique uses a PICMA® piezo actuator from Physik Instrumente (PI), a global leader in precision positioning technology. As with other additive manufacturing techniques, APF makes it possible to inexpensively produce a functional component layer-by-layer from a 3D model dataset. This technology can be used to integrate complex functions into a component, as well as producing more intricate geometries that cannot be achieved using conventional injection moulding. Droplet generation and discharge is central to the process, requiring synchronised motion between the printhead and other moving parts. Martin Neff, Group Manager for Sales and Freeform Plastics Technology at ARBURG, explained: "Our patented nozzle shutter - with high-frequency piezo technology - enables a fast opening and motion, generating around 200 droplets per second at a pressure of 500 bar. We decided to use a PICMA actuator for clocking the nozzle shutter because it provides the necessary accuracy and an excellent dynamic range of 90 µm. The discharge unit on our platform currently operates between 60 and 200 Hz, and we still have capacity in reserve."
Dr Cliff Jolliffe, Head of Segment Marketing for Automation at PI, commented: "The PICMAs microsecond response time is exceptionally fast, and no other valve technology offers similar speed in a comparable size. Im delighted that our technology is supporting the future of additive manufacturing."
Featured Product
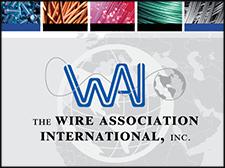